Mentor Graphics Corporation (Nasdaq: MENT) today announced the Questa™ Vanguard Program (QVP), a partnership with industry-leading companies to enhance the verification options for Questa users and build a strong and comprehensive SystemVerilog ecosystem.
The Questa Vanguard Program extends Mentor Graphics breadth of verification technologies through partnerships with other industry-leading companies that provide verification related tools and methods, verification IP, conversion services, training and consulting. Through these technology alliances and strategic partnerships, Mentor Graphics leverages resources and technical expertise to deliver even greater value to Questa users, including strong product integration with other Mentor Graphics technologies (see news release "Mentor Graphics Delivers the Next Generation of Functional Verification," May 8, 2006).
"Without adequate industry infrastructure, no new technologies or methodologies can be successful," said Dennis Brophy, director of strategic business development at Mentor Graphics. "Mentor Graphics is committed to work closely with partners to ensure full support of the Questa platform."
With the Questa Vanguard Program, Mentor has joined forces with leaders (see list of vendors enclosed) in training, consulting, conversion services and verification intellectual property (IP) to simplify and accelerate the adoption of new verification languages and techniques. Each partner works closely with Mentor to ensure that their products support the Questa platform and the Advanced Verification Methodology (AVM). In particular, Mentor has worked with select partners to facilitate the availability of their conversion products and services to help users rapidly migrate from proprietary single-vendor languages to SystemVerilog and the AVM.
QVP enables design and verification engineers to meet today's verification challenges by extending and augmenting the Questa solution via Mentor's partnerships, thus allowing customers to identify the right partner for their verification needs. With a strong balance of QVP partners that support a broad set of verification IP, Mentor Graphics leverages the verification IP qualified for use with the Questa platform to deliver greater value to Mentor customers. QVP partners support more than 30 protocols with over 50 verification IP elements.
2010-12-22
Lighttools-v7.1
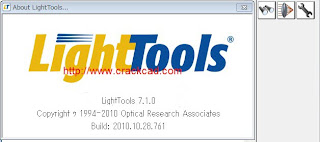
LightTools delivers true design capabilities, accurate analyses, and high-powered product visualization features that will help you get illumination systems to market faster. Explore LightTools’ key features in more detail to find out how it can meet your specific illumination design needs
LightTools’ robust design features help you quickly and efficiently create and modify your illumination system design, from initial concept phases to subsequent engineering iterations and refinements.
Key design features ▼
* Sophisticated solid modeling with full optical accuracy
* State-of-the-art ray tracing speed, with full user control of accuracy and resolution requirements
* Create a light source from any geometric model, for unlimited flexibility to create custom sources
* Application-specific utilities to help you quickly build a complete model
* Extensive source and materials libraries, including LEDs and BSDF measurements
* Robust data exchange support for mechanical CAD data
* Interactive, dynamic link with SolidWorks®.
* Multiple immersion for modeling the embedded phosphor in an encapsulated LED
* Fully optimizable skinned solids for creating efficient LED couplers, solar concentrators, and other complex optical surfaces
* User-defined materials to model phosphor-based white LEDs
* Textures – 2D, 3D, and user defined – with flexibility to vary the shape, size, and spacing of texture elements
* Calculate the color rendering index (CRI) on any receiver – ideal for LED and luminaire design
* Intensity data collection that enables data exchange with other lighting design software through the IES and LDT data formats
* Point-and-shoot ray tracing for real-time, immediate feedback on your system’s light behavior during design iterations
2010-12-20
2010 0day software download
2010-11-30 HyperMILL9.7 SP3 for SolidWorks 2008 SP1
2010-11-29 Tekla Structures v16.1
2010-11-29 CSC Orion v16.0
2010-11-28 IVS.3D.Fledermaus.Professional.v7.2.1a.437
2010-11-26 CIMCO.Software.Suite v6.01.07
2010-11-26 SPI SheetmetalWorks 2011
2010-11-25 3DQuickPress v5.1.0 for SolidWorks 2009-2011
2010-11-24 CAMWorks 2010 SP2.2 for SolidWorks 2010-2011
2010-11-23 HyperMILL v9.7 SP3 for Pro E Wildfire 4.0
2010-11-22 Portable RISA 3D 8.1
2010-11-21 SolidCAM 2010 SP3 HF1
2010-11-19 PowerShape 2011 R1 SP2 Update Only Win32
2010-11-19 Tripos.SYBYL-X.ORCHESTRAR.Databases.v0808.231-IS
2010-11-18 ElectrodeWorks v2011 SP0 Win32&WIN64
2010-11-17 MoldWorks v2011 SP0 Win32&WIN64
2010-11-16 iMold v10 SP2 R3 for SolidWorks 2007-2010
2010-11-15 COMSOL.Multiphysics.v4.0a.Multiplatform
2010-11-12 Autodesk.Quantity.Takeoff.v2011
2010-11-11 Siemens.Digsi.v4.83
2010-11-10 HSM v5.0.5.22708 for Mastercam X5
2010-11-09 MSC MD Nastran v2010.1
2010-11-08 Mastercam X5 V14
2010-11-06 PTC Pro E RSD 9.0 M010
2010-11-04 Tebis v3.4 R4
2011-11-03 Golden Software Voxler v2.2.1057
2010-10-31 Nemetschek Allplan 2011
2010-10-30 CSI Perform-3D v4.04
2010-10-28 Vamos v5.8.2 for Catia v5R19
2010-10-26 CEI.Ensight.Gold.v9.1.2e
2010-10-25 IVS.3D.Fledermaus.Professional.v7.2.1.429
2010-10-24 Autodesk Robot Structural Analysis Pro 2011
2010-10-22 Delcam Exchange 2011 v6.3.10.06 Win32&64
2010-10-20 SolidWorks 2011 SP0.0 Full Multilanguage
2010-10-19 AUTODESK.INVENTOR.PUBLISHER.V2011.R1
2010-10-18 Solid Edge ST3 Win32&Win64
2010-10-17 LMS.TEST.LAB.Rev10B
2010-10-16 MSC.MD.Nastran.v2010
2010-10-15 SolidCAM v2010 SP2 HF1
2010-10-14 PTV VISSIM v5.03
2010-10-12 Camnetics.GearTeq.v2010.18.32.324
2010-10-11 MVTec HALCON 10
2010-10-10 GeometryWorks3D Features v9.0 Build 0007
2010-10-08 CADKON-2D.2011
2010-10-07 CIMCO.Software.Suite.v5.60.73
2010-10-06 Optiwave OptiFDTD 10.0
2010-10-06 Optiwave OptiBPM 10.0.1
2010-10-05 Optiwave OptiGrating 4.2.2
2010-10-04 Optiwave OptiSystem 9.0.1
2010-10-05 Autodesk.Factory.Design.Suite.Premium.2011
2010-10-03 CSI SAP2000 v14.2.2
2010-10-02 PTC Pro ToolMakep v9.0 M060
2010-10-01 Safe.Software.FME.Desktop.v2010.SP3.build.6231
2010-09-30 Maplesoft.Maple.v14.0
2010-08-29 Beta-CAE Ansa v13.0.5
2010-09-27 Encom Engage3D v6.004
from:caxcrack
2010-09-25 EPLAN.Electric.P8.v2.0.4602
2010-09-24 NovaFlow & Solid CV v4.3r6
2010-09-22 Golden.Software.Grapher.v8.4.696
2010-09-21 Crystal.Impact.Endeavour.v1.7e
2010-09-20 ESI.CFD.V2010
2010-09-19 Pointwise.v16.03R4
2010-09-18 PTC.PRO.ENGINEER.WILDFIRE.V5.M060
2010-09-17 Rocscience.Slide.V6.005
2010-09-17 Rocscience.Rocfall.v4.054
2010-09-16 GeoTools.for.autocad.v11
2010-09-15 Imbsen.WinFAD.V5
2010-09-14 ITTVIS.IDL.v7.1.1
2010-09-13 PC-Progress HYDRUS v1.11
2010-09-10 CAMTOOLS V6.1
2010-09-12 SHARC HARPOON 4.2a X64
2010-09-06 Mathworks.Matlab.R2010b for Win&Unix
2010-09-04 TNO DIANA v9.4
2010-09-03 Deform 2D/3D v10.0
2010-09-02 CEI.ENSIGHT.GOLD.v9.1.2c
2010-09-01 Sharc.Harpoon.v4.2a for Win,Linux
2010-11-29 Tekla Structures v16.1
2010-11-29 CSC Orion v16.0
2010-11-28 IVS.3D.Fledermaus.Professional.v7.2.1a.437
2010-11-26 CIMCO.Software.Suite v6.01.07
2010-11-26 SPI SheetmetalWorks 2011
2010-11-25 3DQuickPress v5.1.0 for SolidWorks 2009-2011
2010-11-24 CAMWorks 2010 SP2.2 for SolidWorks 2010-2011
2010-11-23 HyperMILL v9.7 SP3 for Pro E Wildfire 4.0
2010-11-22 Portable RISA 3D 8.1
2010-11-21 SolidCAM 2010 SP3 HF1
2010-11-19 PowerShape 2011 R1 SP2 Update Only Win32
2010-11-19 Tripos.SYBYL-X.ORCHESTRAR.Databases.v0808.231-IS
2010-11-18 ElectrodeWorks v2011 SP0 Win32&WIN64
2010-11-17 MoldWorks v2011 SP0 Win32&WIN64
2010-11-16 iMold v10 SP2 R3 for SolidWorks 2007-2010
2010-11-15 COMSOL.Multiphysics.v4.0a.Multiplatform
2010-11-12 Autodesk.Quantity.Takeoff.v2011
2010-11-11 Siemens.Digsi.v4.83
2010-11-10 HSM v5.0.5.22708 for Mastercam X5
2010-11-09 MSC MD Nastran v2010.1
2010-11-08 Mastercam X5 V14
2010-11-06 PTC Pro E RSD 9.0 M010
2010-11-04 Tebis v3.4 R4
2011-11-03 Golden Software Voxler v2.2.1057
2010-10-31 Nemetschek Allplan 2011
2010-10-30 CSI Perform-3D v4.04
2010-10-28 Vamos v5.8.2 for Catia v5R19
2010-10-26 CEI.Ensight.Gold.v9.1.2e
2010-10-25 IVS.3D.Fledermaus.Professional.v7.2.1.429
2010-10-24 Autodesk Robot Structural Analysis Pro 2011
2010-10-22 Delcam Exchange 2011 v6.3.10.06 Win32&64
2010-10-20 SolidWorks 2011 SP0.0 Full Multilanguage
2010-10-19 AUTODESK.INVENTOR.PUBLISHER.V2011.R1
2010-10-18 Solid Edge ST3 Win32&Win64
2010-10-17 LMS.TEST.LAB.Rev10B
2010-10-16 MSC.MD.Nastran.v2010
2010-10-15 SolidCAM v2010 SP2 HF1
2010-10-14 PTV VISSIM v5.03
2010-10-12 Camnetics.GearTeq.v2010.18.32.324
2010-10-11 MVTec HALCON 10
2010-10-10 GeometryWorks3D Features v9.0 Build 0007
2010-10-08 CADKON-2D.2011
2010-10-07 CIMCO.Software.Suite.v5.60.73
2010-10-06 Optiwave OptiFDTD 10.0
2010-10-06 Optiwave OptiBPM 10.0.1
2010-10-05 Optiwave OptiGrating 4.2.2
2010-10-04 Optiwave OptiSystem 9.0.1
2010-10-05 Autodesk.Factory.Design.Suite.Premium.2011
2010-10-03 CSI SAP2000 v14.2.2
2010-10-02 PTC Pro ToolMakep v9.0 M060
2010-10-01 Safe.Software.FME.Desktop.v2010.SP3.build.6231
2010-09-30 Maplesoft.Maple.v14.0
2010-08-29 Beta-CAE Ansa v13.0.5
2010-09-27 Encom Engage3D v6.004
from:caxcrack
2010-09-25 EPLAN.Electric.P8.v2.0.4602
2010-09-24 NovaFlow & Solid CV v4.3r6
2010-09-22 Golden.Software.Grapher.v8.4.696
2010-09-21 Crystal.Impact.Endeavour.v1.7e
2010-09-20 ESI.CFD.V2010
2010-09-19 Pointwise.v16.03R4
2010-09-18 PTC.PRO.ENGINEER.WILDFIRE.V5.M060
2010-09-17 Rocscience.Slide.V6.005
2010-09-17 Rocscience.Rocfall.v4.054
2010-09-16 GeoTools.for.autocad.v11
2010-09-15 Imbsen.WinFAD.V5
2010-09-14 ITTVIS.IDL.v7.1.1
2010-09-13 PC-Progress HYDRUS v1.11
2010-09-10 CAMTOOLS V6.1
2010-09-12 SHARC HARPOON 4.2a X64
2010-09-06 Mathworks.Matlab.R2010b for Win&Unix
2010-09-04 TNO DIANA v9.4
2010-09-03 Deform 2D/3D v10.0
2010-09-02 CEI.ENSIGHT.GOLD.v9.1.2c
2010-09-01 Sharc.Harpoon.v4.2a for Win,Linux
2010-10-10
CAM-TOOL-V6.1
CAM-TOOL, the "Elite CAD/CAM" system, addresses the needs of the Manufacturing Tooling Industry. CAM-TOOL addresses the sophisticated requirements of Mold & Die builders by offering unparalleled functionality using our powerful NC programming strategies that simply do not exist in other systems.
Whether you're doing High Speed Machining or Hard Milling, CAM-TOOL's integrated surfacing modeling and NC programming techniques allow the user to generate toolpath to run your NC machine "Safely & Unattended" while providing unparalleled finish quality.
Sophisticated NC programmers appreciate the importance of a complete, integrated CAD/CAM environment to handle the toughest manufacturing jobs. Regardless of the application, these ELITE users often find the need to modify, edit & create additional geometry to support the creation of toolpath.
Compatible with Windows XP (32 and 64-bit) Windows Vista (Coming Soon), CAM-TOOL provides Mold & Die manufactures a wide range of modeling capabilities not found in "high end" programming systems. Once your data's prepared, the calculation of NC toolpath is completed by simply defining your machining strategy & cutting tools. CAM-TOOL does the rest by always making sure the tool only goes where necessary to remove material using our powerful optimization capabilities.
CAM-TOOL's ability to create toolpath based on surfaces, not a mesh provides unbelievable finish quality. In addition, our unique Z-Level-Offset cutting and Re-Machining strategies allow programmers of "Hard Tools" and "High Speed Machines" to control the amount of material to be removed with each pass. Providing programmers with:
* Improved Finish Quality
* Safe Unattended Machining
* Increased Tool Life
* Reduction of benching & hand work
* Spot Free/Polish Free Toolpath
* Operation & Tool reduction
Whether you're doing High Speed Machining or Hard Milling, CAM-TOOL's integrated surfacing modeling and NC programming techniques allow the user to generate toolpath to run your NC machine "Safely & Unattended" while providing unparalleled finish quality.
Sophisticated NC programmers appreciate the importance of a complete, integrated CAD/CAM environment to handle the toughest manufacturing jobs. Regardless of the application, these ELITE users often find the need to modify, edit & create additional geometry to support the creation of toolpath.
Compatible with Windows XP (32 and 64-bit) Windows Vista (Coming Soon), CAM-TOOL provides Mold & Die manufactures a wide range of modeling capabilities not found in "high end" programming systems. Once your data's prepared, the calculation of NC toolpath is completed by simply defining your machining strategy & cutting tools. CAM-TOOL does the rest by always making sure the tool only goes where necessary to remove material using our powerful optimization capabilities.
CAM-TOOL's ability to create toolpath based on surfaces, not a mesh provides unbelievable finish quality. In addition, our unique Z-Level-Offset cutting and Re-Machining strategies allow programmers of "Hard Tools" and "High Speed Machines" to control the amount of material to be removed with each pass. Providing programmers with:
* Improved Finish Quality
* Safe Unattended Machining
* Increased Tool Life
* Reduction of benching & hand work
* Spot Free/Polish Free Toolpath
* Operation & Tool reduction
TNO-DIANA-v9.4
DIANA is a well proven and tested software package with a reputation for handling difficult technical problems relating to design and assessment activities in concrete, steel, soil, rock and soil-structure interaction. The program’s robust functionality includes extensive material, element and procedure libraries based on advanced database techniques, linear and non-linear capabilities, full 2D and 3D modelling features and tools for CAD interoperability. With the continuous demand for more efficient utilization of resources and materials, together with the increasingly complex nature of engineering structures, DIANA is becoming the software of choice for gaining a competitive advantage when tackling design and assessment work. Shouldn’t you be using DIANA
2010/08 0day software ftp download
2010-08-30 IntelliCAD.Fine.ELEC.10.NG.v6.6.59.3
2010-08-27 RockWare.RockWorks.15.v2010.7.2
2010-08-26 AutoCAD Architecture.2011
2010-08-25 MapleSoft.Maple.v14.0.Mac OSX
2010-08-23 SpaceClaim.v2010
2010-08-21 ShipConstructor 2011
2010-08-20 Alibre.Design.Expert.v12.1.0.12047
2010-08-20 sp3 for Dassault Systemes CATIA Pi V5R20 x86+x64
2010-08-19 PTC Protoolmaker v9.0 M06
2010-08-17 Geomagic Qualify v12
2010-08-17 Geomagic Studio v12
2010-08-15 PTC Cocreate.2010.v17
2010-08-15 Eagle Point 2010 Q1 10.1.0
2010-08-14 Rocscience.Phase2 v7.015
2010-08-14 EDS Factory v8.0 For AutoCAD
2010-08-13 Shoemaster QS v9.03
2010-08-12 Tower v6.0 Build 1410
2010-08-09 Bitplane.Imaris.v7.1.1
2010-08-08 CSI.ETABS.V9.71
2010-08-07 Pointwise.Gridgen.v15.15
2010-08-06 CAMWorks 2010 SP1.2 Win32&win64
2010-08-05 CSI Safe v12.30
2010-08-03 DriveWorks.Solo.v7.4.0.346
2010-08-01 EdgeCAM 2010 R2
from caxcrack
2010-08-26 Silvaco AMS v2010
2010-08-25 Cadence SPB v16.30.014 Update
2010-08-23 Mentor.Graphics.ModelSIM.SE.v6.6b
2010-08-20 CST Studio Suite 2010 SP5
2010-08-19 NI LabVIEW 2010 Database Connectivity Toolkit
2010-08-19 NI LabVIEW 2010 PID and Fuzzy Logic Toolkit
2010-08-18 NI LabVIEW 2010 Run-Time Engine
2010-08-17 NI LabVIEW C Generator 2010
2010-08-16 NI LabVIEW 2010
2010-08-16 Mentor.Graphics.Calibre.v2010.2.38.23.Linux
2010-08-15 Cadence Low Power Methodology Kit v08.02.001
2010-08-14 Agilent Genesys 2010.05
2010-08-13 SynaptiCAD.Product.Suite.v15.04a
2010-08-12 Keil MDK v4.12
2010-08-09 Altera.Quartus.II.v10 win&Linux
2010-08-08 Mentor.Graphics.Catapult.V2010a.104
2010-08-07 IAR.visualSTATE.v6.3.1
2010-08-06 Zuken.CADSTAR.v12.1
2010-08-04 Cadence EDI v9.1
2010-08-03 SynaptiCAD.Product.Suite.v15.04a
2010-08-01 AWR Design Environment 2010
2010-08-27 RockWare.RockWorks.15.v2010.7.2
2010-08-26 AutoCAD Architecture.2011
2010-08-25 MapleSoft.Maple.v14.0.Mac OSX
2010-08-23 SpaceClaim.v2010
2010-08-21 ShipConstructor 2011
2010-08-20 Alibre.Design.Expert.v12.1.0.12047
2010-08-20 sp3 for Dassault Systemes CATIA Pi V5R20 x86+x64
2010-08-19 PTC Protoolmaker v9.0 M06
2010-08-17 Geomagic Qualify v12
2010-08-17 Geomagic Studio v12
2010-08-15 PTC Cocreate.2010.v17
2010-08-15 Eagle Point 2010 Q1 10.1.0
2010-08-14 Rocscience.Phase2 v7.015
2010-08-14 EDS Factory v8.0 For AutoCAD
2010-08-13 Shoemaster QS v9.03
2010-08-12 Tower v6.0 Build 1410
2010-08-09 Bitplane.Imaris.v7.1.1
2010-08-08 CSI.ETABS.V9.71
2010-08-07 Pointwise.Gridgen.v15.15
2010-08-06 CAMWorks 2010 SP1.2 Win32&win64
2010-08-05 CSI Safe v12.30
2010-08-03 DriveWorks.Solo.v7.4.0.346
2010-08-01 EdgeCAM 2010 R2
from caxcrack
2010-08-26 Silvaco AMS v2010
2010-08-25 Cadence SPB v16.30.014 Update
2010-08-23 Mentor.Graphics.ModelSIM.SE.v6.6b
2010-08-20 CST Studio Suite 2010 SP5
2010-08-19 NI LabVIEW 2010 Database Connectivity Toolkit
2010-08-19 NI LabVIEW 2010 PID and Fuzzy Logic Toolkit
2010-08-18 NI LabVIEW 2010 Run-Time Engine
2010-08-17 NI LabVIEW C Generator 2010
2010-08-16 NI LabVIEW 2010
2010-08-16 Mentor.Graphics.Calibre.v2010.2.38.23.Linux
2010-08-15 Cadence Low Power Methodology Kit v08.02.001
2010-08-14 Agilent Genesys 2010.05
2010-08-13 SynaptiCAD.Product.Suite.v15.04a
2010-08-12 Keil MDK v4.12
2010-08-09 Altera.Quartus.II.v10 win&Linux
2010-08-08 Mentor.Graphics.Catapult.V2010a.104
2010-08-07 IAR.visualSTATE.v6.3.1
2010-08-06 Zuken.CADSTAR.v12.1
2010-08-04 Cadence EDI v9.1
2010-08-03 SynaptiCAD.Product.Suite.v15.04a
2010-08-01 AWR Design Environment 2010
2010-08-24
Radimpex-Tower-6-download-crack
Tower 6, application for static and dynamic structural analysis, concrete, steel and timber design.
Tower 6 is a graphical program for universal analysis of influences in planar and space structures. By providing strong tools that are automated, integrated, all-inclusive and intuitive, this program enables the engineers to increase the speed and quality of designing. Version 6 is a high performance professional tool, based on experience lasting many years and on the latest knowledge and realization of the expert team, engineers and first-class programmers.
Graphical Interface
• Defining the arbitrary planes for drawing
• Simultaneous use of planar and space drawing
• Selecting precisely the points in the drawing (dynamic osnap with combined criteria)
• Dynamic zoom and pan. Dynamic rotation of isometric presentation of the model (orbit)
• Manipulating the elements in the drawing (copying, mirror copying, deleting, rotating, complete undo/redo system of restoring the drawings, etc.)
• Generating automatically the vertical elements of the structure
• Generating automatically the rotationally symmetric bodies (sphere, cone, vault, helix)
• Operating with blocks of drawings (saving and entering the arbitrarily selected parts of the model)
• Grouping the arbitrarily selected parts of the model into wholes and deleting the visibility to other parts of the model (only columns, walls, typical floor structures, web members, main girders, etc. visible)
• Visualization of the model (DirectX render, walking through building with camera)
Processing the Calculation Results
• Finding quickly the extreme values of influences in the whole model or only in a certain group of elements (extreme values of axial forces in columns only, etc.) maximal bending moments in plates in typical floor, maximal displacements of walls only, etc.)
• Presentation of results, both in the entire space model and in its certain parts (in selected frame, wall, floor structure, foundations, arbitrarily selected view, etc.)
• Presentation of results in surface elements by isolines and diagrams along an arbitrarily assigned intersection line
• Presentation of influences in linear elements by diagrams and color gradientsPresentation of support reactions with direction and intensity
• Diagrams of stress distribution in composite cross-sections through defined stages of constructing
• Influences in individual parts of composite cross section
• Simultaneous presentation of influences in all columns and walls in one level (insight into distribution of influences due to seismic action on all columns and walls in one floor, redistribution of axial forces due to vertical load onto columns and walls of a given level, etc.)
• Presentation and animation of oscillating forms and deformed model
• Completely automatized dimensioning of reinforced concrete, steel and wood structures (JUS, EUROCOD, SNIP, DIN, etc.)
• Adopting reinforcement in reinforced concrete structures with automatic creating of reinforcement details and export to our program "ArmCad 2000".
Tower 6 is a graphical program for universal analysis of influences in planar and space structures. By providing strong tools that are automated, integrated, all-inclusive and intuitive, this program enables the engineers to increase the speed and quality of designing. Version 6 is a high performance professional tool, based on experience lasting many years and on the latest knowledge and realization of the expert team, engineers and first-class programmers.
Graphical Interface
• Defining the arbitrary planes for drawing
• Simultaneous use of planar and space drawing
• Selecting precisely the points in the drawing (dynamic osnap with combined criteria)
• Dynamic zoom and pan. Dynamic rotation of isometric presentation of the model (orbit)
• Manipulating the elements in the drawing (copying, mirror copying, deleting, rotating, complete undo/redo system of restoring the drawings, etc.)
• Generating automatically the vertical elements of the structure
• Generating automatically the rotationally symmetric bodies (sphere, cone, vault, helix)
• Operating with blocks of drawings (saving and entering the arbitrarily selected parts of the model)
• Grouping the arbitrarily selected parts of the model into wholes and deleting the visibility to other parts of the model (only columns, walls, typical floor structures, web members, main girders, etc. visible)
• Visualization of the model (DirectX render, walking through building with camera)
Processing the Calculation Results
• Finding quickly the extreme values of influences in the whole model or only in a certain group of elements (extreme values of axial forces in columns only, etc.) maximal bending moments in plates in typical floor, maximal displacements of walls only, etc.)
• Presentation of results, both in the entire space model and in its certain parts (in selected frame, wall, floor structure, foundations, arbitrarily selected view, etc.)
• Presentation of results in surface elements by isolines and diagrams along an arbitrarily assigned intersection line
• Presentation of influences in linear elements by diagrams and color gradientsPresentation of support reactions with direction and intensity
• Diagrams of stress distribution in composite cross-sections through defined stages of constructing
• Influences in individual parts of composite cross section
• Simultaneous presentation of influences in all columns and walls in one level (insight into distribution of influences due to seismic action on all columns and walls in one floor, redistribution of axial forces due to vertical load onto columns and walls of a given level, etc.)
• Presentation and animation of oscillating forms and deformed model
• Completely automatized dimensioning of reinforced concrete, steel and wood structures (JUS, EUROCOD, SNIP, DIN, etc.)
• Adopting reinforcement in reinforced concrete structures with automatic creating of reinforcement details and export to our program "ArmCad 2000".
ShipConstructor-2011-R1.1 download crack
ShipConstructor Software (SSI) has announced the release of ShipConstructor 2011, the newest version of the company’s AutoCAD-based CAD/CAM application for the shipbuilding and offshore industries. The new release incorporates several enhancements that are based upon input to SSI’s Product Management team members who collected feedback and analysed needs from shipbuilders around the world.
“Our latest release supports several of the new features introduced in AutoCAD 2011 to improve the ease of editing,” said Denis Morais, ShipConstructor’s Product Development Manager. “ShipConstructor 2011 also increases speed and improves functionality.”
For instance, in ShipConstructor 2011, the Product Hierarchy Module has been enhanced to now allow users to organise their project in various ways. Multiple hierarchies can now be used to generate production output as well as for analysis. This new feature also empowers shipbuilders to generate multiple build strategies for construction of vessels at different locations.
To ensure that the ShipConstructor SQL database is always optimised for maximum performance, ShipConstructor 2011 now provides a simple method for scheduling database maintenance operations including the cleanup of unused data, compacting of database files, and the re-building of database indexes. This powerful feature can be scheduled to run during down-time, providing the design team with the most well organised and efficient database possible when they return to work.
The Project Revisions dialog has also been enhanced to make it easier to localise and examine project revision history which will aid users in analyzing progress and in tracking potential sources of errors.
The ShipConstructor Project Split & Merge product for multi-site collaboration has also had a performance enhancement in the 2011 version of the software. Merge and refresh speed at distributed locations has been improved by as much as 10 percent.
Information regarding each part’s Global Unique Identifier (GUID) is now more accessible which makes it easier to integrate the ShipConstructor product model with other best-of-breed software such as ERP and FEA applications. Readily accessible GUIDs can also make reporting and macro creation easier, thereby allowing shipyards to customise the software for their own unique requirements.
Additionally, based on customer feedback, ShipConstructor 2011 has expanded its profile endcut definition capabilities. An addition to the software’s parametric features now allows users to create a variety of new types of endcuts being used in today’s offshore and shipbuilding industries.
“Our latest release supports several of the new features introduced in AutoCAD 2011 to improve the ease of editing,” said Denis Morais, ShipConstructor’s Product Development Manager. “ShipConstructor 2011 also increases speed and improves functionality.”
For instance, in ShipConstructor 2011, the Product Hierarchy Module has been enhanced to now allow users to organise their project in various ways. Multiple hierarchies can now be used to generate production output as well as for analysis. This new feature also empowers shipbuilders to generate multiple build strategies for construction of vessels at different locations.
To ensure that the ShipConstructor SQL database is always optimised for maximum performance, ShipConstructor 2011 now provides a simple method for scheduling database maintenance operations including the cleanup of unused data, compacting of database files, and the re-building of database indexes. This powerful feature can be scheduled to run during down-time, providing the design team with the most well organised and efficient database possible when they return to work.
The Project Revisions dialog has also been enhanced to make it easier to localise and examine project revision history which will aid users in analyzing progress and in tracking potential sources of errors.
The ShipConstructor Project Split & Merge product for multi-site collaboration has also had a performance enhancement in the 2011 version of the software. Merge and refresh speed at distributed locations has been improved by as much as 10 percent.
Information regarding each part’s Global Unique Identifier (GUID) is now more accessible which makes it easier to integrate the ShipConstructor product model with other best-of-breed software such as ERP and FEA applications. Readily accessible GUIDs can also make reporting and macro creation easier, thereby allowing shipyards to customise the software for their own unique requirements.
Additionally, based on customer feedback, ShipConstructor 2011 has expanded its profile endcut definition capabilities. An addition to the software’s parametric features now allows users to create a variety of new types of endcuts being used in today’s offshore and shipbuilding industries.
2010/07 0day software ftp download
2010-07-31 LMS Imagine.Lab AMESim R9 SL1
2010-07-30 Camnetics.CamTrax64.v2010.18.64.136
2010-07-28 DriveWorks.Solo.v7.4.0.346
2010-07-25 Bentley Ram Concept V8i 03.04.00.30
2010-07-22 Bentley AutoPIPE V8i 09.02.03.02
2010-07-21 Rocscience.Slide.v6.003
2010-07-20 Cype v2011b
2010-07-19 ShipConstructor 2009
2010-07-18 SigmaNEST 2009
2010-07-17 MoldWorks 2010 SP0 for SolidWorks 2008-2010
2010-07-16 Bentley WaterCAD V8i(SelectSERIES 1) 08.11.01.32
2010-07-15 Siemens.PLM.NX.v7.5.CAST
2010-07-15 Sheetworks v12 SP2
2010-07-14 Autodesk AutoCAD Raster Desigh.v2011
2010-07-14 Bentley MX Tools V8i XM Edition 08.09.04.40
2010-07-14 SPI SheetMetalWorks 2010.1 SP1
2010-07-13 SolidACE BuiltWorks 2010 v1.2 build 3883
2010-07-12 Graphisoft Archicad 14
2010-07-11 CAMWorks 2010 SP1.1 for solidworks
2010-07-11 ESRI ArcPad 10
2010-07-10 AUTODESK ROBOT STRUCTURAL ANALYSIS PRO V2011
2010-07-09 AUTODESK AUTOCAD PLANT3D V2011
2010-07-08 AUTODESK AUTOCAD PID V2011
2010-07-07 Bentley OnSite V8i 08.11.05.28
2010-07-07 Bentley SewerGEMS V8i 08.11.02.46
2010-07-07 GT-Suite 7.0 Gamma Technologies
2010-07-06 Tekla Structures 16.0 SR2
2010-07-05 Bentley SewerGEMS V8i v08.11.02.46
2010-07-04 HSMWorks2010 R2.20781 32bit for SW2007-sw2010
2010-07-02 Dassault.Systemes.3DVIA.Composer.V6R2010x.HF3.v6.5.3.1460
2010-07-01 Simulia.Abaqus.v6.10.1
from caxsoft
2010-07-31 Mentor.Graphics.LP.Wizard.v10.1.1
2010-07-30 Synopsys FPGA v2010.03
2010-07-29 Synopsys Saber vD-2010.03
2010-07-29 Synopsys VCS vD-2010.06
2010-07-25 TannerTools v15.01
2010-07-23 Synopsys FPGA vD-2010.03
2010-07-22 Silvaco TCAD 2010.00
2010-07-20 Agilent.EMPro.2010.07
2010-07-19 GC-PowerStation v9.1.2
2010-07-17 Mentor.Graphics.Hyperlynx.v8.1
2010-07-15 Synopsys Vera vD-2009.12
2010-07-11 Altium Designer Winter v10
2010-07-10 Altera.Quartus II v10.0
2010-07-09 CST Studio Suite 2010 SP4
2010-07-08 Synopsys Hspice vD-2010.03 SP1
2010-07-08 Synopsys PTS vD-2010.06 Linux
2010-07-08 Synopsys SpiceExplore vD-2010.06
2010-07-05 Mentor.Graphics PADS 9.2
2010-07-05 Cadence spb 16.30.011 hotfix
2010-07-02 Altera Edition ModelSim v6.5e
2010-07-01 ANSOFT MAXWELL V13
form caxcrack
2010-07-30 Camnetics.CamTrax64.v2010.18.64.136
2010-07-28 DriveWorks.Solo.v7.4.0.346
2010-07-25 Bentley Ram Concept V8i 03.04.00.30
2010-07-22 Bentley AutoPIPE V8i 09.02.03.02
2010-07-21 Rocscience.Slide.v6.003
2010-07-20 Cype v2011b
2010-07-19 ShipConstructor 2009
2010-07-18 SigmaNEST 2009
2010-07-17 MoldWorks 2010 SP0 for SolidWorks 2008-2010
2010-07-16 Bentley WaterCAD V8i(SelectSERIES 1) 08.11.01.32
2010-07-15 Siemens.PLM.NX.v7.5.CAST
2010-07-15 Sheetworks v12 SP2
2010-07-14 Autodesk AutoCAD Raster Desigh.v2011
2010-07-14 Bentley MX Tools V8i XM Edition 08.09.04.40
2010-07-14 SPI SheetMetalWorks 2010.1 SP1
2010-07-13 SolidACE BuiltWorks 2010 v1.2 build 3883
2010-07-12 Graphisoft Archicad 14
2010-07-11 CAMWorks 2010 SP1.1 for solidworks
2010-07-11 ESRI ArcPad 10
2010-07-10 AUTODESK ROBOT STRUCTURAL ANALYSIS PRO V2011
2010-07-09 AUTODESK AUTOCAD PLANT3D V2011
2010-07-08 AUTODESK AUTOCAD PID V2011
2010-07-07 Bentley OnSite V8i 08.11.05.28
2010-07-07 Bentley SewerGEMS V8i 08.11.02.46
2010-07-07 GT-Suite 7.0 Gamma Technologies
2010-07-06 Tekla Structures 16.0 SR2
2010-07-05 Bentley SewerGEMS V8i v08.11.02.46
2010-07-04 HSMWorks2010 R2.20781 32bit for SW2007-sw2010
2010-07-02 Dassault.Systemes.3DVIA.Composer.V6R2010x.HF3.v6.5.3.1460
2010-07-01 Simulia.Abaqus.v6.10.1
from caxsoft
2010-07-31 Mentor.Graphics.LP.Wizard.v10.1.1
2010-07-30 Synopsys FPGA v2010.03
2010-07-29 Synopsys Saber vD-2010.03
2010-07-29 Synopsys VCS vD-2010.06
2010-07-25 TannerTools v15.01
2010-07-23 Synopsys FPGA vD-2010.03
2010-07-22 Silvaco TCAD 2010.00
2010-07-20 Agilent.EMPro.2010.07
2010-07-19 GC-PowerStation v9.1.2
2010-07-17 Mentor.Graphics.Hyperlynx.v8.1
2010-07-15 Synopsys Vera vD-2009.12
2010-07-11 Altium Designer Winter v10
2010-07-10 Altera.Quartus II v10.0
2010-07-09 CST Studio Suite 2010 SP4
2010-07-08 Synopsys Hspice vD-2010.03 SP1
2010-07-08 Synopsys PTS vD-2010.06 Linux
2010-07-08 Synopsys SpiceExplore vD-2010.06
2010-07-05 Mentor.Graphics PADS 9.2
2010-07-05 Cadence spb 16.30.011 hotfix
2010-07-02 Altera Edition ModelSim v6.5e
2010-07-01 ANSOFT MAXWELL V13
form caxcrack
2010-07-15
DHI-Wasy-FEFLOW-6.0-CRACK
FEFLOW 6 is available for download from the download web page.
All users with a current SMA will receive their new license automatically by e-mail. User manual and release DVD will be sent out in May and June 2010.
The transition to FEFLOW 6 is safe and easy; it is fully compatible with older model files without any loss of computational efficiency. Furthermore, it still contains the classic user interface known from 5.x-versions as a fall-back for experienced users.
A New Working Environment
FEFLOW 6 represents a break with the FEFLOW appearance that has become familiar to many users over the years. The new user interface provides powerful new features and a more intuitive workflow. Designed to give the modeler more degrees of freedom together with the accompanying means of control, FEFLOW 6 keeps all functionality accessible whenever possible to ensure maximum flexibility and efficiency—with all the visualization capabilities that were previously provided by FEFLOW Explorer now fully incorporated!
Some of the new features and improvements compared to versions 5.x:
o Multiple simultaneous view windows (supermesh, 2D, 3D and cross-section views)
o Interactive and flexible visualization of parameters, maps, and 3D GIS/CAD data
o Parameter assignment on arbitrary selections of nodes/elements
o Multilevel undo/redo functionality
o OpenGL graphics acceleration
Want to Know More?
An extensive overview of the new features is given in the Special International Edition of our company’s news periodical "DHI-WASY Aktuell" published at the last FEFLOW conference. [more](pdf)
Probably the best way to get familiar with the new user interface is to give it a try yourself. Download and install FEFLOW 6 from our website. Those who do not own a license can start FEFLOW in demonstration mode. A comprehensive collection of demonstration data as well as a tutorial exercise are available to explore the new possibilities. [more]
Have a look at the FEFLOW 6 documentation for a complete overview of new features. [more]
All users with a current SMA will receive their new license automatically by e-mail. User manual and release DVD will be sent out in May and June 2010.
The transition to FEFLOW 6 is safe and easy; it is fully compatible with older model files without any loss of computational efficiency. Furthermore, it still contains the classic user interface known from 5.x-versions as a fall-back for experienced users.
A New Working Environment
FEFLOW 6 represents a break with the FEFLOW appearance that has become familiar to many users over the years. The new user interface provides powerful new features and a more intuitive workflow. Designed to give the modeler more degrees of freedom together with the accompanying means of control, FEFLOW 6 keeps all functionality accessible whenever possible to ensure maximum flexibility and efficiency—with all the visualization capabilities that were previously provided by FEFLOW Explorer now fully incorporated!
Some of the new features and improvements compared to versions 5.x:
o Multiple simultaneous view windows (supermesh, 2D, 3D and cross-section views)
o Interactive and flexible visualization of parameters, maps, and 3D GIS/CAD data
o Parameter assignment on arbitrary selections of nodes/elements
o Multilevel undo/redo functionality
o OpenGL graphics acceleration
Want to Know More?
An extensive overview of the new features is given in the Special International Edition of our company’s news periodical "DHI-WASY Aktuell" published at the last FEFLOW conference. [more](pdf)
Probably the best way to get familiar with the new user interface is to give it a try yourself. Download and install FEFLOW 6 from our website. Those who do not own a license can start FEFLOW in demonstration mode. A comprehensive collection of demonstration data as well as a tutorial exercise are available to explore the new possibilities. [more]
Have a look at the FEFLOW 6 documentation for a complete overview of new features. [more]
OPEN-MIND-hyperMILL-2009.2
High-performing software components
OPEN MIND Technologies AG is a leading developer of CAD/CAM software and postprocessors for designing and manufacturing complex moulds and parts.
With hyperCAD®, 2D and 3D models can be easily designed and machined. With its wealth of innovative software components, OPEN MIND offers a CAM solution that is optimal for the range of tasks, manufacturing processes and IT organisation at any company. Above all, improved and alternative machining workflows contribute decisively to enhanced process efficiency. The hyperMILL® CAM software provides a broad spectrum of machining strategies and optimisation functions that enable flexible and efficient programming of the most complicated parts: from 2D, 3D, HSC milling and 5axis simultaneous machining, to mill turning with the millTURN module, to special applications for geometries such as impellers, blisks, blades, tubes and tyres.
Complete machining with just one CAM software on one uniform user interface results in integrated processes and minimised machining times, and increases reliability – for maximum process safety, cost efficiency and quality. CAM utilities and postprocessors prepare the way from CAM to NC programmes that are perfectly suited to the machine, controller and the parts spectrum.
OPEN MIND Technologies AG is a leading developer of CAD/CAM software and postprocessors for designing and manufacturing complex moulds and parts.
With hyperCAD®, 2D and 3D models can be easily designed and machined. With its wealth of innovative software components, OPEN MIND offers a CAM solution that is optimal for the range of tasks, manufacturing processes and IT organisation at any company. Above all, improved and alternative machining workflows contribute decisively to enhanced process efficiency. The hyperMILL® CAM software provides a broad spectrum of machining strategies and optimisation functions that enable flexible and efficient programming of the most complicated parts: from 2D, 3D, HSC milling and 5axis simultaneous machining, to mill turning with the millTURN module, to special applications for geometries such as impellers, blisks, blades, tubes and tyres.
Complete machining with just one CAM software on one uniform user interface results in integrated processes and minimised machining times, and increases reliability – for maximum process safety, cost efficiency and quality. CAM utilities and postprocessors prepare the way from CAM to NC programmes that are perfectly suited to the machine, controller and the parts spectrum.
2010.06 0day software download
2010-06-30 Spi sheetmetalworks 2010
2010-06-30 Pointwise.v16.03R3
2010-06-29 MapInfo.Pro.2010.v10.5.19
2010-06-28 PTC.Mathcad.v15.0
2010-06-27 MVTec Halcon v9.0.2
2010-06-26 Delcam Exchange 2010 v623004
2010-06-24 Bentley CulvertMaster v03.03.00.04
2010-06-24 Bentley Electric V8i v08.11.07.56
2010-06-23 Geometric.Technologies.CAMWorks.2009.SP3.2
2010-06-22 Camnetics.GearTeq.v2010.18.32.319
2010-06-22 DriveWorks.Solo.v7.3.0.119
2010-06-21 Archon.STB.V6.0
2010-06-20 3D-COAT v3.3.04 Linux X86 and X64
2010-06-19 VS.3D.Fledermaus.Professional.v7.1.1.b.462
2010-06-18 CAMWorks 2010 SP1.0 for SolidWorks win32&64
2010-06-17 Graitec OMD 2009 v17.1
2010-06-16 Leica Cyclone v7.0.3.1431
2010-06-16 Lectra Modaris v6R1C1
2010-06-15 Progesoft.ProgeCAD.2010.Pro.v10.0.6.23
2010-06-14 Graphisoft.Archicad.13.3
2010-06-13 Progesoft.ProgeCAD.2010
2010-06-12 ADEM v9.0
2010-06-11 Autodesk.MapGuide.Enterprise.V2011
2010-06-10 AutoformPlus R2
2010-06-09 STAR-CD v4.12.016 FOR Win32&Win64
2010-06-08 Cubus cedrus v4.0
2010-06-06 3D-COAT v3.3.01 FOR Linux&Win
2010-06-05 Revworks 2001 SP1 for Solidworks
2010-06-04 IMSpost pro 7.4
2010-06-03 Autodesk MapGuide Enterprise 2011 v2.2.0.5305 Win x86/x64
2010-06-03 iMold v10 SP1.0 for solidworks2007-2010
2010-06-02 XYZ TrueGrid v2.3.4
2010-06-02 Geocentrix ReWaRD v2.5.21
2010-06-01 AUTODESK.AUTOCAD.STRUCTURAL.DETAILING.V2011
caxcrack from
2010-06-30 Dolphin.Integration.SoC.GDS.v6.6.0
2010-06-29 Dolphin.Integration.Smash.v5.15.0
2010-06-28 Mentor.Graphics.Calibre.v2010.1.22.19
2010-06-27 Mentor.Graphics.Flotherm v9.1
2010-06-26 Flowcode for AVR v4.3.6.61
2010-06-23 Synopsys Leda vD-2010.03
2010-06-20 Synopsys.Hspice vD-2010.03.SP1
2010-06-19 Coware spw 2010
2010-06-15 Synopsys Primetime vD-2009.12 SP3
2010-06-10 Proteus 7.7 with SP2
2010-06-07 Altium Designer Summer 09 Build v9.4.0.20159
2010-06-04 Cadence EXT v09.12.001
2010-06-02 Dolphin.Integration.Smash.v5.14.2
2010-06-01 IAR Embedded Workbench for 8051 751A
2010-06-30 Pointwise.v16.03R3
2010-06-29 MapInfo.Pro.2010.v10.5.19
2010-06-28 PTC.Mathcad.v15.0
2010-06-27 MVTec Halcon v9.0.2
2010-06-26 Delcam Exchange 2010 v623004
2010-06-24 Bentley CulvertMaster v03.03.00.04
2010-06-24 Bentley Electric V8i v08.11.07.56
2010-06-23 Geometric.Technologies.CAMWorks.2009.SP3.2
2010-06-22 Camnetics.GearTeq.v2010.18.32.319
2010-06-22 DriveWorks.Solo.v7.3.0.119
2010-06-21 Archon.STB.V6.0
2010-06-20 3D-COAT v3.3.04 Linux X86 and X64
2010-06-19 VS.3D.Fledermaus.Professional.v7.1.1.b.462
2010-06-18 CAMWorks 2010 SP1.0 for SolidWorks win32&64
2010-06-17 Graitec OMD 2009 v17.1
2010-06-16 Leica Cyclone v7.0.3.1431
2010-06-16 Lectra Modaris v6R1C1
2010-06-15 Progesoft.ProgeCAD.2010.Pro.v10.0.6.23
2010-06-14 Graphisoft.Archicad.13.3
2010-06-13 Progesoft.ProgeCAD.2010
2010-06-12 ADEM v9.0
2010-06-11 Autodesk.MapGuide.Enterprise.V2011
2010-06-10 AutoformPlus R2
2010-06-09 STAR-CD v4.12.016 FOR Win32&Win64
2010-06-08 Cubus cedrus v4.0
2010-06-06 3D-COAT v3.3.01 FOR Linux&Win
2010-06-05 Revworks 2001 SP1 for Solidworks
2010-06-04 IMSpost pro 7.4
2010-06-03 Autodesk MapGuide Enterprise 2011 v2.2.0.5305 Win x86/x64
2010-06-03 iMold v10 SP1.0 for solidworks2007-2010
2010-06-02 XYZ TrueGrid v2.3.4
2010-06-02 Geocentrix ReWaRD v2.5.21
2010-06-01 AUTODESK.AUTOCAD.STRUCTURAL.DETAILING.V2011
caxcrack from
2010-06-30 Dolphin.Integration.SoC.GDS.v6.6.0
2010-06-29 Dolphin.Integration.Smash.v5.15.0
2010-06-28 Mentor.Graphics.Calibre.v2010.1.22.19
2010-06-27 Mentor.Graphics.Flotherm v9.1
2010-06-26 Flowcode for AVR v4.3.6.61
2010-06-23 Synopsys Leda vD-2010.03
2010-06-20 Synopsys.Hspice vD-2010.03.SP1
2010-06-19 Coware spw 2010
2010-06-15 Synopsys Primetime vD-2009.12 SP3
2010-06-10 Proteus 7.7 with SP2
2010-06-07 Altium Designer Summer 09 Build v9.4.0.20159
2010-06-04 Cadence EXT v09.12.001
2010-06-02 Dolphin.Integration.Smash.v5.14.2
2010-06-01 IAR Embedded Workbench for 8051 751A
Mentor-Graphics-PADS-9.2-download
Mentor Graphics PADS offers a comprehensive PCB design solution by combining schematic definitions with tools for the layout and simulation. keytech PLM provides strong integration with Mentor Graphics PADS solution (PowerLAYOUT & PowerLOGIC) into the product lifecycle management, ensuring complete revision management of all projects and documents.
* The master items are only maintained once in PLM resulting in a single interface for the ERP systems and the automated transfer of master item data to PADS
* Automated transfer of master item data to PADS
* Management and archiving of PADS projects
* PADS projects are completely controlled by keytech PLM
* Bill of material output from the PADS project becomes part of the PLM product structure
* The master items are only maintained once in PLM resulting in a single interface for the ERP systems and the automated transfer of master item data to PADS
* Automated transfer of master item data to PADS
* Management and archiving of PADS projects
* PADS projects are completely controlled by keytech PLM
* Bill of material output from the PADS project becomes part of the PLM product structure
Metalix-cncKad-2010-v10
The cncKad Software provides an integrated system covering the complete cycle of CNC operations, and includes the following modules:
Drafting – powerful, yet easy to use, 2D Drafting module, with a full set of drafting tools and special sheet-metal drafting aids including: notching, chamfering, filleting, automatic detection and correction of unclosed contours, shape recognition, geometry validation, and utilizing true-type fonts.
Processing – automatic and interactive graphical processing for Punch, Laser, Plasma, Water Jet and Flame technologies including: automatic reposition, clamp-avoidance, stripes, trimming, support for Wilson Wheel family, minimizing tool rotation, and detailed data reports. This module supports also auto-punch, auto-cut, special tools, auto-index, reposition, and common cuts.
AutoNest – Automatic "true-shape" Nesting for optimal material utilization, including: interactivity, grouping, grill, hole-filling, multiple-sheets, automatic DXF to NC solution, and detailed data reports.
Post-Processing – advanced Post-processors generate efficient NC code including: macros, optimized tool path, minimal turret rotation, and support for machine operations such as oiling, vacuum and ram-rate.
Simulation – Graphic Simulation of NC program enables easy editing while viewing the processed sheet. The program is automatically checked for errors, such as: missing parameters, clamp errors, over-travel errors, and more.
The "NC to DFT" option enables importing legacy NC programs and simulating them as well.
DNC – the DNC module supports uploading and downloading of NC files to machine as well as support for batch loading and extracting NC files from the machine controller.
Import and Export – 3D integration with Solid Works®, SolidEdge®, Autodesk® Inventor® and ProE® through a real-time associative link and reading files directly from AutoCAD®.
Multi-language support - except for English, the software is available in various languages such as: Arabic, Chinese, Czech, Dutch, French, German, Greek, Italian, Japanese, Korean, Polish, Portugese, Romanian, Russian, Slovak, Spanish, Taiwanese, Thai and Turkish.
cncKad also offers Parametric Programming, advanced processing technologies and support for a wide range of machines.
Drafting – powerful, yet easy to use, 2D Drafting module, with a full set of drafting tools and special sheet-metal drafting aids including: notching, chamfering, filleting, automatic detection and correction of unclosed contours, shape recognition, geometry validation, and utilizing true-type fonts.
Processing – automatic and interactive graphical processing for Punch, Laser, Plasma, Water Jet and Flame technologies including: automatic reposition, clamp-avoidance, stripes, trimming, support for Wilson Wheel family, minimizing tool rotation, and detailed data reports. This module supports also auto-punch, auto-cut, special tools, auto-index, reposition, and common cuts.
AutoNest – Automatic "true-shape" Nesting for optimal material utilization, including: interactivity, grouping, grill, hole-filling, multiple-sheets, automatic DXF to NC solution, and detailed data reports.
Post-Processing – advanced Post-processors generate efficient NC code including: macros, optimized tool path, minimal turret rotation, and support for machine operations such as oiling, vacuum and ram-rate.
Simulation – Graphic Simulation of NC program enables easy editing while viewing the processed sheet. The program is automatically checked for errors, such as: missing parameters, clamp errors, over-travel errors, and more.
The "NC to DFT" option enables importing legacy NC programs and simulating them as well.
DNC – the DNC module supports uploading and downloading of NC files to machine as well as support for batch loading and extracting NC files from the machine controller.
Import and Export – 3D integration with Solid Works®, SolidEdge®, Autodesk® Inventor® and ProE® through a real-time associative link and reading files directly from AutoCAD®.
Multi-language support - except for English, the software is available in various languages such as: Arabic, Chinese, Czech, Dutch, French, German, Greek, Italian, Japanese, Korean, Polish, Portugese, Romanian, Russian, Slovak, Spanish, Taiwanese, Thai and Turkish.
cncKad also offers Parametric Programming, advanced processing technologies and support for a wide range of machines.
Barco-Ucam-v8.5.1-download
Ucamco clears more front-end engineering bottlenecks with Ucam v8.5
The latest release of Ucamco’s UCAM PCB CAM software delivers increased productivity
in two areas which have historically restricted front-end engineering throughput: the
preparation of complex rout profiles for rigid and flexible boards, and design optimization
to increase fabrication yields.
Ucamco has rolled out an aggressive schedule of new software releases, training
programs and webinars since it was re-founded as an independent provider in 2008.
Each step has been based on the identification of a PCB front-end engineering
bottleneck and the development of an appropriate solution to clear it.
Preparing accurate profiling tools for complex-shaped PCBs has always been a slow
process. It requires entering complex data from the customer’s drawing, preparing the
tool data and then checking it back against the original drawing. UCAM Version 8.5.1
provides a practical real-world solution. The customer’s PDF drawing is displayed
directly on-screen. New profiling functionality allows the engineer to snap his profile-tool
data from point to point on the drawing. Clear function icons eliminate the need for
complex off-screen calculations of radii, chamfered corners etc. Flexible new
dimensioning software highlights critical dimensions to check back against the
customer’s drawing, and generates clear drawings for shop-floor verification of the
finished board. As all system fonts are supported, drawings can be easily annotated in
any local language.
Design rule violation repair and design optimization for manufacturability are two
important customer services to generate repeat business for PCB fabricators. As each
type of PCB and each customer have individual requirements, a “one size fits all” solution
does not work. UCAM’s new on-screen set-up allows the fabricator to define and store a
precise set of repair and optimization strategies immediately they are required and
without time-consuming programming. The stored procedures then run fully
automatically to deliver increased yield for the fabricator and for the customer lower
prices and enhanced end-product reliability.
Ucamco (former Barco ETS) is a market leader in PCB CAM software and laser
photoplotting systems. We have more than 25 years continuous experience developing
and supporting leading-edge front-end tooling solutions for the global PCB industry. We help fabricators world-wide raise yields, increase factory productivity, and cut enterprise risks and costs.
The latest release of Ucamco’s UCAM PCB CAM software delivers increased productivity
in two areas which have historically restricted front-end engineering throughput: the
preparation of complex rout profiles for rigid and flexible boards, and design optimization
to increase fabrication yields.
Ucamco has rolled out an aggressive schedule of new software releases, training
programs and webinars since it was re-founded as an independent provider in 2008.
Each step has been based on the identification of a PCB front-end engineering
bottleneck and the development of an appropriate solution to clear it.
Preparing accurate profiling tools for complex-shaped PCBs has always been a slow
process. It requires entering complex data from the customer’s drawing, preparing the
tool data and then checking it back against the original drawing. UCAM Version 8.5.1
provides a practical real-world solution. The customer’s PDF drawing is displayed
directly on-screen. New profiling functionality allows the engineer to snap his profile-tool
data from point to point on the drawing. Clear function icons eliminate the need for
complex off-screen calculations of radii, chamfered corners etc. Flexible new
dimensioning software highlights critical dimensions to check back against the
customer’s drawing, and generates clear drawings for shop-floor verification of the
finished board. As all system fonts are supported, drawings can be easily annotated in
any local language.
Design rule violation repair and design optimization for manufacturability are two
important customer services to generate repeat business for PCB fabricators. As each
type of PCB and each customer have individual requirements, a “one size fits all” solution
does not work. UCAM’s new on-screen set-up allows the fabricator to define and store a
precise set of repair and optimization strategies immediately they are required and
without time-consuming programming. The stored procedures then run fully
automatically to deliver increased yield for the fabricator and for the customer lower
prices and enhanced end-product reliability.
Ucamco (former Barco ETS) is a market leader in PCB CAM software and laser
photoplotting systems. We have more than 25 years continuous experience developing
and supporting leading-edge front-end tooling solutions for the global PCB industry. We help fabricators world-wide raise yields, increase factory productivity, and cut enterprise risks and costs.
2010-06-24
Ommi-3d-design-v10-crack
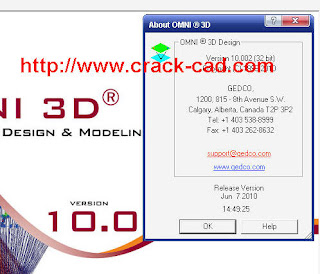
OMNI 3D is the industry standard for seismic survey design and modeling. Developed by geophysicists for geophysicists, OMNI 3D is used by hundreds of specialists around the globe for the planning, execution, and analysis of land, marine, transition zone, VSP, and multi-component surveys. OMNI 3D features a superior user interface and a versatile multi-project handling capability, both of which allow users to quickly and effectively analyze and monitor their seismic acquisition projects.
Design & Edit Module
§ Design Land, VSP, Streamer, OBC, and OBS survey
geometries with easy to use design wizards
§ Create scripts using simple or complex shooting schemes
§ Edit surveys using sophisticated editing tools
§ Analyze and compare multiple survey geometries
§ Import and export data in all common formats
§ Integrate DXF, TIFF, shapefile, and other culture data in
multi-layered projects
§ Output complex scaled plots, including user-defined
labels and annotation to any Windows printer
Target Module
§ Create 3D target horizon models using imported horizon
data
§ Calculate survey design parameters such as bin size,
maximum offset, and migration aperture required to
illuminate the target horizon
link for dwcrk.com
2010-06-18
AutoFormplus-R2-download
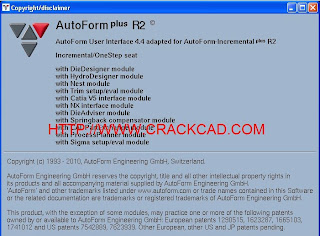
AutoFormplus R2 – Outstanding Speed Performance
AutoForm Engineering GmbH, the leading supplier of software solutions for the sheet metal forming industry, has unveiled the latest software version AutoFormplus R2. This release focuses primarily on superior speed performance. Apart from this extraordinary achievement, AutoFormplus R2 brings further powerful benefits to the users.
AutoFormplus R2 is the second major release of the new product line AutoFormplus. It is characterized by an outstanding speed performance, which is achieved as a result of the redesigned software architecture. When using elastic plastic shell elements and bending enhanced membrane elements, the speed of the solver is now increased by an average of 30% and 12%, respectively. This improvement in speed is made without compromising the accuracy of the results.
AutoFormplus R2 brings further new features and benefits, such as accurate material modeling for stainless steel 1.4301, refined drawbead model, addendum profile templates and option for hidden internal cost data. Further progress has also been made in springback compensation. As a result, the user can implement more advanced compensation strategies to address complex issues that arise in practice.
Ansoft-Simplorer-8.1-download
Simplorer is a multi-domain system simulation software program. It is used for the design, modeling, analysis and optimization of high-performance systems that include electrical, thermal, electromechanical, electromagnetic, and hydraulic designs. These complex systems are commonly found in the automotive, aerospace/defense, and industrial automation industries.
Simplorer provides a wide range of modeling techniques, analysis capabilities, and post processing. This enables the engineer to investigate system functionality, performance, and overall design verification. The result is a dramatic reduction in development time and cost, increased system reliability and system optimization.
New in Simplorer v8.1
* ANSYS Icepak® and ANSYS Mechanical® coupling
* State Space Modeling Capability
* Simplorer stand alone or Maxwell Transient co-simulation Saved States
* Set Assignments
* Dynamic Updates for Plots
* Enhanced "Output Dialog" window
* Evaluated Value display on schematic
* Sub-Circuit Buses
* Library Management Enhancemen
Simplorer provides a wide range of modeling techniques, analysis capabilities, and post processing. This enables the engineer to investigate system functionality, performance, and overall design verification. The result is a dramatic reduction in development time and cost, increased system reliability and system optimization.
New in Simplorer v8.1
* ANSYS Icepak® and ANSYS Mechanical® coupling
* State Space Modeling Capability
* Simplorer stand alone or Maxwell Transient co-simulation Saved States
* Set Assignments
* Dynamic Updates for Plots
* Enhanced "Output Dialog" window
* Evaluated Value display on schematic
* Sub-Circuit Buses
* Library Management Enhancemen
Ansoft-Maxwell-13-download
Maxwell® is the premier electromagnetic field simulation software for engineers tasked with designing and analyzing 3-D and 2-D electromagnetic and electromechanical devices such as motors, actuators, transformers, sensors and coils. Maxwell uses the accurate finite element method to solve static, frequency-domain and time-varying electromagnetic and electric fields. A key benefit of Maxwell is its automated solution process where users are only required to specify geometry, material properties and the desired output. From this point, Maxwell will automatically generate an appropriate, efficient and accurate mesh for solving the problem. This proven automatic adaptive meshing process removes complexity from the analysis process and allows engineers to benefit from a highly-efficient, easy-to-use design flow.
What's new in 13.0?
* Complete Maxwell 3-D project setup by RMxprt™ including geometry, materials, boundary conditions including the appropriate symmetries and excitations with coupling circuit topology
* Maxwell can be linked with ANSYS® Mechanical™ to perform thermal and stress analysis.
* Greater than 5X speed up in magnetic transient solver with rigid body motion
* Highly robust volumetric meshing (TAU) technique
* Maxwell 3-D transient with motion co-simulation with Simplorer
* 3D Skin-depth adaptive meshing
* Time varying solid winding source with more than two terminals
* Demagnetization to 3rd Quadrant
* Element-by-element magnetization capability based on the original non-remnant B(H)-curve
What's new in 13.0?
* Complete Maxwell 3-D project setup by RMxprt™ including geometry, materials, boundary conditions including the appropriate symmetries and excitations with coupling circuit topology
* Maxwell can be linked with ANSYS® Mechanical™ to perform thermal and stress analysis.
* Greater than 5X speed up in magnetic transient solver with rigid body motion
* Highly robust volumetric meshing (TAU) technique
* Maxwell 3-D transient with motion co-simulation with Simplorer
* 3D Skin-depth adaptive meshing
* Time varying solid winding source with more than two terminals
* Demagnetization to 3rd Quadrant
* Element-by-element magnetization capability based on the original non-remnant B(H)-curve
2010-06-08
LISCAD-9.02-keygen
LEICA LISCAD
Designed by Surveyors and Engineers
You’ve collected your data. The hard work is done. Or so
you think. Without the right software to process that data,
you could end up in a real mess. LEICA LISCAD is a purpo-
se made piece of software for the Engineer and Surveyor.
Data from virtually any surveying instrument can be impor-
ted and turned into finished plans so easily, you’ll wonder
how you ever managed without it.
Because LISCAD is purely a surveying and engineering
software, you only pay for what you need. In contrast to
add-on packages for drawing programs, there are no
superfluous functions that you will never use. The data-
base has been designed with surveying and engineering
tasks specifically in mind. This means it’s faster. Data is
imported straight in from Leica Geosystems instruments
with no potentially disastrous reformatting.
Computations (COGO)
Create and edit and examine points, lines, splines, poly-
gons, text and alignments. The WYSIWYG (What you see is
what you get) graphics mean you always know exactly
where you are. Moreover, a range of powerful computa-
tion options for points, circles, arcs, splines and spirals
simplifies and speeds up your work. Create line segments,
best fit lines or arcs through a series of existing points and
create polygons for cadastral work. Its all so easy. All attri-
butes attached to a point can be displayed through a single
mouse click. Editing of points can also be carried out en
masse by block, code, point range, description or group.
Background Images
Background Images, allows the import of aerial photo-
graphs, satellite images and maps, which can be geo-
referenced. This allows for the correlation of images
to your vector geometry, as well as on-screen digitizing.
Designed by Surveyors and Engineers
You’ve collected your data. The hard work is done. Or so
you think. Without the right software to process that data,
you could end up in a real mess. LEICA LISCAD is a purpo-
se made piece of software for the Engineer and Surveyor.
Data from virtually any surveying instrument can be impor-
ted and turned into finished plans so easily, you’ll wonder
how you ever managed without it.
Because LISCAD is purely a surveying and engineering
software, you only pay for what you need. In contrast to
add-on packages for drawing programs, there are no
superfluous functions that you will never use. The data-
base has been designed with surveying and engineering
tasks specifically in mind. This means it’s faster. Data is
imported straight in from Leica Geosystems instruments
with no potentially disastrous reformatting.
Computations (COGO)
Create and edit and examine points, lines, splines, poly-
gons, text and alignments. The WYSIWYG (What you see is
what you get) graphics mean you always know exactly
where you are. Moreover, a range of powerful computa-
tion options for points, circles, arcs, splines and spirals
simplifies and speeds up your work. Create line segments,
best fit lines or arcs through a series of existing points and
create polygons for cadastral work. Its all so easy. All attri-
butes attached to a point can be displayed through a single
mouse click. Editing of points can also be carried out en
masse by block, code, point range, description or group.
Background Images
Background Images, allows the import of aerial photo-
graphs, satellite images and maps, which can be geo-
referenced. This allows for the correlation of images
to your vector geometry, as well as on-screen digitizing.
2010 05 0DAY crack software
2010-05-31 TurboFLOORPLAN.3D.Home.Landscape.Pro.v15
2010-05-30 DesignBuilder.v2.2.5
2010-05-29 Delcam v16.08 for SolidWorks2009-2010
2010-05-27 Next Limit RealFlow v5.0
2010-05-26 SpaceClaim.v2009.Plus.SP2.x86
2010-05-25 Tripos.SYBYL-X.v1.1.1.126
2010-05-24 DSS CATIA V5R20 SP2 (Win32 & Win64)
2010-05-23 IVS.3D.Fledermaus.Professional.v7.1.1.429
2010-05-22 Aquaveo.GMS v7.1.2 Upldate
2010-05-22 Aquaveo.SMS v10.1.6 Upldate
2010-05-21 sp3.1 for Dassault Systemes SolidWorks v2010 x86+x64
2010-05-20 OriginLab.OriginPro.v8.1 with SR3
2010-05-19 Tekla.Structures.V16.SR1
2010-05-18 MSC.Dytran.v2010
2010-05-18 MSC.MARC.AND.MARC.MENTAT.V2010
2010-05-18 MSC.EASY5.V2010
2010-05-17 MSC.PATRAN.V2010
2010-05-17 SIEMENS.PLM.NX.V7.5
2010-05-16 Tecplot.RS.v2010.1.1.7630.x64
2010-05-15 Logopress3 2010 for solidworks SP0.8 to 0.8.1
2010-05-14 LISCAD 9.0.2
2010-05-13 AUTODESK.ALIAS.SKETCH.V2011
2010-05-12 Autodesk Ecotect Analysis 2011
2010-05-12 ArtCAM.Pro.v2010
2010-05-11 Logopress3 2010 SP0.8 for SW2009-2010
2010-05-10 Premier.System.X3.764.iSO.Multilanguage
2010-05-09 CAMWorks 2010 SP0.1 Multilanguage for SolidWorks 2009-2010
2010-05-08 SpaceClaim.v2009.Plus.SP2
2010-05-07 DFMPro.for.SolidWorks.SP1.v2.1.250
2010-05-06 OPTIS SPEOS CAA V5 Based V8.0
2010-05-06 OPTIS SPEOS for Pro/ENGINEER ® 2010
2010-05-06 OptisWorks Studio 2010
2010-05-05 DesignBuilder.v2.2.4.001
2010-05-04 Appligent.AppendPDF.Pro.v5.1.Cracked
2010-05-04 Gurobi.Optimization.Gurobi.for.AMPL.v3.0.0.Cracked
2010-05-03 FLOWSCIENCE.FLOW-3D.V9.3.2
2010-05-03 Quint Optishape-TS 2010 R1
2010-05-03 CHAM.PHOENICS.V2009
2010-05-02 FLUIDON.DSHPLUS.V3.6.2
2010-05-02 ARUP_OASYS_V9.4.1
2010-05-01 QForm v5.10
from caxsoft
2010-05-30 Agilent.EMPro.v2010
2010-05-27 E3.series.2010.v900
2010-05-23 IAR.Embedded.Workbench.For.ARM.V5.501
2010-05-23 IAR.Embedded.Workbench.For.Msp430.V5.1
2010-05-20 Agilent 89600 Vector Signal Analyzer v12.00
2010-05-17 IAR Embedded Workbench for Atmel AVR v5.50.1
2010-05-14 Novas v2010.04
2010-05-09 Xilinx.ISE.Design.Suite.v12.1 for Linux &Win
2010-05-08 Mentor.Graphics.ModelSIM.SE.6.6a
2010-05-07 Tanner LEdit 15.0
2010-05-05 BluePrint-PCB.v2.2.1.506.with.CAM350.v10.2.1.389
2010-05-03 Mentor Graphics SystemVision v5.5
2010-05-02 CoWare SPW 2010.1 Linux
2010-04-29 Mentor.Graphics.Seamless.CVE.v5.4s
2010-05-30 DesignBuilder.v2.2.5
2010-05-29 Delcam v16.08 for SolidWorks2009-2010
2010-05-27 Next Limit RealFlow v5.0
2010-05-26 SpaceClaim.v2009.Plus.SP2.x86
2010-05-25 Tripos.SYBYL-X.v1.1.1.126
2010-05-24 DSS CATIA V5R20 SP2 (Win32 & Win64)
2010-05-23 IVS.3D.Fledermaus.Professional.v7.1.1.429
2010-05-22 Aquaveo.GMS v7.1.2 Upldate
2010-05-22 Aquaveo.SMS v10.1.6 Upldate
2010-05-21 sp3.1 for Dassault Systemes SolidWorks v2010 x86+x64
2010-05-20 OriginLab.OriginPro.v8.1 with SR3
2010-05-19 Tekla.Structures.V16.SR1
2010-05-18 MSC.Dytran.v2010
2010-05-18 MSC.MARC.AND.MARC.MENTAT.V2010
2010-05-18 MSC.EASY5.V2010
2010-05-17 MSC.PATRAN.V2010
2010-05-17 SIEMENS.PLM.NX.V7.5
2010-05-16 Tecplot.RS.v2010.1.1.7630.x64
2010-05-15 Logopress3 2010 for solidworks SP0.8 to 0.8.1
2010-05-14 LISCAD 9.0.2
2010-05-13 AUTODESK.ALIAS.SKETCH.V2011
2010-05-12 Autodesk Ecotect Analysis 2011
2010-05-12 ArtCAM.Pro.v2010
2010-05-11 Logopress3 2010 SP0.8 for SW2009-2010
2010-05-10 Premier.System.X3.764.iSO.Multilanguage
2010-05-09 CAMWorks 2010 SP0.1 Multilanguage for SolidWorks 2009-2010
2010-05-08 SpaceClaim.v2009.Plus.SP2
2010-05-07 DFMPro.for.SolidWorks.SP1.v2.1.250
2010-05-06 OPTIS SPEOS CAA V5 Based V8.0
2010-05-06 OPTIS SPEOS for Pro/ENGINEER ® 2010
2010-05-06 OptisWorks Studio 2010
2010-05-05 DesignBuilder.v2.2.4.001
2010-05-04 Appligent.AppendPDF.Pro.v5.1.Cracked
2010-05-04 Gurobi.Optimization.Gurobi.for.AMPL.v3.0.0.Cracked
2010-05-03 FLOWSCIENCE.FLOW-3D.V9.3.2
2010-05-03 Quint Optishape-TS 2010 R1
2010-05-03 CHAM.PHOENICS.V2009
2010-05-02 FLUIDON.DSHPLUS.V3.6.2
2010-05-02 ARUP_OASYS_V9.4.1
2010-05-01 QForm v5.10
from caxsoft
2010-05-30 Agilent.EMPro.v2010
2010-05-27 E3.series.2010.v900
2010-05-23 IAR.Embedded.Workbench.For.ARM.V5.501
2010-05-23 IAR.Embedded.Workbench.For.Msp430.V5.1
2010-05-20 Agilent 89600 Vector Signal Analyzer v12.00
2010-05-17 IAR Embedded Workbench for Atmel AVR v5.50.1
2010-05-14 Novas v2010.04
2010-05-09 Xilinx.ISE.Design.Suite.v12.1 for Linux &Win
2010-05-08 Mentor.Graphics.ModelSIM.SE.6.6a
2010-05-07 Tanner LEdit 15.0
2010-05-05 BluePrint-PCB.v2.2.1.506.with.CAM350.v10.2.1.389
2010-05-03 Mentor Graphics SystemVision v5.5
2010-05-02 CoWare SPW 2010.1 Linux
2010-04-29 Mentor.Graphics.Seamless.CVE.v5.4s
2010-05-12
Tanner-Tools- v15
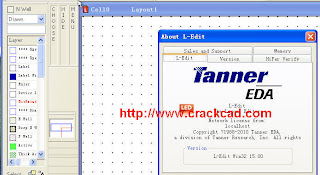
Tanner Tools Version 15.00
What's New in S-Edit v15.00
Spice and Verilog-A Text Views
S-Edit now supports Spice and Verilog-A text views. Any combination of i) schematic,
ii) Spice, and iii) Verilog-A view may be saved for a cell. The view that is used when
simulating is given by a priority list of view types and view names defined in the
Hierarchy Priority tab of the Setup Simulation dialog. A similar list is on the Export
Spice dialog for use when exporting Spice.
Spice Command Tool
The Spice Command Tool for inserting new Spice commands is now available in the
Additional Spice Commands page of the Setup Simulation dialog. The Insert
Command… button is used to invoke the wizard.
Model Parameter Listings
A table showing all the models supported in T-Spice is now available in S-Edit via the
Help > Models Supported by T-Spice… menu. A table showing the models used in
the libraries specified for the current design is available via Tools > T-Spice Library
Models, and a table showing the device parameters for all devices in the design is
available via Tools > T-Spice Device Parameters… . The Help > Models Supported
by T-Spice table shows default values for all models and devices, whereas the Tools
menu shows tables with the actual models and device values to be used in the
simulation of the current design.
Design Checks
Performance of design checks has been significantly improved. A limit of 20 errors
are reported for each design rule.
A new design check for checking overlapping wires has been added.
The default severity of "illegal connectivity" design checks, such as connecting buses
of different widths, is now Error instead of Warning.
The design check for overlapping instances now ignores symbols that do not have
any ports. This prevents the design check from flagging frame instances, which
overlap the entire schematic.
Design check now performs cell name checks in a case insensitive manner. Cell
names in different libraries with same name but different case will now issue a
warning/error.
Bug Fixes
Performance of Push and Pop context is significantly improved.
Design checks now properly identifies the case when two cells with same name are
instanced from different libraries.
Fixed problem when importing an EDIF schematic file created in S-Edit, the option
"Overwrite existing views" did not work properly.
S-Edit has a new Simulation Setup option, "Keep all simulation results". When True,
a time stamp is appended to the Simulation Results folder, so each simulation is
saved in a unique folder. When False, prior results are overwritten.
2
Fixed problem where Verilog import would have missing pins when a module
definition contains a port, but does not declare the port in the module's contents.
These ports will now be declared as type "other" and a warning will be issued.
Verilog import now imports parameters.
Ports containing buses with {} brackets now import properly.
Verilog Import dialog no longer reverts the TieHigh cell: value to TieHigh even when
something else is specified.
Fixed a problem where Property set would apply to selections that were not on the
active page.
Selecting properties on symbols will now select the property that is clicked on. Using
the left mouse button will cycle through overlapping properties, allowing one to select
difficult to select properties.
Fixed a problem where a box width could not be changed to be greater than 66
inches.
An option "Exclude simulator commands" is added to the Spice Export dialog to
suppress simulation setup commands during Spice export.
"New properties ${PageNumber} and ${Pages} have been added. ${PageNumber}
evaluates to the 1-based index of the page that contains the instance. ${Pages}
evaluates to the total number of pages in the schematic view that contains the
instance.
Zoom to selection now works correctly on highlighted nets
ORCAD EDIF files may now be imported and the netlisting commands are correctly
translated for exporting Spice.
"Author (renamed from "Creator"), Version, Modification Date ("Last Modified"), Info
and Organization and RevisionCount are now included as column choices in the
View Navigator.
Import of Cadence EDIF files now reads callbacks from the cdf file and places the
function name and parameters on the property. A tcl file with stubs for the functions is
created for the user to provide the content of the tcl function.
Problems importing EDIF written by the Gateway Schematic Editor are fixed.
Tcl scripts saved from S-Edit and placed in the user preferences startup folder wll
now properly load on program startup.
Exported netlists are now sorted within each sort order block. The sort first sorts the
alphabetic characters and then sorts any numbers in the name as a number. For
example, the sort will produce C1, C2, C10, C11, wheras a normal alphabetical sort
would be C1, C10, C11, C2.
Printing will now print all pages of a schematic view, rather than just the first.
In Setup SPICE Simulation, the Verilog search path is now saved.
When separated by a space instead of a comma, negative values in temperature
sweeps were being evaluated as an expression. The description field has been
enhanced with: "Use commas to separate negative numbers or expressions"
Annotations on schematic are now updated automatically after each simulation. It is
no longer required to turn off then back on annotations to update after a simulation.
The InstanceName property on a symbol can now be used as a prefix to use for the
instance name when creating a new instance. If InstanceName is "M" then instances
will be named M_1, M_2, etc. If InstanceName is blank, then the cell name is used.
GAMMA-TECHGT-SUITE-V7.0-download
New Features Introduced in GT-SUITE V7.0
GAMMA TECH GT SUITE v7.0
GT-POWER
GT-DRIVE
GT-VTRAIN
GT-COOL
GT-FUE
Version V7.0 is a major new release which contains many improvements as well as many added capabilities. The features listed below represent only the main developments of V7.0; in addition there are hundreds of smaller ones that do not show up in the list. Note that all of the new features of V7.0 are included in the base price of GT-SUITE (there are no extra-cost items).
1. SIMULATION ENVIRONMENT
Graphical Interface (GT-ISE)
- The popular Compound Templates have been given new powerful capabilities,
including encryption and database features
- Case Setup has been greatly enhanced, providing many new features for handling of parameters
(organizing them in folders, search, rename, etc.).
It also allows references to EXCEL and ASCII files.
- Data arrays can point to EXCEL data (as well as to ASCII)
- New wizard aids in initiating building of a new model
- Subassembly encryption now includes expiration date
Post-Processing (GT-POST)
- Completely new plotting engine, with many interactive features
(zooming, panning, display data point coordinates, drag legend box, etc.)
- Enhanced handling of plot properties and RLT plotting wizard
- Animated plots
- Interactive sectioning of 3D plots
- Wizard for data export to ASCII files (plot, CaseRLT, TimeRLT, End-of-Run)
Distributed Computing / Run Remote
- Halt a job from the user interface
- Choose solver build number to run when submitting simulation
- Run remote from command line
Optimization and DOE/Post
- Powerful new combined independent and sweep optimization
- Numerous other enhancements
2. ENGINE
Combustion and Heat Transfer
- DI Jet diesel combustion model enhanced, especially for multi-pulse injections
- SITurb SI combustion model enhanced
- Kinetics-based HCCI combustion model added
- New easy-to-use method for predictive combustion model calibration by pressure data
- Measured pressure analysis (to calculate burn rate) greatly improved
Turbocharging
- New extrapolation of compressor efficiency at low speeds
- Range of input data included on compressor contour plots
- Compressor surge dynamic model, based on radial equilibrium theory,
predicts flow beyond the surge line, all the way to negative flow
Acoustics
- New physical models
- Additional data handling features
- Enhancements in the linear acoustics solver
- Improved thermal correction and mean flow correction
- GEM3D has improved STL import, added discretization options and body fitted meshing
Mean Value Modeling and Real-Time
- RT cylinder pressure via crank-angle resolved RT combustion model
- Support for systems from ETAS, dSpace, A&D, Cybermetrix, Mathworks, Opal-RT,
and Real-Time Technologies. NI currently in development.
- Neural Network training wizard enhanced with new capabilities and data merging
Aftertreatment
- 3D and 2D modeling of catalysts and DPF
- DPF with ash filtration and asymmetric channels
- Surface reactions with competing site reactions (‘triplets’)
- Handling of multiple active and non-uniform site density
CFD Coupling and General Flow
- Support for Star-CCM coming soon
- Added support for OpenFOAM
- New PipeTable for building complex pipes (with area changes and bends) all in one
3. INJECTION AND HYDRAULICS
- New fluid-mechanical templates for hydraulic/pneumatic valves
- Transient model for dissolved and free air
- Enhanced frequency dependent friction model
- New electrical and magnetic libraries for detailed valve actuation (solenoid, piezo, etc.)
- Hydro-mechanical coupling extended to 2-D (planar) mechanical systems
- Semi-automatic building of flow networks directly from CAD data
Lubrication
- Free / dissolved gas model for aeration in oil (transient)
- Oil property preprocessor (from test data)
- Added new capabilities to bearing models
- Semi-automatic building of flow networks directly from CAD data
4. VEHICLE THERMAL MANAGEMENT (VTM) and COOLING
- Greatly increased speed of large VTM simulations
- Faster model building
- Enhanced heat exchanger calibration method
- Semi-automatic building of flow networks directly from CAD data
- Enhancements to COOL3D – extended to more general 3D geometries
Two-Phase Flows
- Transient solution based on the standard reliable GT-SUITE flow solver
- Modeling of AC systems, sub- and super-critical, of any topology
- Modeling of Rankine cycle for Waste Heat Recovery
- Hybrid battery cooling
- Seamless integration with overall thermal management in GT-SUITE
- Very fast solution -- several times faster than Real-Time
- Modular lumped analysis cabin model
- Detailed 3D cabin model built by CAD preprocessor COOL3D
5. VEHICLE, DRIVELINE and TRANSMISSION
- New clutch model with no reliance on system identification for lockup modeling
- Versatile model-based vehicle controller
- Generalized transfer case, differential and planetary gear models
- Powerful event manager (control) module
- Vehicle electrical system modeling
Hybrids and Electric Vehicles
- Electric machine models that can be connected to electrical system models
- New electrical and magnetic libraries (added to GT-SUITE at no extra cost)
- Wide range of components can be constructed by using the new library
6. MECHANICAL SYSTEMS
- New FEA (node, element) based architecture
- General 1D,2D and 3D multi-body dynamics (MBD) libraries
- Modal analysis and modal reduction for flexible bodies
- Superelement capability for coupling external FE models
- Four new implicit ODE integrators for improved speed in certain stiff problems
- General planar mechanism kinematics library
Valvetrains (release planned for later Build)
- Completely general MBD architecture with no limitations in modeling any valvetrain mechanism
(non-conventional, VVA etc.)
- Kinematic solution of any mechanical VVA system
- Modeling flexible valvetrain elements (finger, rocker etc.) ,
including reduced FE models
Cranktrains (release planned for later Build)
- Vastly improved simulation time for dynamic models of elastic crankshafts
- Visco-elastic (rubber) damper model based on Maxwell solid
- Graphical model building in CRANK3D
Gear, Chain and Belt Drives
- Helical gears
- New cable-element based detailed model of belt drive systems,
including belt-pulley friction/slipping and belt transverse belt motions
GAMMA TECH GT SUITE v7.0
GT-POWER
GT-DRIVE
GT-VTRAIN
GT-COOL
GT-FUE
Version V7.0 is a major new release which contains many improvements as well as many added capabilities. The features listed below represent only the main developments of V7.0; in addition there are hundreds of smaller ones that do not show up in the list. Note that all of the new features of V7.0 are included in the base price of GT-SUITE (there are no extra-cost items).
1. SIMULATION ENVIRONMENT
Graphical Interface (GT-ISE)
- The popular Compound Templates have been given new powerful capabilities,
including encryption and database features
- Case Setup has been greatly enhanced, providing many new features for handling of parameters
(organizing them in folders, search, rename, etc.).
It also allows references to EXCEL and ASCII files.
- Data arrays can point to EXCEL data (as well as to ASCII)
- New wizard aids in initiating building of a new model
- Subassembly encryption now includes expiration date
Post-Processing (GT-POST)
- Completely new plotting engine, with many interactive features
(zooming, panning, display data point coordinates, drag legend box, etc.)
- Enhanced handling of plot properties and RLT plotting wizard
- Animated plots
- Interactive sectioning of 3D plots
- Wizard for data export to ASCII files (plot, CaseRLT, TimeRLT, End-of-Run)
Distributed Computing / Run Remote
- Halt a job from the user interface
- Choose solver build number to run when submitting simulation
- Run remote from command line
Optimization and DOE/Post
- Powerful new combined independent and sweep optimization
- Numerous other enhancements
2. ENGINE
Combustion and Heat Transfer
- DI Jet diesel combustion model enhanced, especially for multi-pulse injections
- SITurb SI combustion model enhanced
- Kinetics-based HCCI combustion model added
- New easy-to-use method for predictive combustion model calibration by pressure data
- Measured pressure analysis (to calculate burn rate) greatly improved
Turbocharging
- New extrapolation of compressor efficiency at low speeds
- Range of input data included on compressor contour plots
- Compressor surge dynamic model, based on radial equilibrium theory,
predicts flow beyond the surge line, all the way to negative flow
Acoustics
- New physical models
- Additional data handling features
- Enhancements in the linear acoustics solver
- Improved thermal correction and mean flow correction
- GEM3D has improved STL import, added discretization options and body fitted meshing
Mean Value Modeling and Real-Time
- RT cylinder pressure via crank-angle resolved RT combustion model
- Support for systems from ETAS, dSpace, A&D, Cybermetrix, Mathworks, Opal-RT,
and Real-Time Technologies. NI currently in development.
- Neural Network training wizard enhanced with new capabilities and data merging
Aftertreatment
- 3D and 2D modeling of catalysts and DPF
- DPF with ash filtration and asymmetric channels
- Surface reactions with competing site reactions (‘triplets’)
- Handling of multiple active and non-uniform site density
CFD Coupling and General Flow
- Support for Star-CCM coming soon
- Added support for OpenFOAM
- New PipeTable for building complex pipes (with area changes and bends) all in one
3. INJECTION AND HYDRAULICS
- New fluid-mechanical templates for hydraulic/pneumatic valves
- Transient model for dissolved and free air
- Enhanced frequency dependent friction model
- New electrical and magnetic libraries for detailed valve actuation (solenoid, piezo, etc.)
- Hydro-mechanical coupling extended to 2-D (planar) mechanical systems
- Semi-automatic building of flow networks directly from CAD data
Lubrication
- Free / dissolved gas model for aeration in oil (transient)
- Oil property preprocessor (from test data)
- Added new capabilities to bearing models
- Semi-automatic building of flow networks directly from CAD data
4. VEHICLE THERMAL MANAGEMENT (VTM) and COOLING
- Greatly increased speed of large VTM simulations
- Faster model building
- Enhanced heat exchanger calibration method
- Semi-automatic building of flow networks directly from CAD data
- Enhancements to COOL3D – extended to more general 3D geometries
Two-Phase Flows
- Transient solution based on the standard reliable GT-SUITE flow solver
- Modeling of AC systems, sub- and super-critical, of any topology
- Modeling of Rankine cycle for Waste Heat Recovery
- Hybrid battery cooling
- Seamless integration with overall thermal management in GT-SUITE
- Very fast solution -- several times faster than Real-Time
- Modular lumped analysis cabin model
- Detailed 3D cabin model built by CAD preprocessor COOL3D
5. VEHICLE, DRIVELINE and TRANSMISSION
- New clutch model with no reliance on system identification for lockup modeling
- Versatile model-based vehicle controller
- Generalized transfer case, differential and planetary gear models
- Powerful event manager (control) module
- Vehicle electrical system modeling
Hybrids and Electric Vehicles
- Electric machine models that can be connected to electrical system models
- New electrical and magnetic libraries (added to GT-SUITE at no extra cost)
- Wide range of components can be constructed by using the new library
6. MECHANICAL SYSTEMS
- New FEA (node, element) based architecture
- General 1D,2D and 3D multi-body dynamics (MBD) libraries
- Modal analysis and modal reduction for flexible bodies
- Superelement capability for coupling external FE models
- Four new implicit ODE integrators for improved speed in certain stiff problems
- General planar mechanism kinematics library
Valvetrains (release planned for later Build)
- Completely general MBD architecture with no limitations in modeling any valvetrain mechanism
(non-conventional, VVA etc.)
- Kinematic solution of any mechanical VVA system
- Modeling flexible valvetrain elements (finger, rocker etc.) ,
including reduced FE models
Cranktrains (release planned for later Build)
- Vastly improved simulation time for dynamic models of elastic crankshafts
- Visco-elastic (rubber) damper model based on Maxwell solid
- Graphical model building in CRANK3D
Gear, Chain and Belt Drives
- Helical gears
- New cable-element based detailed model of belt drive systems,
including belt-pulley friction/slipping and belt transverse belt motions
2010-05-07
PlantWAVE_PDMS v3.99
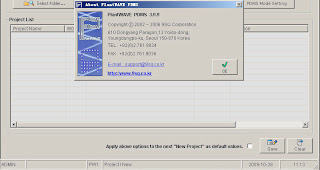
Input of PlantWAVE :
Design database :
PlantWAVE uses PDMS design database (model) as inputs. These design data are the piping design data, equipment design data, structural design data and HVAC design data. Each item of design data is defined geometrically in PDMS as a collection of basic 3D shapes known as primitives. These primitives is used for the background graphics of the drawing and used to calculate the geometric relationship for understanding the geometry.
Design Attributes :
Design attributes are the input of PlantWAVE also. These attributes that are general attributes and special attributes include the non-geometric information of design models. PlantWAVE extracts the information from the design attributes by applying them to the design models. In addition to their standard attributes, elements may have one or more Userdefined Attributes (UDAs). The UDAs can be used for the annotations by user¡¯s option in PlantWAVE option stage.
Catalogue DB :
It contains physical information about standard piping and structural components available in a PDMS project. The catalogue DB is also the input of PlantWAVE in case that PlantWAVE generates 2D hidden drawing directly without using PDMS drawings. If user wants to use the drawing that was created by PDMS, catalogue DB will not be used.
How to be extracted :
The input data are extracted from the PDMS database by the PlantWAVE pre-processor, which was written in PDMS DARs (Data Access Routine) and PML (Programmable Macro Language). The pre-processor is executed by the command of PlantWAVE¡¯s user interface with the given condition and option values.
PlantWAVE consists of the following 4 main processors :
Pre Processor :
Pre processor reads the design model and attributes that are referenced in the drawing. There is more than one view in the drawing in general. All the data are extracted and distributed to the related views. The extracted data is refined and forwarded to HSR processor.
At this point, all the coordinates are the model coordinates. They should be transformed into the drawing coordinates by considering the view direction, view scale, view rotation in the drawing.
In general, there are 5 kinds of design models to be read as follows:
¨ª Piping design model
¨ª Equipment design model
¨ª Structure design model
¨ª HVAC design model
¨ª Electric cable tray design model
ShipConstructor-V2009R1
The latest release of ShipConstructor, a 3D CAD/CAM software toolset for the shipbuilding and offshore industries, is specifically targeted for use on large-scale projects. ShipConstructor 2009 is compatible with AutoCAD 2009 and includes numerous enhancements designed to increase efficiency when working with complex 3D product models as well as features aimed at reducing production costs.
64-bit Support
ShipConstructor 2009 will allow 64-bit capability on the Microsoft Windows Vista and Windows 7 platforms. This added capability will allow modelers to load larger portions of the 3D model into a single working session at a greater level of detail with increased program stability.
Democratizing Virtual Reality
Another enhancement is significant improvements involving the creation of 3D Virtual Reality (VR) models. With only a few mouse clicks, any designer can now more easily create a detailed VR model from the product model. Numerous visualization options are also available.
Nest-lg
ShipConstructor Nest Optimizer improves Material utilization up to 6%. Image courtesy of EAS.
Improved Material Utilization
ShipConstructor has improved its automated nesting capabilities with the introduction of an enhanced nest optimization engine. Test results have shown clients can expect up to a 6% improvement in overall plate utilization.
Intelligent Distributed System Supports
ShipConstructor 2009 includes a new intelligent Distributed Systems Supports module which is a rule-based program for the creation of distributed system supports such as pipe and HVAC. In line with the company’s other efforts to enhance Design for Production (DFP), the software allows an experienced designer to inject knowledge-based rules into the library of supports which are available during the 3D modeling process.
This enhanced module offers parametric design based on a broad range of industry standard supports. Each support is associated with a set of pipes and pipe hangers as well as foundational structure, allowing the support to be constrained and automatically adapt to design changes as the project progresses. This provides a smooth transition from engineering to production.
Multi2-Concept-lg
Example of complex piping model with Standard Assemblies. Image courtesy of EAS.
Effective Design Reuse
Another DFP-based enhancement allows for the standardization of commonly used assemblies, including items such as simple panels, ladders, pipe manifolds, handrails and equipment complete with standard foundations.
In addition to allowing common items to be modeled once and used many times, these Standard Assemblies include the production documentation required for fabrication. The production documents include 3D assembly drawings for each stage in fabrication. When changes are made to the Standard Assembly definition or the related construction documents, all instances where it has been used are automatically changed as well. This reduces the time needed in the design process, especially on large-scale projects.
Space Allocations
This latest version of ShipConstructor provides an intuitive set of tools that allows modelers to allocate space for the various systems (pipe, HVAC, electrical etc.) well before they are modeled. The allocated space is parametrically associated with the wireways in the upcoming ShipConstructor Electrical module. Changes to the allocated space will be automatically propagated to the detailed electrical system model, providing a bridge between the earlier stages of the design process and the final production design.
ShipConstructor 2009 R1 is now available as a full install only. Please contact your dealer for the full install download link. If you run the full install while ShipConstructor 2008 is installed, it will act as an upgrade and will automatically upgrade ShipConstructor 2008.
?What's New: ShipConstructor 2009 R1 introduces many new features and improvements. Please read the What's New document for more details.
?Project Split & Merge Customers Please Read: Project Split & Merge is still undergoing changes to support the new features in ShipConstructor 2009. Therefore users who are using Project Split & Merge should not update to ShipConstructor 2009 until version R1.1 where this feature will be supported.
?Database Update Note: Updating a database from ShipConstructor 2008 to ShipConstructor 2009 uses the same process as updating one version of SC2008 to another, however in this case it may take several hours
64-bit Support
ShipConstructor 2009 will allow 64-bit capability on the Microsoft Windows Vista and Windows 7 platforms. This added capability will allow modelers to load larger portions of the 3D model into a single working session at a greater level of detail with increased program stability.
Democratizing Virtual Reality
Another enhancement is significant improvements involving the creation of 3D Virtual Reality (VR) models. With only a few mouse clicks, any designer can now more easily create a detailed VR model from the product model. Numerous visualization options are also available.
Nest-lg
ShipConstructor Nest Optimizer improves Material utilization up to 6%. Image courtesy of EAS.
Improved Material Utilization
ShipConstructor has improved its automated nesting capabilities with the introduction of an enhanced nest optimization engine. Test results have shown clients can expect up to a 6% improvement in overall plate utilization.
Intelligent Distributed System Supports
ShipConstructor 2009 includes a new intelligent Distributed Systems Supports module which is a rule-based program for the creation of distributed system supports such as pipe and HVAC. In line with the company’s other efforts to enhance Design for Production (DFP), the software allows an experienced designer to inject knowledge-based rules into the library of supports which are available during the 3D modeling process.
This enhanced module offers parametric design based on a broad range of industry standard supports. Each support is associated with a set of pipes and pipe hangers as well as foundational structure, allowing the support to be constrained and automatically adapt to design changes as the project progresses. This provides a smooth transition from engineering to production.
Multi2-Concept-lg
Example of complex piping model with Standard Assemblies. Image courtesy of EAS.
Effective Design Reuse
Another DFP-based enhancement allows for the standardization of commonly used assemblies, including items such as simple panels, ladders, pipe manifolds, handrails and equipment complete with standard foundations.
In addition to allowing common items to be modeled once and used many times, these Standard Assemblies include the production documentation required for fabrication. The production documents include 3D assembly drawings for each stage in fabrication. When changes are made to the Standard Assembly definition or the related construction documents, all instances where it has been used are automatically changed as well. This reduces the time needed in the design process, especially on large-scale projects.
Space Allocations
This latest version of ShipConstructor provides an intuitive set of tools that allows modelers to allocate space for the various systems (pipe, HVAC, electrical etc.) well before they are modeled. The allocated space is parametrically associated with the wireways in the upcoming ShipConstructor Electrical module. Changes to the allocated space will be automatically propagated to the detailed electrical system model, providing a bridge between the earlier stages of the design process and the final production design.
ShipConstructor 2009 R1 is now available as a full install only. Please contact your dealer for the full install download link. If you run the full install while ShipConstructor 2008 is installed, it will act as an upgrade and will automatically upgrade ShipConstructor 2008.
?What's New: ShipConstructor 2009 R1 introduces many new features and improvements. Please read the What's New document for more details.
?Project Split & Merge Customers Please Read: Project Split & Merge is still undergoing changes to support the new features in ShipConstructor 2009. Therefore users who are using Project Split & Merge should not update to ShipConstructor 2009 until version R1.1 where this feature will be supported.
?Database Update Note: Updating a database from ShipConstructor 2008 to ShipConstructor 2009 uses the same process as updating one version of SC2008 to another, however in this case it may take several hours
NovaFlow-Solid-CV-V4.3
NovaFlow & Solid CV is a new complete simulation package. Using new advanced numeric models and a new meshing technology, Control Volume, it is the most efficient simulation package on the market.
NovaFlow & Solid CV requires less than one hour to set up a complete simulation including start-up, meshing and running. The resulting simulation will be extremely accurate in accordance with your 3D drawings.
NovaFlow & Solid CV
is a complete mould filling and solidification simulation package based on advanced fluid flow and heat transfer theories.
NovaFlow & Solid CV utilizes Control Volume Meshing technology (CVM). With this technology, the surface of the 3D model controls the shape of the mesh elements on the border of the casting. This creates cubic elements inside the casting and border cells on the boundary of the casting.
Advantages of using the CVM technology
The CVM technology has the following advantages in comparison with the FDM / FEM method:
* For most castings, simulation time is reduced to around 10% with the same or better accuracy. (FDM)
* Higher accuracy in simulation thanks to perfect description of the 3D model. All sections are correct in size. (FDM)
* CVM needs less cells to define the casting geometry and ensures faster simulations and smaller result files. (FDM)
* The meshing process is completely automatic and takes only seconds. (FEM)
* The method enables more advanced calculation such as gas flow, contact task (stress) or full mould process. (FDM)
NovaFlow & Solid CV requires less than one hour to set up a complete simulation including start-up, meshing and running. The resulting simulation will be extremely accurate in accordance with your 3D drawings.
NovaFlow & Solid CV
is a complete mould filling and solidification simulation package based on advanced fluid flow and heat transfer theories.
NovaFlow & Solid CV utilizes Control Volume Meshing technology (CVM). With this technology, the surface of the 3D model controls the shape of the mesh elements on the border of the casting. This creates cubic elements inside the casting and border cells on the boundary of the casting.
Advantages of using the CVM technology
The CVM technology has the following advantages in comparison with the FDM / FEM method:
* For most castings, simulation time is reduced to around 10% with the same or better accuracy. (FDM)
* Higher accuracy in simulation thanks to perfect description of the 3D model. All sections are correct in size. (FDM)
* CVM needs less cells to define the casting geometry and ensures faster simulations and smaller result files. (FDM)
* The meshing process is completely automatic and takes only seconds. (FEM)
* The method enables more advanced calculation such as gas flow, contact task (stress) or full mould process. (FDM)
2010-05-05
OPTIS-SPEOS-CAA-V5-Based-V8.0-key-crack
* Discover new functionalities, enhancements, fixes in the What's New section of the "User guide"
* All details for installation are available in the “Installation guide”
* For download from the Customer Portal, FDM http://www.freedownloadmanager.org is recommended
* Don't forget to ask for your new OPTIS Labs 2010 License using the "license@optis-world.com" email!
* This setup includes OPTIS Labs 2010
* This setup includes OPTIS License Manager 2010
Table Of Contents
Getting Started............................................................................................................................ 1
Getting Started Visual Ergonomics........................................................................................ 1
Getting Started Visual Ergonomics.................................................................................... 1
Step 1: Preparing data ........................................................................................................ 2
Step 2: Launching SPEOS CAA V5 Based ....................................................................... 3
Step 3: Entering the "Visual Ergonomics"
. Copy SV5_GS_Data_VE_R17V7.zip in a local directory and extract it.
From the Start menu, select "All Programs\OPTIS\SPEOS CAA V5 Based V5.0\SPEOS CAA
V5 Based VX R17".
1. Select the "Start\Analysis & Simulation\Visual Ergonomics" command.
The workbench is opened. The commands for "Visual Ergonomics" are available in the
toolbar to the top and the right of the application window.
1. Right-click the product in the specification tree then select the "Components\Existing
Component..." contextual menu. The "Insert an Existing Component" dialog box is
displayed.
2. Select the "Support.CATPart" document.
3. Click Open
The support is loaded in the "Visual Ergonomics" workbench.
Getting Started
4. Right-click the Product1 and rename it as "GS_VE" in the "Properties" window. In the
"File/Save as" window, rename the CATProduct as "GS_VE.CATProduct" in the
SV5_GS_Data_VE_R17V6 directory.
2010-04-CRACK-0DAY-SOFTWARE-DWONLOAD
2010-04-30 CSC Fastrak 19.0
2010-04-29 Comsol Multiphysics v4.0
2010-04-29 SOLIDWORKS 2010 UPDATE SP3.0
2010-04-28 Autodesk.Softimage.v2011
2010-04-28 SolidCAM 2010 SP0.0 English for Solidworks 2007-2010
2010-04-27 Adobe.Creative.Suite.5.Master.Collection
2010-04-27 Camnetics.GearTeq.v2010.18.32.318
2010-04-26 Mastercam X5 v14.0.10.21 for SolidWorks v2008-2010
2010-04-25 Trumpf ToPs100 v5.02
2010-04-24 Tripos Sybyl-X 1.1
2010-04-23 ProgmanOy.MagiCAD.2009.11.SR
2010-04-23 ADA.EASE.V4.3.8.69
2010-04-22 ETАP Pоwer Stаtiоn 7.1
2010-04-21 FloEFD.pro v9.1
2010-04-20 AUTODESK.AUTOCAD.REVIT.MEP.SUITE.V2011
2010-04-20 Gurobi.Optimization.Gurobi.v3.0.0.Cracked
2010-04-20 Gurobi.Optimization.Gurobi.for.AMPL.v2.0.3.Cracked
2010-04-19 AUTODESK.ROBOT.STRUCTURAL.ANALYSIS.V2011.MULTI
2010-04-18 Tecplot.RS.2010.R1.v2010.1.1.7629.x64
2010-04-17 AUTODESK.AUTOCAD.ECSCAD.V2011.WIN32
2010-04-16 Sema-EXPERIENCE-v11
2010-04-15 AUTODESK.MOTIONBUILDER.V2011
2010-04-14 Dassault.Systemes.3DVIA.Composer.V6R2010x.HF2.v6.5.2.1438
2010-04-14 Iceni.Technology.Infix.Server.v2.01.Cracked
2010-04-13 ETA Dynaform 5.7.3
2010-04-13 MVTec HALCON 9.0.2
2010-04-13 CAM-TOOL v5.0
2010-04-13 HSMWorks 2010 R1.19655 Win32
2010-04-13 MISSLER.TOPSOLID.2010
2010-04-12 AUTODESK.AUTOCAD.CIVIL3D_v2011
2010-04-12 SCAD Office v11.3
2010-04-11 CAMWorks 2010 FOR SLIDWORKS
2010-04-11 AUTODESK.REVIT.ARCHITECTURE.V2011
2010-04-11 CSI SAP2000 14.2
2010-04-10 AUTODESK.REVIT.STRUCTURE.V2011
2010-04-09 AUTODESK_MUDBOX_V2011
2010-04-09 AUTODESK.ALIAS.DESIGN.V2011
2010-04-08 AUTODESK.ALIAS.AUTOMOTIVE.V2011
2010-04-08 Xceed.Ultimate.Suite.2009.v5.Build.3.2.10175.Incl.Keygen
2010-04-08 Heavyweight.Transport.Simulator
2010-04-07 Geometric.Technologies.CAMWorks.2009.SP3.0
2010-04-07 AUTODESK.MAYA.V2011
2010-04-06 Autodesk 3DS MAX Design v2011
2010-04-06 Autodesk 3DS MAX v2011
2010-04-05 CEI.EnSight.Gold.v9.1.1b
2010-04-04 OPTICAL.RESEARCH.ASSOCIATES.LIGHTTOOLS.V7.0
2010-04-03 Golden.Software.Surfer.v9.9.785
2010-04-03 CopperCAM v2010.01.26
2010-04-03 Autodesk.Alias.Surface.v2011
2010-04-02 Retain Pro 9
2010-04-02 LISCAD v9.0.1
2010-04-01 CADKON.2010.German
2010-04-01 AUTODESK.SHOWCASE.V2011
2010-04-01 AUTODESK.ALIAS.SURFACE.V2011
FORM caxsoft
2010-04-29 Mentor.Graphics.Seamless.CVE.v5.4s
2010-04-27 Cadence SPB v16.30.007 Update
2010-04-23 ANSOFT.TPA.V5.1
2010-04-23 ANSOFT MAXWELL V12.2.1
2010-04-22 Agilent.GeneSpring.GX.v11.0
2010-04-21 Mentor.Graphics.Precision.RTL.Synthesis.v2010a.218.Win32
2010-04-18 Mentor Graphics IC Flow2008.2a
2010-04-16 Sigrety SpeedXP Suite x86 v91.2.5
2010-04-13 CoventorWare 2010
2010-04-11 Agilent_SystemVue 2010
2010-04-10 Ansoft. Designer. V5.0
2010-04-09 Laker 2009.12 P2
2010-04-08 Atrenta SpyGlass v4.2.0
2010-04-08 Infolytica Magnet v7.0
2010-04-07 Altera.Quartus.II.v9.1.SP2.Windows.Update.Only &for Linux
2010-04-07 Synopsys Synthesis Tools tool vD-2010.03
2010-04-06 Synopsys Formality 2010.03
2010-04-05 Synopsys Design Compiler 2010.03
2010-04-04 Synopsys Synplify FPGA 2010.03 Win
2010-04-03 CST.STUDIO.SUITE.V2010
FROM CAXCRACK
CGMstudio 8.3.5
Techlog Interactive Suite 2010
SMT Kingdom v8.5 Win32
Datamine Studio v3.19.3025
Earthworks.NPV.Scheduler.v4.2
GeoGraphix DSS R5000.0.0.3
SIMSCI PRO II v8.3
Encom PA 10.0.17
Flaresim v2.0
GEMCOM.MINEX.V6.0.2
Petrosys v16.6.2
Petrel 2009.2 FOR Win32&Win64
Encom Discover3D v5.0.63
Encom Discover v11.1
Portable Golden Software Grapher 8.2.460
Accelrys.Discovery.Studio.v2.5.Linux&Win
Landmark Drillworks 12.5
CMG Suite 2009.06.20
Global.Mapper.v11.2
Vantage.Plant.Design.Management.System.v12 Wth sp4
VMGSIM.V5.0.5
Datamine Studio v3.18.2656.0
PipelineStudio v3.2.0.6
LimitState.GEO.v2.0.c.10779
Applied.Flow.Technology.Fathom.v7.0.2009.11.02.Cracked
Fugro Jason 8
Hampson.Russell.CE8.R4.4
Z-soil 2D V6.13
Intergraph SmartPlant Review v6.0
ChemStations.ChemCAD.v6.2.0.3348.Cracked
FlareSIM V2.0
Permedia Mpath v4.16
SCHLUMBERGER.ECLIPSE.V2009.1
SCHLUMBERGER.Pipesim.V2009.1
Schlumberger.DBR.SOLIDS.V4.2
Erdas image 9.2
Landmark.Dynamic.Surveillance. System (DSS) R5000
GMG-MESA.v11.01
Geographix R2007.2
Asphalt.Test.Report.System.v4.0.0046
FRI.Device.Rating.Program.V1.4.0
Gedco.Vista.Seismic.Processing.V9.00
IPM.Petroleum.Expert.v7.5
Paradigm.Sysdrill.v2009
Intergraph SmartPlant Enterprise 2007
COADE TANK V3.5
CambridgeSoft.ChemOffice.2010.v12
Wavefunction.Spartan.08.v1.2
Wavefunction.Odyssey.College.Chemistry.v3.1.Cracked
Process.Systems.Enterprise.gPROMS.v3.15.
Midland.Valley.Move.V2009.1
PetrisWinds Recall 5.2 system
GEMCOM.Minex.V6.1
Temis Suite 2008
Seismic Processing Workshop v2.2.10
Paradigm Interpret 2009
PvtSim V18 (c)CALSEP
HEXTRAN v9.1
Kingdom Suite SMT 8.3
Omni 3D Design v8.0
HAZOP phapro6
Micromine v11
CGM Studio 9.5 Larson Software Technology
Tempest 6.5
PipeDataPro v8
Roxar_IRAP_RMS_2009.03
Paradigm.Geolog.V6.7.1
Geoframe 4.4
Golden Software Surfer v9.8.669 Update
DNV Phast and Safeti v6.51
Kappa Emeraude 2.42.10
SubPump V9.1
IHS.QUESTOR.v9.4
VMG Sim V4
Plant-4D v7.703
Vista V8.0 2D/3D Seismic Processing
Interactive petrophysics 3.5 (c)Schlumberger
PetrisWinds Recall 5.2 system
Pipe flow expert 2008
Schlumberger.FracCADE.V5.10
Schlumberger TDAS 6.1.6
Schlumberger.Drilling.Office.V4.0
COADE CADWorx 2010
COADE.CAESAR.II.v5.2
IHS_DEEPE$T_3.7
AspenONE Suite v7.1
2010-04-29 Comsol Multiphysics v4.0
2010-04-29 SOLIDWORKS 2010 UPDATE SP3.0
2010-04-28 Autodesk.Softimage.v2011
2010-04-28 SolidCAM 2010 SP0.0 English for Solidworks 2007-2010
2010-04-27 Adobe.Creative.Suite.5.Master.Collection
2010-04-27 Camnetics.GearTeq.v2010.18.32.318
2010-04-26 Mastercam X5 v14.0.10.21 for SolidWorks v2008-2010
2010-04-25 Trumpf ToPs100 v5.02
2010-04-24 Tripos Sybyl-X 1.1
2010-04-23 ProgmanOy.MagiCAD.2009.11.SR
2010-04-23 ADA.EASE.V4.3.8.69
2010-04-22 ETАP Pоwer Stаtiоn 7.1
2010-04-21 FloEFD.pro v9.1
2010-04-20 AUTODESK.AUTOCAD.REVIT.MEP.SUITE.V2011
2010-04-20 Gurobi.Optimization.Gurobi.v3.0.0.Cracked
2010-04-20 Gurobi.Optimization.Gurobi.for.AMPL.v2.0.3.Cracked
2010-04-19 AUTODESK.ROBOT.STRUCTURAL.ANALYSIS.V2011.MULTI
2010-04-18 Tecplot.RS.2010.R1.v2010.1.1.7629.x64
2010-04-17 AUTODESK.AUTOCAD.ECSCAD.V2011.WIN32
2010-04-16 Sema-EXPERIENCE-v11
2010-04-15 AUTODESK.MOTIONBUILDER.V2011
2010-04-14 Dassault.Systemes.3DVIA.Composer.V6R2010x.HF2.v6.5.2.1438
2010-04-14 Iceni.Technology.Infix.Server.v2.01.Cracked
2010-04-13 ETA Dynaform 5.7.3
2010-04-13 MVTec HALCON 9.0.2
2010-04-13 CAM-TOOL v5.0
2010-04-13 HSMWorks 2010 R1.19655 Win32
2010-04-13 MISSLER.TOPSOLID.2010
2010-04-12 AUTODESK.AUTOCAD.CIVIL3D_v2011
2010-04-12 SCAD Office v11.3
2010-04-11 CAMWorks 2010 FOR SLIDWORKS
2010-04-11 AUTODESK.REVIT.ARCHITECTURE.V2011
2010-04-11 CSI SAP2000 14.2
2010-04-10 AUTODESK.REVIT.STRUCTURE.V2011
2010-04-09 AUTODESK_MUDBOX_V2011
2010-04-09 AUTODESK.ALIAS.DESIGN.V2011
2010-04-08 AUTODESK.ALIAS.AUTOMOTIVE.V2011
2010-04-08 Xceed.Ultimate.Suite.2009.v5.Build.3.2.10175.Incl.Keygen
2010-04-08 Heavyweight.Transport.Simulator
2010-04-07 Geometric.Technologies.CAMWorks.2009.SP3.0
2010-04-07 AUTODESK.MAYA.V2011
2010-04-06 Autodesk 3DS MAX Design v2011
2010-04-06 Autodesk 3DS MAX v2011
2010-04-05 CEI.EnSight.Gold.v9.1.1b
2010-04-04 OPTICAL.RESEARCH.ASSOCIATES.LIGHTTOOLS.V7.0
2010-04-03 Golden.Software.Surfer.v9.9.785
2010-04-03 CopperCAM v2010.01.26
2010-04-03 Autodesk.Alias.Surface.v2011
2010-04-02 Retain Pro 9
2010-04-02 LISCAD v9.0.1
2010-04-01 CADKON.2010.German
2010-04-01 AUTODESK.SHOWCASE.V2011
2010-04-01 AUTODESK.ALIAS.SURFACE.V2011
FORM caxsoft
2010-04-29 Mentor.Graphics.Seamless.CVE.v5.4s
2010-04-27 Cadence SPB v16.30.007 Update
2010-04-23 ANSOFT.TPA.V5.1
2010-04-23 ANSOFT MAXWELL V12.2.1
2010-04-22 Agilent.GeneSpring.GX.v11.0
2010-04-21 Mentor.Graphics.Precision.RTL.Synthesis.v2010a.218.Win32
2010-04-18 Mentor Graphics IC Flow2008.2a
2010-04-16 Sigrety SpeedXP Suite x86 v91.2.5
2010-04-13 CoventorWare 2010
2010-04-11 Agilent_SystemVue 2010
2010-04-10 Ansoft. Designer. V5.0
2010-04-09 Laker 2009.12 P2
2010-04-08 Atrenta SpyGlass v4.2.0
2010-04-08 Infolytica Magnet v7.0
2010-04-07 Altera.Quartus.II.v9.1.SP2.Windows.Update.Only &for Linux
2010-04-07 Synopsys Synthesis Tools tool vD-2010.03
2010-04-06 Synopsys Formality 2010.03
2010-04-05 Synopsys Design Compiler 2010.03
2010-04-04 Synopsys Synplify FPGA 2010.03 Win
2010-04-03 CST.STUDIO.SUITE.V2010
FROM CAXCRACK
CGMstudio 8.3.5
Techlog Interactive Suite 2010
SMT Kingdom v8.5 Win32
Datamine Studio v3.19.3025
Earthworks.NPV.Scheduler.v4.2
GeoGraphix DSS R5000.0.0.3
SIMSCI PRO II v8.3
Encom PA 10.0.17
Flaresim v2.0
GEMCOM.MINEX.V6.0.2
Petrosys v16.6.2
Petrel 2009.2 FOR Win32&Win64
Encom Discover3D v5.0.63
Encom Discover v11.1
Portable Golden Software Grapher 8.2.460
Accelrys.Discovery.Studio.v2.5.Linux&Win
Landmark Drillworks 12.5
CMG Suite 2009.06.20
Global.Mapper.v11.2
Vantage.Plant.Design.Management.System.v12 Wth sp4
VMGSIM.V5.0.5
Datamine Studio v3.18.2656.0
PipelineStudio v3.2.0.6
LimitState.GEO.v2.0.c.10779
Applied.Flow.Technology.Fathom.v7.0.2009.11.02.Cracked
Fugro Jason 8
Hampson.Russell.CE8.R4.4
Z-soil 2D V6.13
Intergraph SmartPlant Review v6.0
ChemStations.ChemCAD.v6.2.0.3348.Cracked
FlareSIM V2.0
Permedia Mpath v4.16
SCHLUMBERGER.ECLIPSE.V2009.1
SCHLUMBERGER.Pipesim.V2009.1
Schlumberger.DBR.SOLIDS.V4.2
Erdas image 9.2
Landmark.Dynamic.Surveillance. System (DSS) R5000
GMG-MESA.v11.01
Geographix R2007.2
Asphalt.Test.Report.System.v4.0.0046
FRI.Device.Rating.Program.V1.4.0
Gedco.Vista.Seismic.Processing.V9.00
IPM.Petroleum.Expert.v7.5
Paradigm.Sysdrill.v2009
Intergraph SmartPlant Enterprise 2007
COADE TANK V3.5
CambridgeSoft.ChemOffice.2010.v12
Wavefunction.Spartan.08.v1.2
Wavefunction.Odyssey.College.Chemistry.v3.1.Cracked
Process.Systems.Enterprise.gPROMS.v3.15.
Midland.Valley.Move.V2009.1
PetrisWinds Recall 5.2 system
GEMCOM.Minex.V6.1
Temis Suite 2008
Seismic Processing Workshop v2.2.10
Paradigm Interpret 2009
PvtSim V18 (c)CALSEP
HEXTRAN v9.1
Kingdom Suite SMT 8.3
Omni 3D Design v8.0
HAZOP phapro6
Micromine v11
CGM Studio 9.5 Larson Software Technology
Tempest 6.5
PipeDataPro v8
Roxar_IRAP_RMS_2009.03
Paradigm.Geolog.V6.7.1
Geoframe 4.4
Golden Software Surfer v9.8.669 Update
DNV Phast and Safeti v6.51
Kappa Emeraude 2.42.10
SubPump V9.1
IHS.QUESTOR.v9.4
VMG Sim V4
Plant-4D v7.703
Vista V8.0 2D/3D Seismic Processing
Interactive petrophysics 3.5 (c)Schlumberger
PetrisWinds Recall 5.2 system
Pipe flow expert 2008
Schlumberger.FracCADE.V5.10
Schlumberger TDAS 6.1.6
Schlumberger.Drilling.Office.V4.0
COADE CADWorx 2010
COADE.CAESAR.II.v5.2
IHS_DEEPE$T_3.7
AspenONE Suite v7.1
CMG-2009.10
SIMULATOR CHANGES
Geomechanics Coupling
One- and two-way (explicit as well as iterative) coupling with CMG’s
Geomechanics module has been implemented into GEM and is being
released as a Beta feature.
The geomechanics module handles different constitutive models like,
linear and non-linear elastic, generalized plasticity, elasto-plastic, single
surface, and creep models. For the elasto-plastic model the yield criteria
can be specified via Mohr-Columb or Drucker-Prager that are suitable
for the description of geologic material. There is also an isotropic strain
hardening and softening option. The behavior of cyclic loading and
unloading that occurs during cyclical injection and production can be
modeled. A cap model is also available for yield criteria of elasto-plastic
material. For Non-linear elasticity, hypoelastic and hyperelastic
constitutive models are available. Associated or non-associated flow
rules can be used for Mohr-Columb, Drucker-Prager, single surface, or
generalized plasticity models.
The above constitutive models can be used in 2D or 3D problems in the
Cartesian, corner-point, or axissymmetric grid. Finite element method is
used in the geomechanics module to compute the geomechanical
responses. The user can specify a variety of boundary conditions in 2D
and 3D on nodal points of the finite element.
The geomechanics module solves for the force equilibrium of the
formation and calculates volumetric dilation/compression as a result of
both elastic and plastic straining.
The coupling options allow porosity to be optionally dependent on
deformation. It can be a function of pressure temperature or volumetric
strain; or a function of pressure temperature and total mean stress.
The change in matrix and fracture permeability due to geomechanical
effects can be computed by a number of algorithms including the ones by
Li and Chalaturnyk; and Barton-Bandis.
A large number of possible geomechanics responses are available for
viewing in CMG’s graphical post processor “Results”, and also available
- 6 -
to the text “.out” and “.geo” files. The user can view grids in “Results”
that deform with time, but there are some restrictions for displaying 2D
radial grids.
A new data section GEOMECHANICS has been added which precedes
WELLS AND RECURRENT DATA section in the GEM input data file
to facilitate entry of geomechanics related keywords. Please see the
chapter on geomechanical features for specific keywords.
The coupled geomechanic modeling may be useful for a variety of
situations, like determination of leakage through points of weakness in
the cap rock during GHG sequestration, effect of rock deformation and
porosity change during CBM/ECBM simulation, solid deposition in
asphaltene modeling, and mineral dissolution and precipitation during
geochemical processes, and others.
Improved Parallel Performance
A new method has been implemented for parallel equation and residual
building using a method of domain decomposition based on Parasol
classes. This method is expected to give better scalability on computers
with larger number of processors.
The method is activated by using *JACPAR *ON in the Numerical
Methods section, or by specifying –jacpar on the command line. In order
to use *JACPAR, the parallel computing licensing feature must be
active.
Oil-Wet Rock-Fluid Model
The oil-wet rock fluid model modifies both the initialization and flow
calculations in GEM. See the OILWET subkeyword of the RPT keyword
for details.
The oil wet option initialization assumes that the reservoir was initially
water wet and has undergone a wettability alteration to become an oil
wet reservoir. This assumption has a significant impact on how fluids are
placed during reservoir initialization.
In the oil wet model, three phase flow is calculated assuming water is the
intermediate phase. Therefore Kro is a function of oil saturation, Krg is a
function of gas saturation, while Krw is a function of both oil and gas
saturation (through Krwo and Krwg). The normal three phase flow
models (e.g. Stone 1, Stone 2, segregated, etc) are used to determine
water relative permeability, not oil permeability.
Geomechanics Coupling
One- and two-way (explicit as well as iterative) coupling with CMG’s
Geomechanics module has been implemented into GEM and is being
released as a Beta feature.
The geomechanics module handles different constitutive models like,
linear and non-linear elastic, generalized plasticity, elasto-plastic, single
surface, and creep models. For the elasto-plastic model the yield criteria
can be specified via Mohr-Columb or Drucker-Prager that are suitable
for the description of geologic material. There is also an isotropic strain
hardening and softening option. The behavior of cyclic loading and
unloading that occurs during cyclical injection and production can be
modeled. A cap model is also available for yield criteria of elasto-plastic
material. For Non-linear elasticity, hypoelastic and hyperelastic
constitutive models are available. Associated or non-associated flow
rules can be used for Mohr-Columb, Drucker-Prager, single surface, or
generalized plasticity models.
The above constitutive models can be used in 2D or 3D problems in the
Cartesian, corner-point, or axissymmetric grid. Finite element method is
used in the geomechanics module to compute the geomechanical
responses. The user can specify a variety of boundary conditions in 2D
and 3D on nodal points of the finite element.
The geomechanics module solves for the force equilibrium of the
formation and calculates volumetric dilation/compression as a result of
both elastic and plastic straining.
The coupling options allow porosity to be optionally dependent on
deformation. It can be a function of pressure temperature or volumetric
strain; or a function of pressure temperature and total mean stress.
The change in matrix and fracture permeability due to geomechanical
effects can be computed by a number of algorithms including the ones by
Li and Chalaturnyk; and Barton-Bandis.
A large number of possible geomechanics responses are available for
viewing in CMG’s graphical post processor “Results”, and also available
- 6 -
to the text “.out” and “.geo” files. The user can view grids in “Results”
that deform with time, but there are some restrictions for displaying 2D
radial grids.
A new data section GEOMECHANICS has been added which precedes
WELLS AND RECURRENT DATA section in the GEM input data file
to facilitate entry of geomechanics related keywords. Please see the
chapter on geomechanical features for specific keywords.
The coupled geomechanic modeling may be useful for a variety of
situations, like determination of leakage through points of weakness in
the cap rock during GHG sequestration, effect of rock deformation and
porosity change during CBM/ECBM simulation, solid deposition in
asphaltene modeling, and mineral dissolution and precipitation during
geochemical processes, and others.
Improved Parallel Performance
A new method has been implemented for parallel equation and residual
building using a method of domain decomposition based on Parasol
classes. This method is expected to give better scalability on computers
with larger number of processors.
The method is activated by using *JACPAR *ON in the Numerical
Methods section, or by specifying –jacpar on the command line. In order
to use *JACPAR, the parallel computing licensing feature must be
active.
Oil-Wet Rock-Fluid Model
The oil-wet rock fluid model modifies both the initialization and flow
calculations in GEM. See the OILWET subkeyword of the RPT keyword
for details.
The oil wet option initialization assumes that the reservoir was initially
water wet and has undergone a wettability alteration to become an oil
wet reservoir. This assumption has a significant impact on how fluids are
placed during reservoir initialization.
In the oil wet model, three phase flow is calculated assuming water is the
intermediate phase. Therefore Kro is a function of oil saturation, Krg is a
function of gas saturation, while Krw is a function of both oil and gas
saturation (through Krwo and Krwg). The normal three phase flow
models (e.g. Stone 1, Stone 2, segregated, etc) are used to determine
water relative permeability, not oil permeability.
2010-04-23
Mechanical-Simulation-CarSim-V8.02
Mechanical Simulation is committed to making vehicle simulation available to users who need to "get the job done" without spending weeks of training to learn to use difficult software. We have designed the software for ease of use for the actual engineers who are doing the job, eliminating the need for expensive consultants. BikeSim, CarSim, and TruckSim are known for being much easier to learn and use than vehicle simulation has ever been, even though the math models have all the detail needed to simulate tests over the full nonlinear range of conditions that can be covered with rigid-body multibody system models.
User Interface and Database
Your main connection to the software is through the a VehicleSim (VS) browser. Click a single button to make a simulated run, then click another button to see an animation or view engineering plots of results. While using the Quick Start Guide for your software package (CarSim, BikeSim, etc.), you will be making new runs and seeing their results in less than an hour.
All properties that you set or adjust are represented in the graphical interface. Over 150 graphic screens are organized for you to access properties of the vehicle, control inputs, road geometry, plot settings, and animation settings. The VS browser GUI minimizes the time needed to build a vehicle description and set up run conditions. The database comes with an extensive array of examples and allows you to set up libraries of components, vehicles, tests, etc. This allows you to rapidly go back and forth between different runs to compare results and make changes. You can easily overlay plots and animations to quickly identify the results of your changes.
The vehicle and its properties are defined by parameters and tables that are measurable and available from a variety of sources including tests or suspension design software. The VS browser sets the standard for minimizing the time needed to assemble a complete vehicle description with detailed math models.
Tables for Nonlinear Relationships
Many of the vehicle properties, controls, and road properties are described with nonlinear tables. Starting in 2007, you can select one of many possible calculation methods, depending on your needs. These range from a constant, to a linear coefficient, to linear interpolation, to a spline, to 2D carpet plots. (There are currently 11 calculation options.)
Tables can be generated and/or transformed with a built-in calculator, or sent to Excel with a button click for more advanced work.
Outputs
The math models generate simulated time histories of hundreds of output variables. They provide the motion information for animations, and can be inspected graphically using the built-in plotter. The outputs are also converted automatically for post-processing analysis in Excel, MATLAB, and other software, for the same treatment you might apply to real test data.
Output plots and animations can be easily inserted into reports and PowerPoint presentations.
Help and Documentation
The documentation for VehicleSim products is provided in PDF files that can be accessed on line, or printed to provide old-fashined hard-copies. The documentation is covered by about 50 documents that cover broad topics such as the operation of a VehicleSim math model solver program, to detailed technical descriptions of model features such as tires, steering systems, controllers, etc.
Information is available from several methods at all times.
* Right-click on most screen controls and fields for pop-up help.
* Type F1 or click the help button to bring up the document best matched to the current screen, with details of every control and parameter on the current screen.
* Use the Help menu to access reference material for every screen in the browser program, reference manuals for major components in the VehcleSim software (the browser, the solver programs, the animator, the plotter, etc.), and tech memos covering specific topics such as example applications.
Multiple Databases
A VehicleSim database can include datasets for many vehicles, controls, and test conditions. Further, you can have multiple databases on your computer to further organize your work.
2010-04-22
TracePro-v6.03 crack
The development of optical systems, sources and components involves adherence to various system performance criteria and constraints including spatial and angular light output distribution, uniformity, intensity, and spectral characteristics. Achieving these criteria quickly with a manufacturable and cost effective design requires modeling software that is powerful, easy-to-use and accurate. TracePro, renowned in the scientific community for the accuracy of its simulations, offers engineers and scientists the confidence that the performance of the finished products will concur with the simulated design without costly prototype iterations.
TraceProTransparent Lamp with rays traced and CIE plot
TracePro is a comprehensive, versatile software tool for modeling the propagation of light in imaging and non-imaging opto-mechanical systems. Models are created by importing from a lens design program or a Computer Aided Drafting (CAD) program or by directly creating the solid geometry in TracePro. Optical properties are assigned to materials and surfaces in the model. Source rays propagate through the model with portions of the flux of each ray allocated for absorption, specular reflection and transmission, fluorescence and scatter. From the model, ray trace, and analyze:
# Light distributions in illumination and imaging systems
# Stray light, scattered light and aperture diffraction
# Throughput, loss, or system transmittance
# Flux or power absorbed by surfaces and bulk media
# Light scattering in biological tissue
# Polarization effects
# Fluorescence effects
# Birefringence effects
TracePro features a simple, intuitive interface, and short learning curve that is both powerful and user-friendly for engineers and scientists of all disciplines.
TracePro Product Data Sheet
New Features and Enhancements
* Fluorescence
* Increased Ray Trace Speed
* Direction Sensitive Surfaces
* 3-D Textures for RepTiles
* Enhanced Translators for OSLO® , CODE V® , ZEMAX®
* Optimization Add-In
* Surface Source Property Utility NEW for quickly modeling light sources from manufacturers' data sheets
TraceProTransparent Lamp with rays traced and CIE plot
TracePro is a comprehensive, versatile software tool for modeling the propagation of light in imaging and non-imaging opto-mechanical systems. Models are created by importing from a lens design program or a Computer Aided Drafting (CAD) program or by directly creating the solid geometry in TracePro. Optical properties are assigned to materials and surfaces in the model. Source rays propagate through the model with portions of the flux of each ray allocated for absorption, specular reflection and transmission, fluorescence and scatter. From the model, ray trace, and analyze:
# Light distributions in illumination and imaging systems
# Stray light, scattered light and aperture diffraction
# Throughput, loss, or system transmittance
# Flux or power absorbed by surfaces and bulk media
# Light scattering in biological tissue
# Polarization effects
# Fluorescence effects
# Birefringence effects
TracePro features a simple, intuitive interface, and short learning curve that is both powerful and user-friendly for engineers and scientists of all disciplines.
TracePro Product Data Sheet
New Features and Enhancements
* Fluorescence
* Increased Ray Trace Speed
* Direction Sensitive Surfaces
* 3-D Textures for RepTiles
* Enhanced Translators for OSLO® , CODE V® , ZEMAX®
* Optimization Add-In
* Surface Source Property Utility NEW for quickly modeling light sources from manufacturers' data sheets
2010-04-21
Techlog Interactive Suite 2010 crack
A fully integrated Application module that allows the 2D display of well locations held in the Project together with formation properties (e.g. porosity, saturation etc.) or summarised log and core data (e.g. minimum value, maximum value, average etc.) as contour maps.
New developments
* Display the desired set of wells in a 2D map viewer by a single drag & drop from the Project Browser. Well symbols (oil producer, gas injector,...) retrieved from the Project data store as a well property.
* Compute any chosen value or parameter from the logs, cores or results in the wells as a surface using Kriging as the contouring algorithm. Interactively adjust the variogram parameters to investigate data uncertainty across the fi eld or Project
* The data to be mapped can be directly retrieved from the results of the Summaries computation (e.g. average petrophysical property by zone and/or fl uid zone)
* Finished maps can be easily saved for instant retrieval, printing or display within 3DVue
* Based on well deviation and depth to surface, the mapped values are placed at the actual X,Y, locations of the zone whose data is represented by the map. Well trajectories may be projected onto any map
Coming soon
* Ability to load any kind of map from third party software, satellite pictures (with compatible geographic reference system)
* Additional contouring algorithms to be developed
Clarity
The simple principles of a “Data Family” or a “Data Alias” allow you to rapidly harmonise names, units, scales, colours etc. across your entire project, and allow you automatically to control preferential data selection
Access
From potentially many hundreds of wells in a project, use powerful data mining tools to rapidly understand the data that are present and any errors of naming, units and families assignment, etc.
Efficiency
Using the combination of data inventories and detailed data queries, search, fi nd and repair spurious names, units and family/alias assignment. Arrive at fully harmonised datasets ready for efficient multi-well work in a fraction of the time.
New developments
* Display the desired set of wells in a 2D map viewer by a single drag & drop from the Project Browser. Well symbols (oil producer, gas injector,...) retrieved from the Project data store as a well property.
* Compute any chosen value or parameter from the logs, cores or results in the wells as a surface using Kriging as the contouring algorithm. Interactively adjust the variogram parameters to investigate data uncertainty across the fi eld or Project
* The data to be mapped can be directly retrieved from the results of the Summaries computation (e.g. average petrophysical property by zone and/or fl uid zone)
* Finished maps can be easily saved for instant retrieval, printing or display within 3DVue
* Based on well deviation and depth to surface, the mapped values are placed at the actual X,Y, locations of the zone whose data is represented by the map. Well trajectories may be projected onto any map
Coming soon
* Ability to load any kind of map from third party software, satellite pictures (with compatible geographic reference system)
* Additional contouring algorithms to be developed
Clarity
The simple principles of a “Data Family” or a “Data Alias” allow you to rapidly harmonise names, units, scales, colours etc. across your entire project, and allow you automatically to control preferential data selection
Access
From potentially many hundreds of wells in a project, use powerful data mining tools to rapidly understand the data that are present and any errors of naming, units and families assignment, etc.
Efficiency
Using the combination of data inventories and detailed data queries, search, fi nd and repair spurious names, units and family/alias assignment. Arrive at fully harmonised datasets ready for efficient multi-well work in a fraction of the time.
MICROMINE-v11
MICROMINE is a toolbox of solutions that allows you to capture, manage and interpret critical mining and exploration data. As an explorer, MICROMINE provides you with an in-depth understanding of your project so you can target prospective regions more accurately, increasing the chance of your project’s success. As a miner, MICROMINE gives you easy-to-use modelling, estimation, and design tools to simplify your day-to-day design and production tasks.
MICROMINE comprises nine modules giving you the flexibility to choose what you need as you need it, as your operation expands or your requirements change.
Core
The heart of MICROMINE, Core allows you to import, validate, visualise and interpret surface, drillhole and subsurface data. Users or third parties gain a rapid and in-depth understanding of the data using industry-standard 3D graphics.
* Vizex 3D viewing environment
* Compatibility with many third party file formats
* Graphically interpret drillhole and other data
* Display all supported MICROMINE data types
* Essential statistical and coordinate conversion tools
* Automate repetitive tasks using macros
* Easily communicate ideas to non-technical audiences using fly through animations or VRML scenes
Exploration
The Exploration module provides a set of tools for working in detail with drillhole data, including the performance of statistical calculations and DTM surfaces or grids.
* Drillhole calculations
* Statistical and geostatistical calculations
* Enhanced display capabilities; pie charts, oriented diamond drill structures, 3D contours
* Digital terrain modelling and calculations
Wireframing
The Wireframing module allows you to build and manipulate triangulated 3D solids and surfaces. Analytical tools include flagging 3D data as being inside or outside a solid or above or below a surface, grade-tonnage calculations, and many other spatial operations
* Use a wireframe solid and drillhole assay data to quickly calculate a grade/tonnage
* Use interactive Boolean operations to intersect two or more wireframes, or the menu version to batch process many wireframes via a macro
* Build polygonal solids from a profile, or slice a wireframe using sequential planes in any orientation
* Modify wireframe coordinates by rotation, scaling, translation, or geographic coordinate conversion
* Calculate drillhole pierce points from a wireframe
* Construct wireframe solids from a variety of data types
Resource Estimation
The Resource Estimation module provides a comprehensive range of modelling related functions, you can:
* Classify, quantify, and report the grade and tonnage of a resource model
* Create grade/ tonnage curves in preparation for reserve estimation
* Unfold or flatten a block model
* Supports all common interpolation methods from IDW through to Multiple Indicator Kriging (MIK)
* Also supports 2D polygonal methods for extremely simple or extremely complex deposits
Pit Optimisation
Pit Optimisation allows users to find the most profitable open pit or nested pits using industry-standard Lerchs-Grossman optimisation.
* Enhanced pit optimisation including variable slope angles, dilution, recovery, rehabilitation costs and analysis
* Use function parameters, variable element prices, or periodic capital expenditure for more complex projects
* Enhanced block model reporting
* Support for multiple slope regions and processing methods with multiple elements per rock type
Mining
The Mining module allows you to develop a mine plan based on your organisation’s mining parameters and business fundamentals.
* Functions for designing open pits, haul roads, slot ramps, switch backs and cutbacks
* Functions for designing underground drives, rises, shafts, declines and inclines
* Calculator for simple conversion between overall slope angle and batter angles/berm widths
* Variable geotechnical parameters for pit design
* Open pit blast pattern design including clipping blastholes to a DTM, calculation of volumes, production of collar/assay files and blast displacement of ore blocks
* Underground ring design tools including drill fans, charging, stemming and volume calculations.
Scheduling
The Scheduling module allows you to schedule and report on mine production by defining mining blocks, resources calendars, and extraction rates.
* Interactive 3D tools combine with Gantt chart and calendar interfaces to provide a truly integrated environment
* Spatially define a mining sequence
* Set up resources and calendars in Gantt chart or calendar interfaces
* Interactively re-sequence tasks on the Gantt chart and see the effect in 3D
* Use a block model to generate time-based grade/tonnage reports
Surveying
The Surveying module comprises tools for importing and processing survey data. It provides calculation facilities for points, strings, surfaces and volumes.
* Tools to import data from any data recorder or total station text format
* Functions to reduce raw survey observations and to calculate and adjust coordinates
* Create and work with Digital Terrain Models (DTMs)
* Calculate volumes from DTMs or cross sections
more please vist caxcrack
MICROMINE comprises nine modules giving you the flexibility to choose what you need as you need it, as your operation expands or your requirements change.
Core
The heart of MICROMINE, Core allows you to import, validate, visualise and interpret surface, drillhole and subsurface data. Users or third parties gain a rapid and in-depth understanding of the data using industry-standard 3D graphics.
* Vizex 3D viewing environment
* Compatibility with many third party file formats
* Graphically interpret drillhole and other data
* Display all supported MICROMINE data types
* Essential statistical and coordinate conversion tools
* Automate repetitive tasks using macros
* Easily communicate ideas to non-technical audiences using fly through animations or VRML scenes
Exploration
The Exploration module provides a set of tools for working in detail with drillhole data, including the performance of statistical calculations and DTM surfaces or grids.
* Drillhole calculations
* Statistical and geostatistical calculations
* Enhanced display capabilities; pie charts, oriented diamond drill structures, 3D contours
* Digital terrain modelling and calculations
Wireframing
The Wireframing module allows you to build and manipulate triangulated 3D solids and surfaces. Analytical tools include flagging 3D data as being inside or outside a solid or above or below a surface, grade-tonnage calculations, and many other spatial operations
* Use a wireframe solid and drillhole assay data to quickly calculate a grade/tonnage
* Use interactive Boolean operations to intersect two or more wireframes, or the menu version to batch process many wireframes via a macro
* Build polygonal solids from a profile, or slice a wireframe using sequential planes in any orientation
* Modify wireframe coordinates by rotation, scaling, translation, or geographic coordinate conversion
* Calculate drillhole pierce points from a wireframe
* Construct wireframe solids from a variety of data types
Resource Estimation
The Resource Estimation module provides a comprehensive range of modelling related functions, you can:
* Classify, quantify, and report the grade and tonnage of a resource model
* Create grade/ tonnage curves in preparation for reserve estimation
* Unfold or flatten a block model
* Supports all common interpolation methods from IDW through to Multiple Indicator Kriging (MIK)
* Also supports 2D polygonal methods for extremely simple or extremely complex deposits
Pit Optimisation
Pit Optimisation allows users to find the most profitable open pit or nested pits using industry-standard Lerchs-Grossman optimisation.
* Enhanced pit optimisation including variable slope angles, dilution, recovery, rehabilitation costs and analysis
* Use function parameters, variable element prices, or periodic capital expenditure for more complex projects
* Enhanced block model reporting
* Support for multiple slope regions and processing methods with multiple elements per rock type
Mining
The Mining module allows you to develop a mine plan based on your organisation’s mining parameters and business fundamentals.
* Functions for designing open pits, haul roads, slot ramps, switch backs and cutbacks
* Functions for designing underground drives, rises, shafts, declines and inclines
* Calculator for simple conversion between overall slope angle and batter angles/berm widths
* Variable geotechnical parameters for pit design
* Open pit blast pattern design including clipping blastholes to a DTM, calculation of volumes, production of collar/assay files and blast displacement of ore blocks
* Underground ring design tools including drill fans, charging, stemming and volume calculations.
Scheduling
The Scheduling module allows you to schedule and report on mine production by defining mining blocks, resources calendars, and extraction rates.
* Interactive 3D tools combine with Gantt chart and calendar interfaces to provide a truly integrated environment
* Spatially define a mining sequence
* Set up resources and calendars in Gantt chart or calendar interfaces
* Interactively re-sequence tasks on the Gantt chart and see the effect in 3D
* Use a block model to generate time-based grade/tonnage reports
Surveying
The Surveying module comprises tools for importing and processing survey data. It provides calculation facilities for points, strings, surfaces and volumes.
* Tools to import data from any data recorder or total station text format
* Functions to reduce raw survey observations and to calculate and adjust coordinates
* Create and work with Digital Terrain Models (DTMs)
* Calculate volumes from DTMs or cross sections
more please vist caxcrack
2010-04-16
Sema-EXPERIENCE-v11-usb-dongle-crack
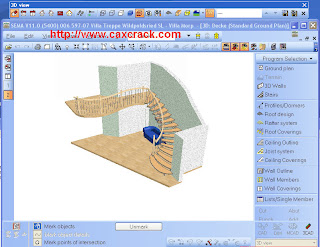
SEMA EXPERIENCE V11.0: The Easy Way to Build on a Slope
On the trade fairs in spring and summer 2009, SEMA will introduce a completely new module called ‘Terrain Designer’. Many customers asked for it and so SEMA integrated this new module into the SEMA EXPERIENCE V11.0 program package, which makes it fast and simple to use.
The easy way to build on a slope,
or on the coast:
With this new program part, any topography can be created and visualized directly with the timber construction program.
And, of course, it is also possible to automatically create sectional views of buildings on a slope where all the height information is displayed as well.
Nevertheless, the SEMA programmers were able to keep operation as simple as possible and user-friendly.
Structural Analysis Perfectly Integrated
This is as easy as it gets: Timber and steel components can be analysed directly during the design stage - whether it is in Ground Plan or in 3D - and then be optionally transferred to the FRILO structural analysis software. All geometric data, component dimensions and material codes are automatically taken into account.
FRILO - A Strong Partner
The company Friedrich + Lochner, with their main office in Stuttgart, Germany, has been developing calculation programs for structural analysis for 30 years. The new generation of standards with semi-probalistic safety concepts is quite a challenge for construction engineers as well as for software developers
2010-04-14
OPTICAL-RESEARCH-ASSOCIATES-LIGHTTOOLS-V7.0
LightTools® is a unique optical engineering and design software product that features virtual prototyping, simulation, optimization, and photorealistic renderings of illumination applications. The software has adapted solid modeling technology to accommodate the inherent accuracy required to simulate ray paths of light as they traverse through and within optical elements and mechanical structures. LightTools is straightforward to use, accurate, has the most advanced capabilities commercially available, and supports the tasks of design and engineering iterations in addition to analysis.A Robust Design and Analysis Tool
LightTools' unique power lies in its complementary strengths of design and analysis. The analysis gives you the status of how well your design is working against spec. The design features help you quickly and efficiently improve the design, in both the initial concept phase and during engineering iterations and refinements. This coupling of benefits (design and analysis) makes LightTools really pay off in terms of productivity improvement, faster time to market, and better engineered products.
Build and Modify
While analysis requires only the initial creation or importing of geometry, practical design requires quick and simple geometry modifications. You can perform easy design modifications because LightTools' implementation of Boolean operations and trimming operations retains the parametric information about how the geometry was created. Surface and material properties are also maintained as you edit the model, allowing quick analysis of multiple design forms.
LightTools' basic 3D solid primitives, sphere, ellipse, toroid, block, cylinder (including cone), extrusion and rotationally swept polyline, can be parametrically edited and inserted with any size, in any location, and at any angle. Complex objects previously defined using Boolean operations can be edited at any time (even after the object is complete). Each solid can be combined with any other solid (native or imported) using the Boolean operations, union, intersection, and subtraction. This allows the creation of complex, as-fabricated, models, such as segmented reflectors and multifaceted lightpipes. Note that the complex elements can be optical, mechanical, or structural components. And of course, LightTools can also import and export CAD data in several standard and product-specific formats.
Create Complex 3D Objects Quickly and Easily
LightTools' "skinned solids" feature allows you to build extremely complex 3D objects simply by specifying their transverse cross sections, available in various shapes, at two or more points. The software then automatically constructs the longitudinal structure between these shapes. Furthermore, you can specify the longitudinal surface profile to be straight lines, cubic splines, or even Bezier curves. The precise shape of the skinned solids can then be adjusted automatically using the LightTools optimizer.
Point-and-Shoot Ray Tracing
Your understanding of the optical behavior of a complex illumination system is greatly enhanced because you can graphically start and aim rays from any point in your model, even from inside parts. Rays are displayed visually and automatically update as the model is changed, and rays can be moved or rotated interactively to probe the behavior of a model.
Link from caxcrack
LightTools' unique power lies in its complementary strengths of design and analysis. The analysis gives you the status of how well your design is working against spec. The design features help you quickly and efficiently improve the design, in both the initial concept phase and during engineering iterations and refinements. This coupling of benefits (design and analysis) makes LightTools really pay off in terms of productivity improvement, faster time to market, and better engineered products.
Build and Modify
While analysis requires only the initial creation or importing of geometry, practical design requires quick and simple geometry modifications. You can perform easy design modifications because LightTools' implementation of Boolean operations and trimming operations retains the parametric information about how the geometry was created. Surface and material properties are also maintained as you edit the model, allowing quick analysis of multiple design forms.
LightTools' basic 3D solid primitives, sphere, ellipse, toroid, block, cylinder (including cone), extrusion and rotationally swept polyline, can be parametrically edited and inserted with any size, in any location, and at any angle. Complex objects previously defined using Boolean operations can be edited at any time (even after the object is complete). Each solid can be combined with any other solid (native or imported) using the Boolean operations, union, intersection, and subtraction. This allows the creation of complex, as-fabricated, models, such as segmented reflectors and multifaceted lightpipes. Note that the complex elements can be optical, mechanical, or structural components. And of course, LightTools can also import and export CAD data in several standard and product-specific formats.
Create Complex 3D Objects Quickly and Easily
LightTools' "skinned solids" feature allows you to build extremely complex 3D objects simply by specifying their transverse cross sections, available in various shapes, at two or more points. The software then automatically constructs the longitudinal structure between these shapes. Furthermore, you can specify the longitudinal surface profile to be straight lines, cubic splines, or even Bezier curves. The precise shape of the skinned solids can then be adjusted automatically using the LightTools optimizer.
Point-and-Shoot Ray Tracing
Your understanding of the optical behavior of a complex illumination system is greatly enhanced because you can graphically start and aim rays from any point in your model, even from inside parts. Rays are displayed visually and automatically update as the model is changed, and rays can be moved or rotated interactively to probe the behavior of a model.
Link from caxcrack
Subscribe to:
Posts (Atom)