Saber® software simulates physical effects in different engineering domains (hydraulic, electronic, mechanical, thermal, etc.) as well as signal-flow algorithms and software control. Saber is used in the automotive, aerospace, power and IC industries to simulate and analyze systems, sub-systems and components under a variety of different operational and environmental conditions. This dramatically improves design reliability while reducing the need for physical prototypes.
Key features include the industry's largest model library, advanced analyses (Monte Carlo, Stress, Sensitivity, etc.) to support Robust Design methodologies, integration into popular design environments, and support for standard modeling languages including MAST and VHDL-AMS. Saber improves design productivity while helping engineers create more robust, reliable and cost-efficient designs faster.
Wire harness design is the backbone of the electrical system for any vehicle, whether automotive, aerospace, or other form of transportation. Mission critical, safety, infotainment, etc. signals are carried through a complex network of wires and harness assemblies to every portion of the vehicle. Saber Harness was developed in partnership with leading automotive and truck manufacturers to ensure production-proven harness designs for the most demanding environments. Combined with the industry-standard Saber simulation tool suite, Saber Harness helps streamline costs, reduce design time, and ensures signal-carrying capacity for all components throughout the vehicle.
Industries
Automotive Automotive
The Saber design environment is the proven standard in automotive design groups worldwide. Automotive engineers rely on Saber's unique analysis capabilities to insure robust and reliable designs. With Saber, engineers are able to analyze the interactions between the complex hardware and software technologies used in modern automotive systems. Saber includes the ability to analyze performance sensitivities and stresses, investigate system failure modes, and evaluate a design's reliability and manufacturability all in the same environment. Automotive applications where Saber is successfully used include in-vehicle networking, powernet management, drive-by-wire control, powertrain, engine regulation, and many more. Production-proven with advanced capabilities, Saber is the top choice for Automotive engineers seeking the advantages of robust design and analysis.
Aerospace Aerospace
Flight-critical systems must operate accurately and reliably in extreme environments. Therefore, Aerospace engineers must consider and thoroughly analyze a variety of factors when designing aircraft systems. The Saber design environment is the preferred choice for Aerospace engineers seeking robust system analysis. Engineers can investigate environmental effects such as changes in atmospheric pressure, temperature swings, etc. They can also evaluate changes in system performance resulting from manufacturing tolerance spreads (stack up) in system components. Saber also allows engineers to inject failures in their designs to see how the rest of the system is affected. Aerospace applications where Saber is successfully used include fly-by-wire control, power network sizing and validation, radar and flight control computers, hydraulic power generation and distribution, and many others. Saber is the only tool that can deliver advanced analysis critical to the demanding safety and reliability requirements inherent in today’s Aerospace industry.
2007-11-29
2007-11-27
Cadence IC6.11 design for Linux

Personal consumer electronics and wireless products have become the dominant force in today's global electronics market. And relentless demand for new features and functionality in these devices is driving unprecedented growth in RF, analog, and mixed-signal applications. To create new products that fulfill this demand, IC designers must manipulate precise analog quantities—voltages, currents, charges, and continuous ratios of parameter values such as resistance and capacitance. This is when companies turn to custom design.
Full-custom design maximizes performance while minimizing area and power. However, it requires significant handcrafting by a select set of engineers with very high skill levels. In addition, custom analog circuits are more sensitive to physical effects, which are exacerbated at new, nanometer process nodes. To streamline the process of designing custom ICs and integrating them into end products, semiconductor and systems companies need sophisticated software and flow methodologies to meet time-to-market and time-to-volume goals. The Cadence Virtuoso custom design platform provides an exceptionally fast and silicon-accurate way to design custom analog, RF, and mixed-signal ICs.
2007-11-24
Agilent.Genesys.v.2007.08

Agilent Technologies Inc. (NYSE: A) today announced the availability of GENESYS 2007, a new release of its popular RF and microwave design software in Agilent's Eagleware product line. The release includes improvements to simulation, tuning, optimization and integration through file-format export. The improvements help boost designers' confidence in circuit performance and speed the communications-design process.
"We're pleased to be shipping this high-performance and high-quality release," said Frank Vincze, product manager with Agilent's EEsof EDA division. "Early feedback from customers indicates we've hit the right balance of performance and technology that can cut development time and reduce or eliminate design turns."
Improvements and new features of Agilent's GENESYS 2007 release include:
* Improved performance: Faster and more accurate simulation, tuning and optimization
* New statistical yield analyses: Save and compare iterative results
* Improved intermediate file format (IFF) interface: Smoother export of GENESYS models into Agilent's industry-leading Advanced Design System (ADS) for more advanced simulations that get you closer to design implementation
* Expanded support for mixer spur tables in WhatIF: Use hardware-measured mixer models, with their range of frequency responses, to define operating frequencies
* Integrated ADS licensing: A common licensing protocol between GENESYS and ADS eliminates the need for a physical hardware key
GENESYS is an integrated and easy-to-use software suite with leading price performance for use in Windows PC environments. It supports a full range of communications design, from algorithms to artwork. GENESYS circuit-design software is used to develop products such as cellular telephones, radar systems, cable TV systems, satellite systems, mobile base-station equipment, Radio Frequency Identification (RFID) devices and wireless networking products. GENESYS also is used in high-frequency applications such as system-architecture design and analysis, linear simulation, non-linear and electromagnetic simulation, synthesis, and RF-board and microwave-IC layout.
2007-11-23
Advanced-Design-System-(ADS)-V2008 (c)Agilent
Agilent Technologies Inc. (NYSE: A) today announced Advanced Design System release 2008. Advanced Design System (ADS) is an industry-leading high-frequency, high-speed electronic design automation (EDA) software platform. This release contains productivity breakthroughs for faster communications product design.
"Working closely with our top customers, we've enhanced this ADS release with user interface and technology improvements that speed the design process," said Jim McGillivary, general manager of Agilent's EEsof EDA division. "In 2008, I am challenging my development team to double customer productivity for a comprehensive set of typical design tasks, which we'll publish and track on our Web site."
Advanced Design System 2008's advanced, graphical user interface enhancements come from the same interface development platform used by the most popular Internet software tools and search engines, and contain advanced search and context-dependent features. The speed improvements gained from this new interface help make software-tools integration seamless for common and emerging design applications.
Speed and productivity enhancements include:
* improved project management, real-time zoom and pan, interactive 3-D layout viewing, stretching, and cut planes;
* improved LVS (layout vs. schematic) design synchronization, providing full control over the automation to guarantee the correct layout;
* updated design rule checking and fast, accurate artwork export/import for a smoother transition from design to production;
* full 3-D electromagnetic integration into ADS, for designers who increasingly need electromagnetic analysis for complete communications product design. The integrated Electromagnetic Design System also contains a faster bond wire drawing interface;
* the latest multi-processor computing, including support for today's 64-bit processors; and
* faster high-frequency Transient simulations, providing average speed improvements of up to 6x for large circuits.
Because high-speed digital designers are now facing the same physical design challenges that Agilent's EDA design tools have addressed for RF and microwave design, Advanced Design System 2008 features full support for high-speed, gigabit link (signal integrity) design, including advanced bit error rate measurement and analysis.
This is first in a series of four ADS releases expected in 2008. By the end of the year, Agilent plans to double productivity for common design and simulation tasks compared with previous versions of ADS.
"Working closely with our top customers, we've enhanced this ADS release with user interface and technology improvements that speed the design process," said Jim McGillivary, general manager of Agilent's EEsof EDA division. "In 2008, I am challenging my development team to double customer productivity for a comprehensive set of typical design tasks, which we'll publish and track on our Web site."
Advanced Design System 2008's advanced, graphical user interface enhancements come from the same interface development platform used by the most popular Internet software tools and search engines, and contain advanced search and context-dependent features. The speed improvements gained from this new interface help make software-tools integration seamless for common and emerging design applications.
Speed and productivity enhancements include:
* improved project management, real-time zoom and pan, interactive 3-D layout viewing, stretching, and cut planes;
* improved LVS (layout vs. schematic) design synchronization, providing full control over the automation to guarantee the correct layout;
* updated design rule checking and fast, accurate artwork export/import for a smoother transition from design to production;
* full 3-D electromagnetic integration into ADS, for designers who increasingly need electromagnetic analysis for complete communications product design. The integrated Electromagnetic Design System also contains a faster bond wire drawing interface;
* the latest multi-processor computing, including support for today's 64-bit processors; and
* faster high-frequency Transient simulations, providing average speed improvements of up to 6x for large circuits.
Because high-speed digital designers are now facing the same physical design challenges that Agilent's EDA design tools have addressed for RF and microwave design, Advanced Design System 2008 features full support for high-speed, gigabit link (signal integrity) design, including advanced bit error rate measurement and analysis.
This is first in a series of four ADS releases expected in 2008. By the end of the year, Agilent plans to double productivity for common design and simulation tasks compared with previous versions of ADS.
2007-11-22
OPTISWORKS-V2008 FOR SOLIDWORKS-2008 (C)OPTIS

• Simultaneously optimize optical and mechanical parts thanks to powerful optimization engine
• Import all optical systems created with traditional software
• Study tolerancing of your system thanks to multi-configuration capabilities
• Treat optical rays as 3D sketches
• Access a full set of optical components libraries
• Calculate all optical performances of your system (MTF, PSF, Spot diagrams, Aberrations…)
• Reduce system size thanks to free shape lens design & optimization
New functionalities
Virtual Human Vision Lab: Visual acuity, Condition of observation of the scene and Vision mode evaluation.
Virtual Human Vision Lab: Analysis tools.
Virtual Human Vision Lab: Legibility/Visibility tools.
ANSI/IESNA LM-63-2002 standard support.
ANSI/IESNA LM-63 Type A standard support.
Virtual Photometric Lab: Following operations on maps are now multithreaded: Open, Standard filtering, Remove highest peaks filtering, Map addition and multiplication by a value (Photometric Calc and Distributed calculation), Surface/Section calculations and Display update.
New OPTIS License Manager.
Virtual Photometric Lab: The export of spectral map to convert it into an extended map has been added.
Advanced Scattering Surface: The Autofill tool has been added to help the Advanced scattering generation.
Improvements
Availability of preferences from independent Labs: Virtual Photometric Lab, Virtual Human Vision Lab, User Material Editor, Spectrum Editor, Advanced Scattering Surface Editor and BSDF - BRDF - Anisotropic Surfaces Viewer.
IES / Eulumdat / Optis Intensity viewers: Horizontal symmetry and intensity's export to a Virtual Photometric map.
IESNA viewer: Graphic user interface for "Miscellaneous".
Sollner curve and Luminance calculation only available for IES C format.
Eulumdat viewer: Possibility to add symmetry properties on an existing intensity diagram (CAS-01655-1BEXMM).
Virtual Human Vision Lab: New Time adaptation dialog box.
Virtual Photometric Lab: Eye Illuminance.
Virtual Photometric Lab: Colorimetric data - Possibility to select a reference color and to calculate the DeltaE between the reference color and the selected color.
Rebuilt of the "Complete Scattering" model.
"Measure Treatment" feature added to the "BSDF - BRDF - Anisotropic Surfaces Viewer" to allow post-treatment of measured files.
Fixed bugs
Virtual Photometric Lab: BMP mask import has been fixed (CAS-01573-49SKT9).
Virtual Photometric Lab: The "Remove highest peaks" filtering has been corrected for radiometric values (CAS-01647-ZNBTWK).
Virtual Photometric Lab: The crash with grid parameters has been solved.
Virtual Photometric Lab: The crash when a not well written CLS file has been chosen as been solved.
Virtual Photometric Lab: The txt Import/Export command for a conoscopic map has been solved.
Virtual Photometric Lab: Saved of values for points' position of the "user line" of a conoscopic map has been solved.
Virtual Photometric Lab: The flux value when using Foot Candle has been solved (CAS-01913-AYLLNF).
When opening a Virtual Photometric Lab, the default filter with highest peaks remove has been solved.
User Material Editor: Units of the spectrum editor for fluorescence materials' absorption has been fixed (CAS-01548-DW70C2).
User Material Editor: It is not more possible to enter an index below than 1.0.
User Material Editor: A problem when displaying the index graph with very low variation of the index has been fixed.
Ray File Editor: The "Save As" command has been fixed (CAS-01929-X4J8HA).
Lambda minimum limitation for Spectrum Generation has been solved.
IESNA LM-63 Type B: The measured flux has been solved.
• Limit number of optical elements in your opto-mechanical systems
Essential Macleod v8.15.174
The Essential Macleod program contains all the essentials for the design and performance calculation of optical coatings. In particular it will calculate a wide range of performance parameters of a given coating design including the usual reflectance and transmittance magnitude and phase, but also color, ultrafast, ellipsometric quantities and from the zero’th up to the third derivative as a function of wavelength. It will estimate the effects of random errors in the layers. It will refine existing designs to improve their performance and it will synthesize designs that start with virtually no instructions other than the materials to be used and the performance that is targeted. It includes allowance for layer packing density. It has powerful design editors to make it very easy to create or change even the most complex designs. It also maintains the files that contain the optical constants of materials. The Essential Macleod will also calculate performance of series of different substrates, with or without associated coatings and it will perform a wide range of analytical functions such as generating admittance diagrams and electric field distributions. It has a completely flexible system of variable units.
The Essential Macleod is equipped to export coating designs to the ZEMAX and Code V optical design packages, It will also export performance to the LinkSIM simulation tool.
Optional enhancements add a virtually limitless range of possible performance functions, run sheets and monitoring curves with links to thin film monitors.
The package is an integrated whole with the operation controlled almost entirely from menus. The menu commands are designed to permit the user to indicate what has to be done without needing to indicate how. To calculate an aspect of performance, for example, the user simply tells the package to produce a plot or a table. The underlying operation and organization is completely automatic. The description that follows, therefore, concentrates on the menu commands, what they are and what they do. It is purely a description of the operation of the software package. It does not go into details of the calculation techniques nor does it discuss design technique
The Essential Macleod uses a Multiple Document Interface (MDI). A document can be a plot, a table, a design, a list of materials and so on. Multiple Document Interface means that many documents may be displayed at once, the total number being limited by the capabilities of the computer and of the Windows installation. One document at a time is active. The menu bar changes as the active document changes so that the menu commands always apply to whichever of the open documents is the active one. For example, if a plot is active then the Edit menu will apply to the plot and will permit such things as changing the parameters of the axes. The user will find that it is often useful to be able to keep several designs open simultaneously. Should the capacity of Windows or of the computer be exceeded then the user will simply be requested to reduce the number of open documents. There is no need constantly to keep track of what is open. We do recommend, however, that unnecessary documents should be closed to avoid clutter.
Throughout the operation of the package, designs and specifications are saved to various files. The principal files are known as design files and they contain not just the sequence of layers but also the calculation parameters that should be used to evaluate the design. If a design is passed to refinement, the refinement specification also becomes part of the design file. The operation of saving the design and parameters can be manually performed at any time by choosing the appropriate menu item but it is also automatically initiated at those stages where there is a danger that something might otherwise be lost. In spite of this automatic feature, we do recommend that the user acquire the habit of saving the work at intervals. In particular when moving from one design to another it often seems convenient just to write the new design over the old. However, if the existing design is important the editing process will change it perhaps beyond recovery. No automatic save is initiated whenever a design is edited - editing is a very simple and straightforward process. Before beginning major editing, where a design is going to be substantially altered, it is good practice to save the design twice, once in the existing design file, thereby preserving the current design for later recall, and once in a new design file, which can then be edited without fear of changing the original. You may find this approach useful in other applications such as word processors also.
In the Essential Macleod the optical constant information for the thin film materials is kept in separate files in one or more materials databases. In the designs, the materials of the films and substrate are referred to explicitly by name (normally the chemical formula). A material database consists of a set of materials files together with control files that are kept in a separate folder, the path being the identifier for the database. Many different material databases may exist together. This is a particularly useful feature of the Essential Macleod and we encourage the user to make full use of it. Separate databases could be used, for example, for infrared materials as distinct from visible materials with wavelength stated in microns rather than nanometres. Alternatively, different databases could be used for different customers or for different plants or processes. In order to keep track of the particular database that was used to generate a design, information on both the database and the number/name conversion for the materials used, is stored in each design file. This information is compared with the existing database when a design file is read and only if an exact match is found can the calculations proceed without intervention. The material database can easily be changed but only when there are no open documents. The General command in the Options menu opens the form that contains the necessary command for changing the material database. A number of facilities are provided to simplify the maintenance of many different material databases. These are described later in the manual.
The Essential Macleod is equipped to export coating designs to the ZEMAX and Code V optical design packages, It will also export performance to the LinkSIM simulation tool.
Optional enhancements add a virtually limitless range of possible performance functions, run sheets and monitoring curves with links to thin film monitors.
The package is an integrated whole with the operation controlled almost entirely from menus. The menu commands are designed to permit the user to indicate what has to be done without needing to indicate how. To calculate an aspect of performance, for example, the user simply tells the package to produce a plot or a table. The underlying operation and organization is completely automatic. The description that follows, therefore, concentrates on the menu commands, what they are and what they do. It is purely a description of the operation of the software package. It does not go into details of the calculation techniques nor does it discuss design technique
The Essential Macleod uses a Multiple Document Interface (MDI). A document can be a plot, a table, a design, a list of materials and so on. Multiple Document Interface means that many documents may be displayed at once, the total number being limited by the capabilities of the computer and of the Windows installation. One document at a time is active. The menu bar changes as the active document changes so that the menu commands always apply to whichever of the open documents is the active one. For example, if a plot is active then the Edit menu will apply to the plot and will permit such things as changing the parameters of the axes. The user will find that it is often useful to be able to keep several designs open simultaneously. Should the capacity of Windows or of the computer be exceeded then the user will simply be requested to reduce the number of open documents. There is no need constantly to keep track of what is open. We do recommend, however, that unnecessary documents should be closed to avoid clutter.
Throughout the operation of the package, designs and specifications are saved to various files. The principal files are known as design files and they contain not just the sequence of layers but also the calculation parameters that should be used to evaluate the design. If a design is passed to refinement, the refinement specification also becomes part of the design file. The operation of saving the design and parameters can be manually performed at any time by choosing the appropriate menu item but it is also automatically initiated at those stages where there is a danger that something might otherwise be lost. In spite of this automatic feature, we do recommend that the user acquire the habit of saving the work at intervals. In particular when moving from one design to another it often seems convenient just to write the new design over the old. However, if the existing design is important the editing process will change it perhaps beyond recovery. No automatic save is initiated whenever a design is edited - editing is a very simple and straightforward process. Before beginning major editing, where a design is going to be substantially altered, it is good practice to save the design twice, once in the existing design file, thereby preserving the current design for later recall, and once in a new design file, which can then be edited without fear of changing the original. You may find this approach useful in other applications such as word processors also.
In the Essential Macleod the optical constant information for the thin film materials is kept in separate files in one or more materials databases. In the designs, the materials of the films and substrate are referred to explicitly by name (normally the chemical formula). A material database consists of a set of materials files together with control files that are kept in a separate folder, the path being the identifier for the database. Many different material databases may exist together. This is a particularly useful feature of the Essential Macleod and we encourage the user to make full use of it. Separate databases could be used, for example, for infrared materials as distinct from visible materials with wavelength stated in microns rather than nanometres. Alternatively, different databases could be used for different customers or for different plants or processes. In order to keep track of the particular database that was used to generate a design, information on both the database and the number/name conversion for the materials used, is stored in each design file. This information is compared with the existing database when a design file is read and only if an exact match is found can the calculations proceed without intervention. The material database can easily be changed but only when there are no open documents. The General command in the Options menu opens the form that contains the necessary command for changing the material database. A number of facilities are provided to simplify the maintenance of many different material databases. These are described later in the manual.
2007-11-21
ESI.PROCAST.V2007

We are proud to announce, only six months after the previous release, a new release of ProCAST 2007, the leading finite element software package for foundry simulation.
This new version brings additional new features in meshing, processing capabilities, viewing and numerous improvements in product performance.
The ProCAST solutions include automatic mesh generation, thermal analysis with radiation effects, flow analysis for mould filing, fully coupled thermal, flow and stress analysis and advanced metallurgical options.
The following main improvements deserve to be highlighted (for more information, please contact your ESI Group’s representative).
SOLVERS
True 64 bits executables for ProCAST solvers are now available on Windows for both scalar and DMP versions (64 bits executables are available on Linux, as before).
ASSEMBLY
The assembly algorithm was improved in order to be more automatic and powerful.
FADING
Nodular cast iron (SGI) is obtained by a Mg treatment of the melt. The graphite formation tends to diminish as the interval between the treatment and the solidification increases (fading effect). As a consequence, the expansion effect will be reduced as graphite formation is decreasing. This will of course have an effect on the amount of porosity. ProCAST 2007 integrates the modeling of graphite fading in SGI and therefore allows better porosity modeling.
One illustration of this new model is presented above for two extreme cases: on the left the FADING value is one while on the right the FADING value is zero. It is seen that in this latter case the porosity is decreased to zero.
PARALLEL PROCESSING
Continuous efforts are being devoted to improve the scalability, repeatability and availability on various platforms of the ProCAST DMP solver. The following improvements have been made in ProCAST 2007:
The Microstructure module is now available in the DMP solver,
The Freckle calculation is now available in the DMP solver,
The Core blowing option is now available in the DMP,
Improved performance of the stress parallel solver,
Improvements in lost foam modeling and interpenetrating mesh option.
CORE BLOWING
ProCAST allows now improved modeling of the core blowing process. When modeling the sand injection process, the air and sand are modeled as a homogeneous fluid in which the air-sand mixture is treated as a single phase. Thus, the process is considered as a filling with ad-hoc material properties and boundary conditions.
FLUID FRONT TRACKING
The "Fluid Front Tracking indicator" is based on an algorithm which is calculating in the solver the tracking of the free surface front. This allows identifying the locations where oxides and impurities trapped at the free surface are most likely to end-up as
2007-11-20
ADINA-v8.4.2 (c)Adina
The ADINA System consists of the following modules:
ADINA-AUI The ADINA User Interface program (AUI) provides complete pre- and post-processing capabilities for all the ADINA solution programs.
ADINA-M The ADINA Modeler (ADINA-M) is an add-on module to ADINA-AUI that provides solid modeling capabilities and direct integration with all other Parasolid-based CAD systems.
ADINA The premium finite element program for linear and highly nonlinear analyses of solids and structures.
ADINA-F CFD program for the analysis of compressible and incompressible flow with state-of-the-art capabilities for moving boundaries and automatic remeshing.
ADINA-T Module for the heat transfer analysis of solids and field problems.
ADINA-FSI The ADINA-FSI (fluid structure interaction) program is the leading code used by industries for fully coupled analysis of fluid flow with structural interaction problems. This module is available to users who license both the ADINA and ADINA-F modules.
ADINA-TMC This module provides capabilities for thermo-mechanical coupled (TMC) analysis, including analysis of contact with heat transfer. By licensing both the ADINA and ADINA-T modules, the user automatically has access to this module.
CAD Interfaces Through ADINA-M, users can directly import Parasolid-based (e.g., Unigraphics, SolidWorks, and SolidEdge) CAD geometry. We also provide interface programs to major systems such as
I-DEAS and MSC.Patran. Where a direct interface is currently not available (e.g., CATIA), the geometry can
ADINA-AUI The ADINA User Interface program (AUI) provides complete pre- and post-processing capabilities for all the ADINA solution programs.
ADINA-M The ADINA Modeler (ADINA-M) is an add-on module to ADINA-AUI that provides solid modeling capabilities and direct integration with all other Parasolid-based CAD systems.
ADINA The premium finite element program for linear and highly nonlinear analyses of solids and structures.
ADINA-F CFD program for the analysis of compressible and incompressible flow with state-of-the-art capabilities for moving boundaries and automatic remeshing.
ADINA-T Module for the heat transfer analysis of solids and field problems.
ADINA-FSI The ADINA-FSI (fluid structure interaction) program is the leading code used by industries for fully coupled analysis of fluid flow with structural interaction problems. This module is available to users who license both the ADINA and ADINA-F modules.
ADINA-TMC This module provides capabilities for thermo-mechanical coupled (TMC) analysis, including analysis of contact with heat transfer. By licensing both the ADINA and ADINA-T modules, the user automatically has access to this module.
CAD Interfaces Through ADINA-M, users can directly import Parasolid-based (e.g., Unigraphics, SolidWorks, and SolidEdge) CAD geometry. We also provide interface programs to major systems such as
I-DEAS and MSC.Patran. Where a direct interface is currently not available (e.g., CATIA), the geometry can
2007-11-19
DYNAFORM V5.6 (c)ETA
DYNAFORM Version 5.6 release note:
The release of DYNAFORM Version 5.6 contains many enhancements that certainly improve your stamping design and development capabilities. Some of the major improvements include:
Enhanced Pre Processor Functions:
1. New layout for line functions from CREATE, DELETE, EDIT/MODIFY, TRANSFORM to DISLAY. Integrate TRANTSLATE, ROTATE, MIRROR and SCALE in one dialog. Translate line can be completed from LCS to LCS.
2. New layout for surface functions from CREATE, DELETE, EDIT/MODIFY, TRANSFORM to DISPLAY. Integrate TRANTSLATE, ROTATE, MIRROR and SCALE in one dialog. Translate surface can be completed from LCS to LCS.
3. Add Mesh to Surface function. User can create surfaces from mesh.
4. Add brand new Extend Surface function. User can expand untrimmed surfaces.
5. Add brand new Check Surface function.
6. New layout for Element functions from CREATE, DELETE, EDIT/MODIFY, TRANSFORM to DISPLAY. Integrate TRANTSLATE, ROTATE, MIRROR and SCALE in one dialog. Translate element can be completed using LCS to LCS.
7. Drag Mesh function is updated. Thick Shell or Solid Elements are created using this function.
8. Add Trim Element function in Element dialog box. The user can select one or several trim lines to trim elements.
9. Add Lance Element function in Element dialog box.
10. New layout for Node functions from CREATE, DELETE, EDIT/MODIFY, TRANSFORM to DISPLAY. Integrate TRANTSLATE, ROTATE, MIRROR and SCALE in one dialog. Translate node can be completed using LCS to LCS.
11. Add brand new Check function to check the deviation between surface and mesh.
Improved Blank Size Engineering Module:
1. Develop special GUI for the Trimline development.
2. Support Multi-step Unfold function.
3. Enhanced Middle and Group surface functions.
4. Improved Blank Development function.
Redesign Die Face Engineering Module:
1. Improved DFE Preparation GUI.
2. Add Double Attach function.
3. Allow input for pre-designed binders.
4. Improve Surface Edit function. User can easily edit surfaces.
5. Add Side-Step function to allow user to easily fill end of geometry.
6. Inner Fill function is improved with Control Line.
7. Element Morphing function is improved. Over crown can be easily created.
8. Binder function has been improved to support 2-D binder shape edition. User can
select Reference Line feature line to edit the control line in the 2-D edition dialog.
9. Add brand new Flange On Binder function.
10. Add brand new Butterfly Binder function.
11. Addendum function is improved.
12. Binder trim function is improved.
Enhanced Setup Module:
1. Support Geometry offset and Contact offset.
2. Support Multi-stage stamping in one setup for line die simulation.
3. Add QuickSetup GUI for Tube Rotary Bending.
4. Support Super Plastic Forming simulation.
5. Support Solid/Tshell blank element.
6. Support Thermal Forming Simulation. Add thermal solver parameters and thermal material models.
7. Material Library is improved. User can easily define his/her material library.
8. Improve Blank Trim function. User can trim inner boundary and outer boundary.
Springback Compensation (SCP) Module:
1. Add brand new Springback Compensation module.
2. Add SCP solver.
New Post Processor Features:
1. Improved the index file. Index File Transfers Part Name, Blank Material, FLD, Bead Information and multi-stage information to the Post-processor.
2. User Defined Contour function is added. User can Create, Modify and Delete User Defined Component.
3. FLD plots can be scaled.
4. Interface Pressure can be checked.
5. Face Reflection Function is improved. Face Reflection simulation using several light strips to check smooth surface. Distorted light strips indicate surface’s curvature is uneven.
6. Brand new Tool Wear function. All necessary data needed for wear depth calculation are supplied from the LS-DYNA interface force database file (d3plotint). The tool wear interface is displayed after opening d3plotint file.
7. Add brand new Painted blank function. User can paint the select pictures on the deformed blank.
8. Support plot and animate thickness and thinning for Solid and Tshell Element.
9. Support process multi-stage simulation result.
The release of DYNAFORM Version 5.6 contains many enhancements that certainly improve your stamping design and development capabilities. Some of the major improvements include:
Enhanced Pre Processor Functions:
1. New layout for line functions from CREATE, DELETE, EDIT/MODIFY, TRANSFORM to DISLAY. Integrate TRANTSLATE, ROTATE, MIRROR and SCALE in one dialog. Translate line can be completed from LCS to LCS.
2. New layout for surface functions from CREATE, DELETE, EDIT/MODIFY, TRANSFORM to DISPLAY. Integrate TRANTSLATE, ROTATE, MIRROR and SCALE in one dialog. Translate surface can be completed from LCS to LCS.
3. Add Mesh to Surface function. User can create surfaces from mesh.
4. Add brand new Extend Surface function. User can expand untrimmed surfaces.
5. Add brand new Check Surface function.
6. New layout for Element functions from CREATE, DELETE, EDIT/MODIFY, TRANSFORM to DISPLAY. Integrate TRANTSLATE, ROTATE, MIRROR and SCALE in one dialog. Translate element can be completed using LCS to LCS.
7. Drag Mesh function is updated. Thick Shell or Solid Elements are created using this function.
8. Add Trim Element function in Element dialog box. The user can select one or several trim lines to trim elements.
9. Add Lance Element function in Element dialog box.
10. New layout for Node functions from CREATE, DELETE, EDIT/MODIFY, TRANSFORM to DISPLAY. Integrate TRANTSLATE, ROTATE, MIRROR and SCALE in one dialog. Translate node can be completed using LCS to LCS.
11. Add brand new Check function to check the deviation between surface and mesh.
Improved Blank Size Engineering Module:
1. Develop special GUI for the Trimline development.
2. Support Multi-step Unfold function.
3. Enhanced Middle and Group surface functions.
4. Improved Blank Development function.
Redesign Die Face Engineering Module:
1. Improved DFE Preparation GUI.
2. Add Double Attach function.
3. Allow input for pre-designed binders.
4. Improve Surface Edit function. User can easily edit surfaces.
5. Add Side-Step function to allow user to easily fill end of geometry.
6. Inner Fill function is improved with Control Line.
7. Element Morphing function is improved. Over crown can be easily created.
8. Binder function has been improved to support 2-D binder shape edition. User can
select Reference Line feature line to edit the control line in the 2-D edition dialog.
9. Add brand new Flange On Binder function.
10. Add brand new Butterfly Binder function.
11. Addendum function is improved.
12. Binder trim function is improved.
Enhanced Setup Module:
1. Support Geometry offset and Contact offset.
2. Support Multi-stage stamping in one setup for line die simulation.
3. Add QuickSetup GUI for Tube Rotary Bending.
4. Support Super Plastic Forming simulation.
5. Support Solid/Tshell blank element.
6. Support Thermal Forming Simulation. Add thermal solver parameters and thermal material models.
7. Material Library is improved. User can easily define his/her material library.
8. Improve Blank Trim function. User can trim inner boundary and outer boundary.
Springback Compensation (SCP) Module:
1. Add brand new Springback Compensation module.
2. Add SCP solver.
New Post Processor Features:
1. Improved the index file. Index File Transfers Part Name, Blank Material, FLD, Bead Information and multi-stage information to the Post-processor.
2. User Defined Contour function is added. User can Create, Modify and Delete User Defined Component.
3. FLD plots can be scaled.
4. Interface Pressure can be checked.
5. Face Reflection Function is improved. Face Reflection simulation using several light strips to check smooth surface. Distorted light strips indicate surface’s curvature is uneven.
6. Brand new Tool Wear function. All necessary data needed for wear depth calculation are supplied from the LS-DYNA interface force database file (d3plotint). The tool wear interface is displayed after opening d3plotint file.
7. Add brand new Painted blank function. User can paint the select pictures on the deformed blank.
8. Support plot and animate thickness and thinning for Solid and Tshell Element.
9. Support process multi-stage simulation result.
IMAGINE.AMESim.v4.3
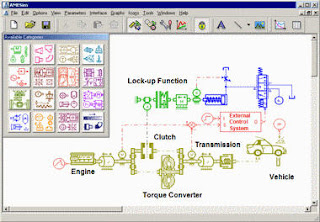
A graphical environment for modeling, simulation and analysis of dynamic engineering systems, AMESim is based on a large set of validated libraries issued from different physical domains. AMESim allows you to access rapidly the ultimate goal of modeling: the analysis and optimization of your design.
Focusing on physics, AMESim frees the engineer from numerical aspects. The basic element concept, which lies behind each model, provides basic engineering elements that can be combined to describe all functions of the component or system in the model. Thereby, engineers don't have to worry about code writing.
User Interface
The AMESim graphical interface enables the user to build complex models by choosing among a collection of components. The resulting sketch is then easily understandable, as close as possible to what a design engineer could expect. Various levels of models can be selected for each component.
The user can also set parameters and units in a friendly way. The modeling process divided into four modes (build sketch, select model complexity, set parameter and finally, run simulations and perform analysis) enables the user to work quickly and efficiently.
Multi-domain system design
The AMESim platform provides a simulation environment for multi-domain system design with a large set of libraries covering multiple domains and applications. Focusing on physics, AMESim offers both a structured multiport approach for the modeling of physical systems and a block diagram approach for control systems. This effective and clear concept for communication of model information provides a clear-cut technique to model physical systems, capture and re-use engineering knowledge, and finally to greatly facilitate the sharing of engineering efforts.
Key Points
Adaptability & Reusability
Multi-domain simulation platform
Structured libraries of physical models
Various model complexity levels
Designed to capitalize and share know-how
Comprehensive documentation
Open Platform
Interface with CAE software such as Matlab®, Simulink®, Flux® or in-house code
C Code generation
Access to library's source code
Cross platform: Windows, UNIX and Linux
Unrivaled Numerical Core
Automatic and adaptive selection of the integration method
Discontinuity handling
Model linearization
Advanced Features
Sensitivity analysis
Parametric study analysis
FFT and Linear analysis
HTML report generator
Animation
2007-11-16
Comsol-Multiphysics-V3.4

COMSOL Multiphysics 3.4 provides fully parallelized meshing for assemblies straight out of the box. A new boundary layer meshing feature in version 3.4 enables users to mesh thermal boundary layers, charged double-layers in AC/DC applications, or viscous boundary layers in fluid-flow applications more efficiently, with greater accuracy, and with less memory consumption than previously possible.
A major upgrade to COMSOL Multiphysics’s iterative methods pushes solver performance for fluid dynamics to new heights. For example, new, state-of-the-art Galerkin Least Squares (GLS) stabilization techniques now complement COMSOL’s iterative solvers, enabling engineers and scientists to compute large fluid flow problems with millions of degrees of freedom. A segregated solver with an easy-to-use interface, new in version 3.4, reduces memory consumption significantly when computing large problems, such as fluid-structure interaction (FSI) or wave propagation in thermally deformed structures. When compared to its predecessors, COMSOL Multiphysics 3.4 solves fluid-flow problems up to five times faster.
COMSOL Multiphysics 3.4 also offers users a new suite of postprocessing tools for computing geometric properties such as volume, area, center of gravity, and moment of inertia. Even simulation results can be presented in exciting new ways with version 3.4’s expanded palette of color scales.
Multiphase flow and free convection in the Chemical Engineering and Heat Transfer Modules
Users of the COMSOL Chemical Engineering and Heat Transfer Modules can now step up their simulations to include variable-density flow and free convection. Engineers will find these new capabilities particularly useful when solving coupled flow and conjugate heat transfer problems commonly encountered in electronic cooling and heat exchanger analyses. For applications such as microfluidics, multi-species convection, and reacting flows, COMSOL Multiphysics 3.4 has been enhanced with additional multiphysics modeling interfaces for turbulent and laminar flow with variable densities due to variations in composition.
The Chemical Engineering Module has been improved with a powerful modeling interface for the simulation of multiphase flow. With it, users can now simulate bubbly flows such as in scrubbers, aerators, bioreactors, and food-processing equipment effortlessly. Users can also easily set up mixture models for simulating emulsification, sedimentation, and other separation processes common in the chemical, pharmaceutical, and food-processing industries.
The Heat Transfer Module has been greatly enhanced by the introduction of boundary layer meshing and by improvements to COMSOL’s solver technology. Boundary layer meshing provides engineers and scientists with greater accuracy yet requires fewer elements for simulating electronic cooling, heat exchangers, and heat losses to solid structures in mechanical design. Also new in the Heat Transfer Module is the ability to model 3D surface-to-surface radiation using the memory-saving 2D axisymmetric modeling domain.
Parameter estimation in COMSOL Reaction Engineering Lab
Upgrades to the COMSOL Reaction Engineering Lab® include a powerful new interface for running nonlinear parameter estimations on multiple sets of experimental data. In addition, it is now possible to select which parameters to estimate and which parameters to keep constant in each estimation run. Outputs now display with confidence intervals and standard deviations.
SPICE import in the AC/DC Module and new lumped ports in the RF Module
Version 3.4 makes it easy to build and run COMSOL models as part of SPICE-based circuit simulations thanks to the AC/DC Module’s new SPICE user interface. Another exciting new feature for electronics, electrical components, geophysics, and electrochemistry applications is small-signal analysis for AC impedance studies. Users can also easily model electric motors and generators through a new interface supporting periodic boundary conditions and sector symmetry. Additionally, a new periodic boundary condition user interface has been introduced in the RF Module along with an improved interface for lumped port boundary conditions, which is ideal for wave propagation in transmission lines and circuit boards.
Fatigue analysis enhances the Structural Mechanics Module
The COMSOL Multiphysics Structural Mechanics Module now lets users predict high- and low-cycle fatigue damage. A suite of COMSOL Script functions calculate fatigue damage from inputs made up of loading data and deterministic, stochastic, or even nonproportional material fatigue data.
COMSOL Multiphysics 3.4 Highlights
Parallelized meshing, assembly, and solving on multicore and multiprocessor computers
Memory-efficient fluid flow solvers for chemical engineering, heat transfer, and microfluidics
Segregated solver minimizes memory consumption for large multiphysics problems
Improved postprocessing including geometric properties such as center of gravity
Easy modeling of electronics cooling and free convection with interfaces for variable-density flow
Boundary layer meshing for representing boundary layers in fluid flow, heat transfer, and electromagnetics
Bubbly flow interfaces for modeling of scrubbers, aerators, bioreactors, food processing equipment, and boiling
Mixture-model two-phase flow interfaces for simulation of emulsification, sedimentation and separation processes as well as fluidized beds
Nonlinear parameter estimation
Piezoacoustic multiphysics modeling of microphones, ultrasonic transducers and MEMS devices
Full-wave 3D RF analysis of printed circuit boards and transmission lines with lumped port boundary conditions
Fatigue analysis
2007-11-14
Nupas 2007 v5.2(c)Cadmatic 3d hull

Nupas-Cadmatic ship design software was developed through a joint venture between Cadmatic Oy and the Dutch software design company, Numeriek Centrum Groningen B.V.
A Nupas-Cadmatic 3D-model of ship a ship engine room with machinery layout, piping and HVAC
By combining our resources we have created a design software package that provides better design solutions than traditional market offerings.Nupas-Cadmatic is a unique CAD/CAE/CAM design software package for shipyards and design offices interested in improving their efficiency, design and production. The open software lends itself to efficient hull-, machinery-, piping-, outfitting-, and interior design while efficiently creating the required production and maintenance information. The software supports concurrent and distributed design leading to more cost efficient and effective design.
3D Hull Engineering, the main hull modelling module, is the core of the Nupas-Cadmatic Hull system. It is used for modelling of the hull structure from the early design up to the detailed and production engineering of hull blocks, panels and parts.
The 3D Hull Engineering module distinguishes itself from other CAD/CAE/CAM systems in that it is extremely easy to use. The intuitive user interface guides the hull designer with maximum assistance while creating structural components like decks, bulkheads, stiffeners, shell frames, girders, flanges, brackets etc.
Hull structures are stored topologically, meaning that relations between structural components and relations with the hull shape allow fast and easy re-use of information without redoing work. The effects of modifications on a topological structure are automatically carried through to the related structural components.
The 3D Hull Engineering module includes powerful copy functions, parametric definition of yard standards and many automatic mechanisms like part and panel numbering, marking lines, standard bracket selection, part coding etc. taking away many of the hull designer's daily worries and routine tasks.
The project library used by the 3D Hull Engineering module consists of a collection of all necessary yard standards for cut outs, profile end shapes, stiffener types, brackets, holes and other structural entities. Besides the yard related standards, software settings and project specific parameters are also stored and maintained in the project library.
2007-11-13
Zuken.CR5000.Board.Designer.v10
Zuken's CR-5000 Board Designer provides an intuitive, integrated environment for designing PCBs, BGAs and MCMs. It serves to guide the user, via a common user interface, from schematic capture, floorplanning, placement and routing, analysis and into manufacturing. It operates seamlessly across Unix and Windows platforms combining the functionality of a high-end tool with ease of use. While rules are constant throughout the design process, they are dynamically linked to ensure flexibility and consistency.
Benefits
1. A single, intuitive environment with a coherent approach throughout the design process, easy links between tools, and a common database and libraries.
2. Rules-driven design for correct-by-construction outcomes.
3. An optimized combination of automatic, semi-automatic and interactive functionality to maximize design productivity.
4. Design partitioning that facilitates intelligent, concurrent engineering: especially useful for large or complex products and for the re-use of proven circuits.
5. Re-use of proven circuit blocks saves time.
The CR-5000 EDA design suite provides the most advanced PCB design functionality currently available. It is constraints driven, from schematic capture through board layout, to the output of manufacturing data. This means that the rules you apply early in the design process are maintained right through to manufacturing. So products are right first time, manufacturable first time, and get to market fast. A common component database is used throughout the process, so design, bill-of-materials (BOM) generation and manufacturing processes are based on a common data set. Efficiency is driven up, waste and re-work are eliminated. Amongst its other advanced features, CR-5000 supports advanced technologies such as build-up to facilitate miniaturization, automatic routing to speed up and optimize PCB layout, early design verification to eliminate design iterations (particularly in high-speed circuits), and RF design. It enables design re-use to prevent unnecessary duplication of effort, design partitioning to facilitate teams of individuals working on the various elements of a design simultaneously, and 3D viewing/editing for component placement and package optimization. CR-5000 is constantly developed and adjusted to new technologies in co-operation with our customers, to enable them to face to the challenges of the future.
Benefits
1. A single, intuitive environment with a coherent approach throughout the design process, easy links between tools, and a common database and libraries.
2. Rules-driven design for correct-by-construction outcomes.
3. An optimized combination of automatic, semi-automatic and interactive functionality to maximize design productivity.
4. Design partitioning that facilitates intelligent, concurrent engineering: especially useful for large or complex products and for the re-use of proven circuits.
5. Re-use of proven circuit blocks saves time.
The CR-5000 EDA design suite provides the most advanced PCB design functionality currently available. It is constraints driven, from schematic capture through board layout, to the output of manufacturing data. This means that the rules you apply early in the design process are maintained right through to manufacturing. So products are right first time, manufacturable first time, and get to market fast. A common component database is used throughout the process, so design, bill-of-materials (BOM) generation and manufacturing processes are based on a common data set. Efficiency is driven up, waste and re-work are eliminated. Amongst its other advanced features, CR-5000 supports advanced technologies such as build-up to facilitate miniaturization, automatic routing to speed up and optimize PCB layout, early design verification to eliminate design iterations (particularly in high-speed circuits), and RF design. It enables design re-use to prevent unnecessary duplication of effort, design partitioning to facilitate teams of individuals working on the various elements of a design simultaneously, and 3D viewing/editing for component placement and package optimization. CR-5000 is constantly developed and adjusted to new technologies in co-operation with our customers, to enable them to face to the challenges of the future.
2007-11-09
ASPEN-TECH (C)ASPENONE 2006
aspenONE® for Chemicals drives collaborative manufacturing by providing solutions for each phase of the business in an integrated environment, providing visibility, sharing and re-use of data and process models. By integrating the overall business processes, companies achieve significant improvements in performance with payback in months instead of years. aspenONE for Chemicals maximizes profitability by:
Optimizing feedstock selection and scheduling
Improving and accelerating process innovation
Optimizing plant performance
Standardize manufacturing workflow
Improving capital efficiency
Reducing environmental risk
Optimizing feedstock selection and scheduling
Improving and accelerating process innovation
Optimizing plant performance
Standardize manufacturing workflow
Improving capital efficiency
Reducing environmental risk
2007-11-05
RSoft-Photonics-CAD-Suite

RSoft Design Group produces photonic design and simulation software for both passive and active optical components for optical communications, optoelectronics and semiconductor manufacturing. The software is used by these organizations to reduce costs of creating a physical prototype, to assess design risks, and to assist in the discovery of new products from creating "what if" product scenarios. These key benefits enable a faster design process and shorter time to market.
RSoft currently addresses both passive and active devices through two design suites, a Passive Device Suite and an Active Device Suite. Each suite has a CAD environment, simulation engines and can utilize an optimization utility. Some of the key applications of our products include:
The RSoft CAD™ is the core program in the RSoft Photonic Suite, and allows researchers and engineers to create systems for the design of waveguide devices, optical circuits, and other photonic devices. It acts as a control program for RSoft's passive device simulation modules, including BeamPROP, FullWAVE, BandSOLVE, GratingMOD, and DiffractMOD, and defines the most important input required by these programs: the material properties and structural geometry of the photonic device to be studied.
Layout Capabilities The complete layout capabilities of the RSoft CAD have been designed from the ground up to accommodate the special needs of photonic devices and circuits. Fundamental objects such as straight, tapered, curved, y-branched waveguide segments and lenses can easily be selected from the toolbar, and graphically added to the circuit using the mouse. In addition to standard objects, the CAD also allows for the creation of customized components using mathematical equations or data files. Positioning coordinates may also be specified directly, either absolutely, or through relative offsets or angles with respect to any other waveguide component. At any time, one or several components may be selected and moved, scaled, deleted, or reinserted. Our unique design approach is an extremely flexible system in which the desired logical arrangement can be maintained as subsequent placement.
Object-Oriented Design
Each individual component has its own set of properties that can be accessed with a right click of the mouse. Parameters include shape information, such as taper or bend type and magnitude, and optical properties, such as refractive index profile type and value. This unique object-oriented input model is extremely natural and flexible. Each parameter of a component (e.g. position coordinates, width, index) can be specified by an arithmetic expression involving user-defined variables, rather than simply being a constant number. Thus, a waveguide circuit might have several angled waveguides, each with a different relative angular value. By using formulas to define each waveguide�s angle, the entire circuit can be modified by simply changing the value of a single variable, without having to redraw or otherwise edit
Component Design Products
include
BeamProp V8.0
FULLWAVE V6.0
BandSOLVE v4.0
GratingMOD v3.0
MOST v3.0
FemSIM v3.0
CimPACK v11.2.3
CimPACK Software
Each of these products is built around the same core software, a general purpose CAD engine called CimCAD, so they share the same user interface and file format. Our specialized licensing process allows you to pick the product or products that best fits your requirements.
CimPACK for Designers
Consists of a large library of Standard Designs, and Mix and Match so that you can create a one-up design and then lay it out to a printed sheet. This is the correct choice if you are doing folding carton or corrugated work but do not need to create any of the advanced pre-press tooling. Parametric design capability is also included.
CimPACK for Diemakers
We now offer two separate products for Diemakers. The standard Diemakers software includes tools for adding punches, hang holes, and die-edges. It also contains the tools for adding stripping/breaker knives, balancing rules, and chase registration holes. This is the correct choice for Gasket and Label companies as well as Diemakers that do not require pre-press tooling capabilities such as creation of Upper and Lower stripping boards, flat top blanking tools and phenolic counter plates.
The advanced Diemakers software includes the standard items plus all of the pre-press tooling. This includes the SF/SC Component Stripping System, the EASIBLANK(TM) blanking system, the SPEEDBAR(TM) presser bar system, the BSI Flush presser system, and the Bobst SPider presser system.. This software is ideal for the Diemaker who receives designs directly from the customer and does not require box design capabilities.
CimPACK Complete
This product includes all of the Designer, Diemaker, and Advanced Diemaker functions. If you require full design capabilities for producing flat dies and the associated tooling, then this is definitely the software you should be considering.
CimPACK for Rotary Diemakers
If you are a Rotary Diemaker, the Rotary functions can be added to CimPACK Complete and both of the CimPACK for Diemakers products.
Each of these products is built around the same core software, a general purpose CAD engine called CimCAD, so they share the same user interface and file format. Our specialized licensing process allows you to pick the product or products that best fits your requirements.
CimPACK for Designers
Consists of a large library of Standard Designs, and Mix and Match so that you can create a one-up design and then lay it out to a printed sheet. This is the correct choice if you are doing folding carton or corrugated work but do not need to create any of the advanced pre-press tooling. Parametric design capability is also included.
CimPACK for Diemakers
We now offer two separate products for Diemakers. The standard Diemakers software includes tools for adding punches, hang holes, and die-edges. It also contains the tools for adding stripping/breaker knives, balancing rules, and chase registration holes. This is the correct choice for Gasket and Label companies as well as Diemakers that do not require pre-press tooling capabilities such as creation of Upper and Lower stripping boards, flat top blanking tools and phenolic counter plates.
The advanced Diemakers software includes the standard items plus all of the pre-press tooling. This includes the SF/SC Component Stripping System, the EASIBLANK(TM) blanking system, the SPEEDBAR(TM) presser bar system, the BSI Flush presser system, and the Bobst SPider presser system.. This software is ideal for the Diemaker who receives designs directly from the customer and does not require box design capabilities.
CimPACK Complete
This product includes all of the Designer, Diemaker, and Advanced Diemaker functions. If you require full design capabilities for producing flat dies and the associated tooling, then this is definitely the software you should be considering.
CimPACK for Rotary Diemakers
If you are a Rotary Diemaker, the Rotary functions can be added to CimPACK Complete and both of the CimPACK for Diemakers products.
CoWare SPW 5-XP Version 5.03

CoWare SPW Advances Verification of 3G Wireless Modems
New HSDPA Models in 3GPP Library Reduce Design Risk for High-Speed Cellular Modems
SAN JOSE, Calif.--November 7, 2005--CoWare, Inc., the leading supplier of system-level electronic design automation (EDA) software and services announced the availability of the High Speed Downlink Packet Access (HSDPA) models in 3GPP Library for its SPW signal processing design solution. Wireless system designers are able to reduce their specification risk by up to 70%.
“Designing an HSDPA system requires a myriad of system performance simulations,” said Dr. Ahmad Vafaei, Senior Staff Engineer, InterDigital Communications Corporation. “We have been using CoWare’s HSPDA Library as a reference tool for the 3GPP Release 5 standard. Having an executable reference for 50% of the modem functionality lets us focus on the differentiating components of our HSDPA algorithms.”
“CoWare’s wireless design solution goes beyond the proof of concept demonstrations other ESL solution providers are offering,” said Johannes Stahl, Director Marketing, CoWare. “Our experienced team of wireless design experts continues to deliver detailed, high-quality libraries in lock step with the published standards. Whether you design a particular modem or you are working on software-defined radio, CoWare has the wireless models you need.”
HSDPA – Complex, Adaptive Modulation and Coding, Hybrid ARQ
HSDPA delivers high data rates according to the transmission conditions by using adaptive modulation and coding (AMC) schemes. These cover a wide dynamic range in order to cope with the varying downlink radio and channel quality conditions at the handset. HSDPA adapts to these conditions by modifying the effective code rate, the modulation scheme, the number of codes used and power per code. The Hybrid ARQ (H-ARQ) mechanism is used in HSDPA to reduce the delay and increase the efficiency of the retransmitting data. Developing HSDPA receivers, which exhibit the desired performance using AMC and H-ARQ under varying channel conditions, is a design problem with an order of magnitude more scenarios to consider than the static modulation schemes used in previous 3GPP standards.
SPW Libraries Speed HSDPA Design
CoWare SPW is a complete platform for design and verification of DSP algorithms. Its up-to-date communications and multimedia source code libraries are transparently accessible, providing unmatched value for standards explanation and design. The 3GPP library is Release 5 compliant with the newly-added executable end-to-end system models of the HSDPA standard. Using the library, system engineers can rapidly create an accurate model of the system, incorporate their differentiating components, and then simulate the system under different scenarios to optimize the system performance. Leveraging SPW’s high simulation speed, users can now explore many system options. And, with source code delivery and powerful PolyModel, designers can use the library as a starting point for detailed fixed-point design. Because the SPW HSDPA library was developed from active participation in the standardization process and with many years of experience developing 3G UMTS/WCDMA models, second-guessing of written standards proposals is eliminated.
Availability & Pricing
CoWare SPW with the 3GPP HSDPA Library and Communication Library is available today.
October 0day software
2007-10-31 AUTODESK_MUDBOX_PRO_V1.0.7
2007-10-30 PTC.Mathcad.v14.0.GERMAE
2007-10-30 ANSYS.PRODUCTS.V11.SP1.WIN32
2007-10-30 INNEO.Startup.TOOLS.v2008.WiNNT2K
2007-10-28 Telelogic.Rhapsody.v7.1.For WiNNT2K&Linux
2007-10-28 PATHTRACE.EDGECAM.V12
2007-10-28 PTC.Arbortext.Editor.and.Architect.v5.3.WiNNT2K
2007-10-27 Simatic.Step7.Professional.Edition.2006.SR3.MULTiLANGUAGE
2007-10-27 AUTODESK_LUSTRE_V2008
2007-10-25 Schrodinger.Suite.2007
2007-10-25 Intel.VTune.Performance.Analyzer.v9.0.030
2007-10-22 Bentley.Microstation.GEOPAK.Survey.XM.Edition.v08.09.04.37
2007-10-22 Delcam.Powermill.Pro.8009.CB1098013.SP1.Multilanguage
2007-10-22 Bentley.Map.XM.v08.09.04.45
2007-10-22 Bentley.Microstation.GEOPAK.Site.XM.v08.09.04.37
2007-10-16 UGS.NX5.V5.0.2.UPDATE for X86 &X64
2007-10-16 MSC.PATRAN.V2007.FOR R1B.LINUX.IRIX ,Win
2007-10-16 MSC.FEA.AFEA.V2006.R1
2007-10-15 GEOMAGIC_STUDIO_V9_SR3
2007-10-15 GEOMAGIC_QUALIFY_V9_SR2
2007-10-15 GEOMAGIC_ESHELL_V8
2007-10-14 CAD_TRANSLATORS_FOR_CRANES_NISA_V15.1
2007-10-14 SmartCode.VNC.Manager.Enterprise.v3.6.24.0
2007-10-14 Siemens.SIMATIC.S7.SCL.v5.3.SP2.Multilanguage
2007-10-14 Bentley.Civil.Extension.for.GEOPAK.v08.08.02.81
2007-10-14 Bentley.Microstation.GEOPAK.Civil.Engineering.Suite.XM.v08.09.04.37
2007-10-14 Bentley.Microstation.GEOPAK.Suite.v8.08.02.81
2007-10-14 Bentley.PowerCivil.v08.09.04.37.for.Powerdraft.XM
2007-10-14 Bentley.PowerSurvey.v08.09.04.37.for.Powerdraft.XM
2007-10-11 PTC.PRO.ENGINEER.WILDFIRE.v3.0.M100.WIN32&WIN64$Linux DVD
2007-10-11 ADAPT_BUILDER_ABI_V5.0
2007-10-10 UGS.SOLID.EDGE.V20 DVD
2007-10-10 DIMSOLN_COMBINED_3D_V4.0.0
2007-10-10 DIMSOLN_FOUNDATION_3D_V4.0.0
2007-10-10 DIMSOLN_MAT_3D_V4.0.0
2007-10-10 DIMSOLN_SHAFT_3D_V3.0.0
2007-10-10 LEAPSOFT_CONBOX_V7.0.1
2007-10-10 LEAPSOFT_CONSPAN_RATING_V7.0.1
2007-10-10 LEAPSOFT_CONSYS_V1.3.0
2007-10-10 LEAPSOFT_GEOMATH_V7.0.0
2007-10-10 LEAPSOFT_RC-PIER_V7.0.0
2007-10-09 Reation.Design.Chemkin.v4.11.WiNNT2K
2007-10-08 CADRASTER.PRO.V8.0.FOR.AUTOCAD
2007-10-08 TESSEL.HYPERDOC.V4.51-
2007-10-06 Pointwise.Gridgen.v16.0.WiNNT2 For Linux
2007-10-06 ANSYS.PRODUCTS.V11.SP1 for Win32&win64 2DVD
2007-10-05 Mastcam X2_MR2 V11.2.35 1CD
2007-10-03 BMW.ETK.v8.0.2007.MULTiLANGUAGE
2007-10-03 OpenMind.HyperMILL.V9.5.incl.SP4.HF.33658.Multilanguage.DVD.
2007-10-03 Siemens.Simatic.WinCC.Connectivity.Pack.v6.2.MULTiLANGUAGE.
2007-10-03 Mathworks.Matlab.R2007b DVD
2007-10-03 GibbsCAM.2007.v8.5.30
form caxsoft
2007-10-30 PTC.Mathcad.v14.0.GERMAE
2007-10-30 ANSYS.PRODUCTS.V11.SP1.WIN32
2007-10-30 INNEO.Startup.TOOLS.v2008.WiNNT2K
2007-10-28 Telelogic.Rhapsody.v7.1.For WiNNT2K&Linux
2007-10-28 PATHTRACE.EDGECAM.V12
2007-10-28 PTC.Arbortext.Editor.and.Architect.v5.3.WiNNT2K
2007-10-27 Simatic.Step7.Professional.Edition.2006.SR3.MULTiLANGUAGE
2007-10-27 AUTODESK_LUSTRE_V2008
2007-10-25 Schrodinger.Suite.2007
2007-10-25 Intel.VTune.Performance.Analyzer.v9.0.030
2007-10-22 Bentley.Microstation.GEOPAK.Survey.XM.Edition.v08.09.04.37
2007-10-22 Delcam.Powermill.Pro.8009.CB1098013.SP1.Multilanguage
2007-10-22 Bentley.Map.XM.v08.09.04.45
2007-10-22 Bentley.Microstation.GEOPAK.Site.XM.v08.09.04.37
2007-10-16 UGS.NX5.V5.0.2.UPDATE for X86 &X64
2007-10-16 MSC.PATRAN.V2007.FOR R1B.LINUX.IRIX ,Win
2007-10-16 MSC.FEA.AFEA.V2006.R1
2007-10-15 GEOMAGIC_STUDIO_V9_SR3
2007-10-15 GEOMAGIC_QUALIFY_V9_SR2
2007-10-15 GEOMAGIC_ESHELL_V8
2007-10-14 CAD_TRANSLATORS_FOR_CRANES_NISA_V15.1
2007-10-14 SmartCode.VNC.Manager.Enterprise.v3.6.24.0
2007-10-14 Siemens.SIMATIC.S7.SCL.v5.3.SP2.Multilanguage
2007-10-14 Bentley.Civil.Extension.for.GEOPAK.v08.08.02.81
2007-10-14 Bentley.Microstation.GEOPAK.Civil.Engineering.Suite.XM.v08.09.04.37
2007-10-14 Bentley.Microstation.GEOPAK.Suite.v8.08.02.81
2007-10-14 Bentley.PowerCivil.v08.09.04.37.for.Powerdraft.XM
2007-10-14 Bentley.PowerSurvey.v08.09.04.37.for.Powerdraft.XM
2007-10-11 PTC.PRO.ENGINEER.WILDFIRE.v3.0.M100.WIN32&WIN64$Linux DVD
2007-10-11 ADAPT_BUILDER_ABI_V5.0
2007-10-10 UGS.SOLID.EDGE.V20 DVD
2007-10-10 DIMSOLN_COMBINED_3D_V4.0.0
2007-10-10 DIMSOLN_FOUNDATION_3D_V4.0.0
2007-10-10 DIMSOLN_MAT_3D_V4.0.0
2007-10-10 DIMSOLN_SHAFT_3D_V3.0.0
2007-10-10 LEAPSOFT_CONBOX_V7.0.1
2007-10-10 LEAPSOFT_CONSPAN_RATING_V7.0.1
2007-10-10 LEAPSOFT_CONSYS_V1.3.0
2007-10-10 LEAPSOFT_GEOMATH_V7.0.0
2007-10-10 LEAPSOFT_RC-PIER_V7.0.0
2007-10-09 Reation.Design.Chemkin.v4.11.WiNNT2K
2007-10-08 CADRASTER.PRO.V8.0.FOR.AUTOCAD
2007-10-08 TESSEL.HYPERDOC.V4.51-
2007-10-06 Pointwise.Gridgen.v16.0.WiNNT2 For Linux
2007-10-06 ANSYS.PRODUCTS.V11.SP1 for Win32&win64 2DVD
2007-10-05 Mastcam X2_MR2 V11.2.35 1CD
2007-10-03 BMW.ETK.v8.0.2007.MULTiLANGUAGE
2007-10-03 OpenMind.HyperMILL.V9.5.incl.SP4.HF.33658.Multilanguage.DVD.
2007-10-03 Siemens.Simatic.WinCC.Connectivity.Pack.v6.2.MULTiLANGUAGE.
2007-10-03 Mathworks.Matlab.R2007b DVD
2007-10-03 GibbsCAM.2007.v8.5.30
form caxsoft
2007-11-03
DASSAULT.SYSTEMES.CATIA.P3.V5R18.SP1

CATIA V5.18 improves quality of the final composite part through post-processing analysis
CATIA V5.18 extends the end-to-end composites process from design to simulation to manufacturing for automotive and aerospace industries. CATIA V5.18 delivers post-processing analysis on composite parts for an accurate product behavior evaluation. It embeds failure criteria specification to composites structure (Tsai-Hill and Tsai Wu criteria) to give a better assessment of composites parts. In addition, the composites analysis environment can receive all producibility information needed to ensure accurate manufacturing results.
Enables effective Electronics CAD and Mechanical CAD design collaboration by strengthening the Printed Circuit Board (PCB) design process
A library of 3D components, defined in neutral data exchange format, from several construction methods, either designed in CATIA or imported through data exchange formats, makes it easy to map with several ECAD tool import/export references to the position of electrical components without the need to redesign in CATIA.
Integrates knowledge early in the design process for significant quality improvements
V5.18 enables Generative electrical design based on company rules captured in V5 knowledge - Generative Harness covering placement (Tube, Tape), Generative electrical parts connections (auto create electrical assemblies from catalog), and delivers more electrical design checks (part connection compatibility, wire route and manufacturability, splice location in harness, completion of V5 electrical model).
Reinforces end-to-end electrical process by integrating manufacturing constraints directly in the design
CATIA V5.18 enhances CATIA Electrical Harness Flattening for harness drawing production by delivering more accurate harness manufacturing documentation (Backshell representation), smoothing harness flattening process for device orientation and improving the harness drafting quality. The CATIA Electrical Harness offer reduces the design to manufacturing cycle time especially for Automotive and Aerospace CATIA V5 Electrical design customers. The flattening process becomes more robust and completes the layout process more efficiently.
Subscribe to:
Posts (Atom)