The VeSys Design course was developed to provide a comprehensive introduction to VeSys Design concepts and functionality. It will cover the basic functions required for the creation of electrical Wiring diagrams as well as the circuit analysis features available to the designer.
You will learn how to
Create functional wiring/circuit diagrams
Setup Electrical parts in the component database
Perform Simulation and Analysis
Input Behavioral models of Electronic Control Units
Generate Reports
Generate Reports
Hands-On Labs
Throughout this course, extensive hands-on lab exercises provide you with practical experience using the Vesys software. Hands-on lab topics include:
Creation of wiring and functional diagrams
Creation of components
Creation of reports
Audience
Circuit/Schematic design engineers that use VeSys Design in their daily work process.
Prerequisites
Participants should be familiar with electrical schematic diagrams
Key Topics
Component Data Input and Maintenance
Electrical Components
Connecting Components
Custom Components and Logic
Inline and Component Connectors
Simulation and Analysis
Data Export and Reports
Configuration
2009-01-31
HALCON 9.0 crack MVTec Software GmbH
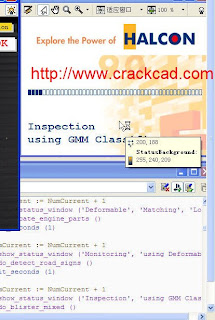
MVTec Software GmbH, HALCON 9.0
Faster Processing
Profit from the speedup of the entire HALCON library
The entire HALCON library again is faster by improved algorithms, extended use of SSE technology, and a comprehensive utilization of multi-core and multi-processor hardware. HALCON's automatic operator parallelization, industry-proven for 8 years, has been accelerated by more than 20% and now runs more than 400 operators in parallel, such as filters, matching, 3D matching, subpixel extraction, and FFT.
Extremely Robust Matching
Rely on HALCON's revolutionary new matching technologies
introduces two new matching technologies for robustly finding perspectively distorted objects: descriptor-based matching, which is based on the detection of interest points, and perspective, deformable matching, which uses a shape-based approach. These technologies supplement HALCON's powerful matching methods for every application.
Complete 3D Vision
Take the first choice for 3D vision
HALCON 9.0 again offers many new methods for 3D vision, making HALCON the only software you need for your application. These methods include, but are not limited to the above mentioned new matching technologies, as well as multigrid stereo that reconstructs stereo images without texture in entire image parts for high-precision results, and sheet-of-light measurement. Furthermore, HALCON's comprehensive 3D calibration, which is crucial for 3D vision as well as for highly precise measuring, is strongly enhanced.
Faster Development
Speed up your development by improved usability
HALCON's integrated development environment (IDE) HDevelop includes many enhancements, such as a full text editor, an alternative to the established dialog-based editor. The new editor speeds up the development and provides many intelligent editing features, e.g., advanced autocompletion. The new HDevelop calibration assistant evaluates the quality of calibration images and helps you to easily and accurately perform the camera calibration. Furthermore, HALCON 9.0 comes with a huge amount of new source code modules and classes – HALCON codelets. These are used outside HDevelop as templates for new applications or directly called within newly developed code.
Higher Resolution
Process extremely large images with HALCON XL
With the version 9.0, HALCON is able to process images in practically unlimited image size, even larger than 32k x 32k. This lets you process images of any width and any height. The limitation only depends on available memory and the used operating system. This new feature comes as a separate IDE and library, named HALCON XL. Of course, HALCON XL covers the full HALCON library.
Thanks to HALCON XL, even demanding line scan camera applications now can be realized – even if the height of the scanned image exceeds 32k.
Further New Features
* Upgraded GigE Vision interface
* Operators with timeout
* New increased tolerance mode for shape-based matching
* Model generation from DXF files
* Improved hand-eye calibration
* Extended documentation
* Correction of lens distortions without calibration plate
* Enhanced 3D visualization techniques, e.g., for 3D plots
* Exception handling in HDevelop
* Documentation mechanism for HDevelop procedures
* Faster and improved bar code reader for all RSS codes (incl. composites)
* Print quality inspection for further standards
* More robust data code reader and enhanced ECC200 reader
* Large set of matrix operators
* Fast color space transformation
* And many, many more...
2009-01-29
Siemens PLM FEMAP 10.0 license crack
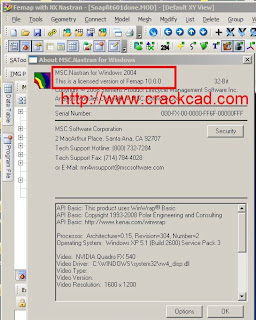
Femap provides comprehensive functionality in an independent environment for modeling, simulation and review of product performance results.
Geometry creation:Boolean and extrude/revolve solid modeling; mid-surface extraction; project curves onto surfaces; intersect surfaces to create curves; define regions by projecting curves on solid; create curves based on U-V space on surfaces; shell solids with constant thickness; rule, revolve, extrude and loft surfaces; stitch surfaces into solids; create points, lines, arcs, circles and splines;. break, trim, extend, join, fillet, offset and copy geometric entities.
Import or export: DXF and IGES points and curves, stereolithography (SLA) data, ACIS (.sat) Parasolid (.x_t) parts or assemblies. CATIA import model files, and Express files from CATEXP. (CATIA v4.1.x, v4.2, or v5) , VDA Import (up to v2.0), I-deas import (MS8), Pro/E import.(v16 to v20), Solid Edge import, Unigraphics NX import.( v11 through NX v4).
Meshing: Global and local controls with default sizing. Define element size or spacing with bias. Free surface meshing, quads or triangles only. Mapped meshing with quads or bricks. Direct generation of line, shell and solid elements. Extrude and revolve geometric curves or line elements into shell elements, shell elements can be extruded or revolved to form solid elements. Connected shell elements can be extruded normal to themselves to turn thin-shell models into solid ones. Mesh refinement and smoothing. Subdivision and semi-automatic meshing of solids, Automatic solid meshing with tetrahedral elements.
Materials:Isotropic, orthotropic and anisotropic. Nonlinear elastic, bi-linear and plastic. Hardening: isotropic or kinematic. Hyperelasticity, creep and composites. Temperature and strain rate dependence. User extensible library included.
Loads and constraints:Geometry or finite element based. Associativity between geometry and mesh. Load case definition and management. Fixed (non-zero) displacements and rotations. Multipoint constraint equations (MPCs). Nodal forces and moments. Distributed loads on line elements. Constant or variable pressure. Velocities and accelerations. Transient dynamic, frequency and random vibration. Temperatures, heat generation or flux. Convection and radiation.
User interface: Native Windows look and feel. Multiple graphics windows. Multiple model interface. Full, multi-level undo/redo. On-line help with hypertext links. Floating dockable toolbars to access frequently used commands. Toolbar entity editor. Model info tree and entity editor. Data manipulation through the data table. Cut and paste images into Windows applications. Dynamic highlight during selection operations. Box, circle, polygon, front, depth and query picking of geometric and FEA entities. Select entities by associativity (all elements connected to specified nodes, all elements of a specified property).
Element library:1-D: rod, tube, bar, beam, spring, gap. Full support of arbitrary and standard cross-sections including all property calculations. 2-D planar solid. 3-D surface or solid. Planar and surface: quads and triangles. 3-D solid: tetra, wedge and brick. All 2- and 3-D elements: linear or parabolic. 2-D planar: plane strain or stress, axisymmetric. 3-D surface: shear panel or membrane. Mass and general stiffness matrices. Contact lines and surfaces, and slide lines. Spot weld elements.
Customization: Record, edit and playback user-defined macros. Full features, object oriented, OLE/COM-based programming API, can be directly accessed from fully integrated VB compatible BASIC Scripting development environment. Neutral file: fully documented ASCII file format.
Groups and Layers:With Femap you can easily subdivide your model for visualization or post-processing purposes,.. Automatically add new entities to active or user-specified group. Group by ID, associativity, material, property, and type. Automatic group creation based on properties, materials, and geometric constraints.
Results:Deformations, animations, and vector displays. Single- and multi-load set animations. Filled color contours and criteria displays. Isosurface and cutting planes, with dynamic control. Shear and bending moment diagrams. Error estimates. Results across composite laminates. Extensive result sorting capabilities. X-Y Plots with multiple curves. Text reports: standard and user-customized. Interactive data query with mouse. Freebody displays, including grid point force balance support for grouped entities. Import/export in comma separated tables. Internet publishing with VRML support. Save animations with AVI support.
Graphics:Dual Windows GDI (vector-based) and OpenGL graphics. 3-D dynamic pan, zoom and rotation. Hidden line and wireframe display. Free edge and free face display. Light source shading and transparency.
2009-01-22
Predator Virtual CNC V8
Predator Virtual CNC is software designed to simulate and verify operation of your CNC machines on your PC. By simulating the machining process off line you literally save thousands of dollars in lost time, scrapped parts, broken tools, machine crashes and improve overall machine productivity.
What can it do for me?
Running a profitable manufacturing shop floor is challenging. And keeping it productive is tough work. Those that succeed embrace technology. Over 1000 manufacturers and job shops rely on Predator Virtual CNC to keep their CNC machines running reliably while minimizing errors.
Eliminate expensive mistakes
Prove out processes offline
Simplify CNC Setup
Minimize waste
Organizes release to shop floor process
Gets started quickly and easily
Performing off line simulations has many, many other benefits including:
Increase Productivity - off line simulation frees your machines to run jobs that are making you revenues, not costing you profits...
Maximize Resources - off line simulation adds to tooling life, saves coolant for "real" jobs, reduces "wear and tear" on expensive machine tools, and much more...
Ensure Quality - verify surface finish, feature dimensions, cutter path, tool and holder clearance, gouge checking, and more...
Looking for a better way to prove out your parts? With Virtual CNC™ from Predator Software you have full featured, true solids based NC code verification and simulation capabilities on your PC.
Includes the following features:
Easy to use with standard Windows interface and online help
2, 3, 4 & 5 Axis Milling
2 Axis Turning
True Solids
Comprehensive G & M code support
APTCL, NCI and INC support
Error Detection
Part Inspection prior to machining
Includes support for over a 100 CNC controls
User Configurable Reverse Post Processor
Automatic Gouge Detection
Multiple Parts, Fixtures, Tombstones and Processes
Lots of customization options
Advanced Tooling
Complex Stock and Fixtures
CAD Compare for 'Designed vs Machined' analysis
Full Machine Simulation with collision detection
Predator CNC Editor
Predator API and ActiveX development platform
Milling - 2, 3, 4 & 5 Axis
Predator Virtual CNC™ supports all standard milling machine configurations with 3 to 5 driven axes. User definable machine tool configurations with our flexible reverse post processors allows standard VMCs and HMCs to be supported. Standard milling and drilling cycles are all supported.
What can it do for me?
Running a profitable manufacturing shop floor is challenging. And keeping it productive is tough work. Those that succeed embrace technology. Over 1000 manufacturers and job shops rely on Predator Virtual CNC to keep their CNC machines running reliably while minimizing errors.
Eliminate expensive mistakes
Prove out processes offline
Simplify CNC Setup
Minimize waste
Organizes release to shop floor process
Gets started quickly and easily
Performing off line simulations has many, many other benefits including:
Increase Productivity - off line simulation frees your machines to run jobs that are making you revenues, not costing you profits...
Maximize Resources - off line simulation adds to tooling life, saves coolant for "real" jobs, reduces "wear and tear" on expensive machine tools, and much more...
Ensure Quality - verify surface finish, feature dimensions, cutter path, tool and holder clearance, gouge checking, and more...
Looking for a better way to prove out your parts? With Virtual CNC™ from Predator Software you have full featured, true solids based NC code verification and simulation capabilities on your PC.
Includes the following features:
Easy to use with standard Windows interface and online help
2, 3, 4 & 5 Axis Milling
2 Axis Turning
True Solids
Comprehensive G & M code support
APTCL, NCI and INC support
Error Detection
Part Inspection prior to machining
Includes support for over a 100 CNC controls
User Configurable Reverse Post Processor
Automatic Gouge Detection
Multiple Parts, Fixtures, Tombstones and Processes
Lots of customization options
Advanced Tooling
Complex Stock and Fixtures
CAD Compare for 'Designed vs Machined' analysis
Full Machine Simulation with collision detection
Predator CNC Editor
Predator API and ActiveX development platform
Milling - 2, 3, 4 & 5 Axis
Predator Virtual CNC™ supports all standard milling machine configurations with 3 to 5 driven axes. User definable machine tool configurations with our flexible reverse post processors allows standard VMCs and HMCs to be supported. Standard milling and drilling cycles are all supported.
2009-01-21
Delft3D 3.28
Delft3D is a world leading 2D/3D modelling system to investigate hydrodynamics, sediment transport and morphology and water quality for fluvial, estuarine and coastal environments.
The software is used and has proven his capabilities on many places around the world, like the Netherlands, USA, Hong Kong, Singapore, Australia, Venice, etc. The software is continuously improved and developed with innovating advanced modelling techniques as consequence of the research work of our institute and to stay world leading
The FLOW module is the heart of Delft3D and is a multi-dimensional (2D or 3D) hydrodynamic (and transport) simulation program which calculates non-steady flow and transport phenomena resulting from tidal and meteorological forcing on a curvilinear, boundary fitted grid.
In 3D simulations, the vertical grid is defined following the so-called sigma coordinate approach. This results in a high computing efficiency because of the constant number of vertical layers over the whole of the computational field.
For a brief description of Delft3D we refer to the module descriptions on our website.
For a detailed and comprehensive description we refer to the user manuals. These can be found in the download section of this website
The software is used and has proven his capabilities on many places around the world, like the Netherlands, USA, Hong Kong, Singapore, Australia, Venice, etc. The software is continuously improved and developed with innovating advanced modelling techniques as consequence of the research work of our institute and to stay world leading
The FLOW module is the heart of Delft3D and is a multi-dimensional (2D or 3D) hydrodynamic (and transport) simulation program which calculates non-steady flow and transport phenomena resulting from tidal and meteorological forcing on a curvilinear, boundary fitted grid.
In 3D simulations, the vertical grid is defined following the so-called sigma coordinate approach. This results in a high computing efficiency because of the constant number of vertical layers over the whole of the computational field.
For a brief description of Delft3D we refer to the module descriptions on our website.
For a detailed and comprehensive description we refer to the user manuals. These can be found in the download section of this website
2009-01-12
CODE V9.82
The latest version of CODE V delivers enhancements to the Geometric Spot Diagram feature which offer designers greater ease of use and efficiency. Specifically, CODE V 9.82 enables users to specify the desired accuracy level of the RMS spot computation, and the software then automatically determines the minimum ray grid necessary to achieve this precision. This is a more efficient method than that used by other software programs, which require users to set the ray grid density manually, and then iteratively increase this density until spot size precision stabilizes. Moreover, CODE V now uses separate ray grids for computation and graphing purposes to yield accurate spot size computations along with a less dense plotted ray density for optimal visualization of the spot structure.
The Spot Diagram graphical display also now supports various reference overlays (e.g., Airy disk and/or detectors) and annotations, which is useful for design reviews and presentations. Two new macro functions provide access to virtually all spot size data, greatly improving the user’s ability to perform customized analysis, optimization, and tolerancing.
In addition, this release contains several other smaller enhancements based on customer input, including:
* Enhancements that provide greater flexibility when using gradient-index lens materials within non-sequential surface ranges.
* The addition of several new sample files, including lenses, sample images for use with the 2D Image Simulation feature, and macros. For example, the new FISHEYE2 sample lenses illustrates system modeling issues for a lens with a hyper-hemispheric field of view.
* Performance improvements that speed up tolerancing on RMS spot diameter.
* Improvements to CODE V’s ray tracing processes that have resulted in a 50% ray trace speedup for optical systems in which polarization ray tracing is activated. This performance enhancement has been in place since the CODE V 9.81 release, but was not previously reported.
CODE V also now uses separate ray grids for computation and graphing purposes to yield accurate spot size computations along with a less dense plotted ray density for optimal visualization of the spot structure.
The Spot Diagram graphical display supports various reference overlays (e.g., Airy disk and/or detectors) and annotations, which is useful for design reviews and presentations. Two new macro functions provide access to virtually all spot size data, improving the user's ability to perform customized analysis, optimization, and tolerancing.
The release contains several other smaller enhancements based on customer input. These include enhancements when using gradient-index lens materials within non-sequential surface ranges and the addition of several new sample files (e.g., lenses, images, and macros).
The Spot Diagram graphical display also now supports various reference overlays (e.g., Airy disk and/or detectors) and annotations, which is useful for design reviews and presentations. Two new macro functions provide access to virtually all spot size data, greatly improving the user’s ability to perform customized analysis, optimization, and tolerancing.
In addition, this release contains several other smaller enhancements based on customer input, including:
* Enhancements that provide greater flexibility when using gradient-index lens materials within non-sequential surface ranges.
* The addition of several new sample files, including lenses, sample images for use with the 2D Image Simulation feature, and macros. For example, the new FISHEYE2 sample lenses illustrates system modeling issues for a lens with a hyper-hemispheric field of view.
* Performance improvements that speed up tolerancing on RMS spot diameter.
* Improvements to CODE V’s ray tracing processes that have resulted in a 50% ray trace speedup for optical systems in which polarization ray tracing is activated. This performance enhancement has been in place since the CODE V 9.81 release, but was not previously reported.
CODE V also now uses separate ray grids for computation and graphing purposes to yield accurate spot size computations along with a less dense plotted ray density for optimal visualization of the spot structure.
The Spot Diagram graphical display supports various reference overlays (e.g., Airy disk and/or detectors) and annotations, which is useful for design reviews and presentations. Two new macro functions provide access to virtually all spot size data, improving the user's ability to perform customized analysis, optimization, and tolerancing.
The release contains several other smaller enhancements based on customer input. These include enhancements when using gradient-index lens materials within non-sequential surface ranges and the addition of several new sample files (e.g., lenses, images, and macros).
2009-01-10
ZUKEN CadStar V11 license crack
CADSTAR is Zuken’s powerful PCB design solution that allows an intuitive work flow, guiding designers easily through their design process. CADSTAR incorporates all the technologies necessary for a complete electronic development process in a single environment.
The full range of the solution includes schematics, board- and FPGA-level system design, PCB layout, high-speed and signal integrity, analysis, 3D, and creation of manufacturing output, complemented by complete data management capabilities and extensive internet-accessible libraries containing over 200,000 components.
Its price-performance, coupled with a scalable design environment, provides total flexibility to engineers of small- to mid-sized EDA development teams.
Intuitive work flow
Throughout CADSTAR’s Schematic and PCB design editors, the menu items and options are all in the same location, providing intuitive guidance through the design process.
Fast design cycle
Zuken’s P.R.Editor XR HS (Place & Route High-Speed) is at the heart of CADSTAR. With a 'right-first-time' approach, this powerful placement and routing tool is optimized for speed and accuracy, tackling today’s dense PCB design challenges with creativity and intelligent automation.
CADSTAR’s fully integrated 3D environment dramatically reduces design time by using proven technology from the verification and timing analysis engines in Zuken’s high-end solutions.
Migration preserves legacy data
Migrating from PADS or other tools to CADSTAR is simple. Users can move all the data over to CADSTAR from previous designs, re-using symbols, footprints and other supporting design data and benefit from the ability to re-work legacy designs.
The full range of the solution includes schematics, board- and FPGA-level system design, PCB layout, high-speed and signal integrity, analysis, 3D, and creation of manufacturing output, complemented by complete data management capabilities and extensive internet-accessible libraries containing over 200,000 components.
Its price-performance, coupled with a scalable design environment, provides total flexibility to engineers of small- to mid-sized EDA development teams.
Intuitive work flow
Throughout CADSTAR’s Schematic and PCB design editors, the menu items and options are all in the same location, providing intuitive guidance through the design process.
Fast design cycle
Zuken’s P.R.Editor XR HS (Place & Route High-Speed) is at the heart of CADSTAR. With a 'right-first-time' approach, this powerful placement and routing tool is optimized for speed and accuracy, tackling today’s dense PCB design challenges with creativity and intelligent automation.
CADSTAR’s fully integrated 3D environment dramatically reduces design time by using proven technology from the verification and timing analysis engines in Zuken’s high-end solutions.
Migration preserves legacy data
Migrating from PADS or other tools to CADSTAR is simple. Users can move all the data over to CADSTAR from previous designs, re-using symbols, footprints and other supporting design data and benefit from the ability to re-work legacy designs.
2009-01-08
PTC CADDS 5i REVISION 15 flexlm crack
As one of the most technologically advanced companies in China's highly competitive shipbuilding industry, Huangpu Shipbuilding's relationship with PTC dates back to 1999. At that time, Huangpu Shipbuilding became the first shipyard in southern China's Guangdong province to purchase PTC CADDS 5i. Huangpu Shipbuilding has relied on PTC CADDS 5i since that time to facilitate its ongoing expansion and modernization.
The suite of CADDS 5i solutions enables users to reference each other's evolving designs and facilitate concurrent engineering in a fully digitized ship design and 3D modeling environment. This sophisticated enterprise application for shipbuilding will shorten product design lead-time and accelerate time-to-market. With its new deployment of CADDS 5i Huangpu Shipbuilding is expected to bring additional revolutionary changes in digitization at its shipyard. CADDS 5i will now be used by 80 additional engineers at Huangpu Shipbuilding.
As in any industrial sector, innovation is key to realizing opportunities and market growth. However, the shipbuilding sector is often marked by lengthy product development cycles, due largely to archaic manual design processes that are still in place. Huangpu Shipbuilding led the industry in adopting CADDS 5i, which offers flexible 3D hybrid modeling and 2D drafting capabilities across a broad application range, easing engineers' workload, and freeing up their time to develop more innovative products.
The suite of CADDS 5i solutions enables users to reference each other's evolving designs and facilitate concurrent engineering in a fully digitized ship design and 3D modeling environment. This sophisticated enterprise application for shipbuilding will shorten product design lead-time and accelerate time-to-market. With its new deployment of CADDS 5i Huangpu Shipbuilding is expected to bring additional revolutionary changes in digitization at its shipyard. CADDS 5i will now be used by 80 additional engineers at Huangpu Shipbuilding.
As in any industrial sector, innovation is key to realizing opportunities and market growth. However, the shipbuilding sector is often marked by lengthy product development cycles, due largely to archaic manual design processes that are still in place. Huangpu Shipbuilding led the industry in adopting CADDS 5i, which offers flexible 3D hybrid modeling and 2D drafting capabilities across a broad application range, easing engineers' workload, and freeing up their time to develop more innovative products.
2009-01-07
SILVACO 2008
Silvaco Europe Ltd. is a wholly-owned subsidiary of Silvaco International. Silvaco International, headquartered in Santa Clara, California, is a leading vendor of TCAD and EDA software. Founded in 1984, and a TCAD leader since 1987, the company is privately held. In 2005 it spun out Simucad Design Automation which now focuses on EDA software. Worldwide customers include leading foundries, fabless semiconductor companies, integrated semiconductor manufacturers, and universities.
VICTORY PROCESS is an open architecture process simulator. VICTORY includes a complete set of advanced models for etch, deposition, implantation, diffusion and oxidation. Company proprietary models and public domain research models can be integrated easily into VICTORY through its open architecture making it suitable for both commercial and academic applications. VICTORY replaces costly wafer experiments with simulations to deliver shorter process development cycles.
TonyPlot3D is a powerful graphics tool, capable of displaying 3D TCAD data generated by Silvaco TCAD process or device simulators and Simucad's 3D parasitic products. It provides visualization and graphic features such as zoom, pan, views and different drawing modes. TonyPlot3D provides a user-friendly environment to view 3D structures in various TCAD specific display modes such as Regions, Contours, Rays, IsoSurfaces and Vectors
The Interactive Tools are a suite of applications that provide interactive GUI based pre and post processing services to Silvaco’s 1D, 2D and 3D TCAD simulators. The tools within the interactive tools suite are fully integrated and provide users with a comfortable environment within which all TCAD simulations can be performed
VICTORY PROCESS is an open architecture process simulator. VICTORY includes a complete set of advanced models for etch, deposition, implantation, diffusion and oxidation. Company proprietary models and public domain research models can be integrated easily into VICTORY through its open architecture making it suitable for both commercial and academic applications. VICTORY replaces costly wafer experiments with simulations to deliver shorter process development cycles.
TonyPlot3D is a powerful graphics tool, capable of displaying 3D TCAD data generated by Silvaco TCAD process or device simulators and Simucad's 3D parasitic products. It provides visualization and graphic features such as zoom, pan, views and different drawing modes. TonyPlot3D provides a user-friendly environment to view 3D structures in various TCAD specific display modes such as Regions, Contours, Rays, IsoSurfaces and Vectors
The Interactive Tools are a suite of applications that provide interactive GUI based pre and post processing services to Silvaco’s 1D, 2D and 3D TCAD simulators. The tools within the interactive tools suite are fully integrated and provide users with a comfortable environment within which all TCAD simulations can be performed
2009-01-03
2008.12 0DAY SOFTWARE
2008-12-31 Dassault Systemes CATIA v6 2009
2008-12-28 Cosmic.Software.Suite.v10.2008
2008-12-27 PTC.PRO.ENGINEER.WILDFIRE.V4.M060
2008-12-25 Accelrys.Materials.Studio.V4.3
2008-12-25 PTC.PRO.ENGINEER.WILDFIRE.v3.0.M190
2008-12-25 Accelrys.Pipline.Pilot.v7.01.Linux.Win.MERRY.CHRISTMAS
2008-12-25 Bentley.Architecture.V8i.XM.v8.11.05.46
2008-12-25 Bentley.Generative.Components.V8i.XM.v8.11.05.36
2008-12-25 Bentley.Map.V8i.XM.v8.11.05.26
2008-12-25 Bentley.Microstation.Powerdraft.v8i.XM.v8.11.05.17
2008-12-24 Siemens.Solid.Edge.ST.v100.0.Retail.x64.GERMAN.MERRY.CHRISTMAS
2008-12-23 MAGMASOFT.V4.4
2008-12-23 SOFTWARE.CRADLE.SC.TETRA.V7
2008-12-22 PGI.Visual.Fortran.2008.v8.0.2
2008-12-21 Right.Hemisphere.Deep.Exploration.CAD.Edition.v5.7.0.4228
2008-12-19 Shop.Talk.CAD.CAM.v8.0
2008-12-19 GibbsCAM.2009.V9.0.6
2008-12-18 Bentley.MicroStation.V8i.XM.v8.11.05.17
2008-12-17 3DVia.Composer.v2009x.WiNNT2K.RTFM
2008-12-16 Compusoft.Winner.v8.0a1.MULTILANG
2008-12-15 Strata_3D_CX_v5.6
2008-12-14 AUTODESK_LUSTRE_V2009
2008-12-14 Autodesk.Stitcher.Unlimited.2009.Build61.x86
2008-12-13 CIMCO.Software.Suite.v5.12.28
2008-12-12 Cedrat.Flux.v10.2.WiNNT2K
2008-12-11 Dassault.Systemes.3DVIA.Composer.v6R2009
2008-12-09 Tecplot.RS.2009.v11.3.29.1445
2008-12-08 CD-adapco.Star-CCM.Plus.and.Cad.Series.v3.06.Windows&Linux
2008-12-07 Embarcadero.ERStudio.v8.0.0.5865
2008-12-07 MicroSurvey.CAD.2009.Premium
2008-12-06 Hampson.Russell.CE8.R3.1
2008-12-06 Accelrys.Discovery.Studio.v2.1.Windows
2008-12-05 Siemens.Tecnomatix.v8.2
2008-12-04 Mastercam_X3_MU1
2008-12-03 AVL_FIRE_V8.5 FOR WINDOWS
2008-12-02 Klocwork.Insight.v8.0.7.1
2008-12-02 GIBBSCAM.2009.V9.0.5
2008-12-01 Delcam_Powershape_v8008
2008-12-01 AUTODESK.MOTIONBUILDER.V2009
FORM CAXSOFT
2008-12-28 Cosmic.Software.Suite.v10.2008
2008-12-27 PTC.PRO.ENGINEER.WILDFIRE.V4.M060
2008-12-25 Accelrys.Materials.Studio.V4.3
2008-12-25 PTC.PRO.ENGINEER.WILDFIRE.v3.0.M190
2008-12-25 Accelrys.Pipline.Pilot.v7.01.Linux.Win.MERRY.CHRISTMAS
2008-12-25 Bentley.Architecture.V8i.XM.v8.11.05.46
2008-12-25 Bentley.Generative.Components.V8i.XM.v8.11.05.36
2008-12-25 Bentley.Map.V8i.XM.v8.11.05.26
2008-12-25 Bentley.Microstation.Powerdraft.v8i.XM.v8.11.05.17
2008-12-24 Siemens.Solid.Edge.ST.v100.0.Retail.x64.GERMAN.MERRY.CHRISTMAS
2008-12-23 MAGMASOFT.V4.4
2008-12-23 SOFTWARE.CRADLE.SC.TETRA.V7
2008-12-22 PGI.Visual.Fortran.2008.v8.0.2
2008-12-21 Right.Hemisphere.Deep.Exploration.CAD.Edition.v5.7.0.4228
2008-12-19 Shop.Talk.CAD.CAM.v8.0
2008-12-19 GibbsCAM.2009.V9.0.6
2008-12-18 Bentley.MicroStation.V8i.XM.v8.11.05.17
2008-12-17 3DVia.Composer.v2009x.WiNNT2K.RTFM
2008-12-16 Compusoft.Winner.v8.0a1.MULTILANG
2008-12-15 Strata_3D_CX_v5.6
2008-12-14 AUTODESK_LUSTRE_V2009
2008-12-14 Autodesk.Stitcher.Unlimited.2009.Build61.x86
2008-12-13 CIMCO.Software.Suite.v5.12.28
2008-12-12 Cedrat.Flux.v10.2.WiNNT2K
2008-12-11 Dassault.Systemes.3DVIA.Composer.v6R2009
2008-12-09 Tecplot.RS.2009.v11.3.29.1445
2008-12-08 CD-adapco.Star-CCM.Plus.and.Cad.Series.v3.06.Windows&Linux
2008-12-07 Embarcadero.ERStudio.v8.0.0.5865
2008-12-07 MicroSurvey.CAD.2009.Premium
2008-12-06 Hampson.Russell.CE8.R3.1
2008-12-06 Accelrys.Discovery.Studio.v2.1.Windows
2008-12-05 Siemens.Tecnomatix.v8.2
2008-12-04 Mastercam_X3_MU1
2008-12-03 AVL_FIRE_V8.5 FOR WINDOWS
2008-12-02 Klocwork.Insight.v8.0.7.1
2008-12-02 GIBBSCAM.2009.V9.0.5
2008-12-01 Delcam_Powershape_v8008
2008-12-01 AUTODESK.MOTIONBUILDER.V2009
FORM CAXSOFT
Subscribe to:
Posts (Atom)