2011-12-15
Magmasoft-5.1-Tutorial
Aachen, October 2010. MAGMA GmbH introduces with MAGMA5 a new generation of casting process simulation. MAGMA5 continues the series of MAGMASOFT® solutions used by foundries world-wide in order to optimize their cast component production. The software is based on more than 20 years of development, during which the Aachen based company has continued to innovate on and establish casting process simulation as a standard.
„First understand, then optimize“: following this standard, MAGMA5 delivers a profound understanding of casting processes that allows optimization along the complete process chain of the cast component. Within the software, this is made possible through different perspectives which can be used simultaneously by the user.
Integrated information and tools for simulation projects
In MAGMA5, all steps that are necessary for casting process simulation can be specified and performed from a process perspective. This allows the complete production process from geometry input, through the design of gating, risering and tooling, on to solidification and finishing processes such as heat treatment, to be described and simulated.
In the process perspective, all information about the used materials, metallurgy and melting practice, production conditions and finishing processes such as heat treatment come together. This allows the user to get a complete overview of the entire manufacturing process he wants to simulate.
Altogether, the process orientation of MAGMA5 sets the basis for a profitable manufacture of cast components – through improved casting layouts, achieving the required casting quality, and saving costs.
New simulation capabilities
MAGMA5 provides important new casting process simulation capabilities. New advanced turbulence models as well as the consideration of surface tension improve the mold filling prediction for gravity castings. And, tracer particles can be modeled with mass and size to evaluate slag inclusions. Burn-on and penetration criteria help identify sand related surface defects. Moreover, a new module for the simulation of as-cast local microstructures and properties of aluminum alloys is available with MAGMAnonferrous. The stress module MAGMAstress has also been completely reworked and for the first time offers the option to simulate thermally induced casting stresses for the complete manufacturing route. A new and comprehensive plasticity model provides improved accuracy, because it considers temperature-dependent as well as time-dependent effects on stresses and strains.
Clearly presented results
Simulation results such as 3D graphics, diagrams, and tables can be shown in multiple views and can be displayed in selectable levels of detail. This means that results can be evaluated reliably in order to allow an optimization of cast components and casting processes.
New software architecture secures future developments
The new methodology that MAGMA5 provides is mirrored in the software architecture. Technically, the software is built on a completely new platform and, as it is also modularly extendable and scalable, it offers development potential for the coming years. Due to standard interfaces that allow the free import and export of data, MAGMA5 can be completely integrated into the user’s work environment.
With MAGMA5, new hardware and operating systems offer new opportunities. MAGMA5 is fully native Windows compliant and runs on 64-bit Windows operating systems, offering the advantage of greatly increased memory access. For Linux users, MAGMA5 is available for the current SUSE and RedHat Linux Enterprise distributions. MAGMA5 supports multi-core architectures effectively. The combination of MAGMA5 and the latest hardware (Core i7/Neharlem CPU) results in a reduction of simulation times by up to a factor of 5.
With the currently released MAGMA5 Version 5.0 all important sand casting processes are supported. The simulation of permanent mold and die casting processes including gravity die casting is available with MAGMA5 Version 5.1.
MAGMA5 in a compact overview:
Comprehensive project management
Solid modeling with a CAD kernel as well as import and export of CAD data (STL, STEP, CATIA, Pro/E)
Automatic mesh generation of the geometry within seconds
Comprehensive process description with direct access to all process steps and the related simulation definitions
Completely new capabilities for the prediction of: mold filling, burn-on and penetration, local microstructures and properties of aluminum alloys, thermal stresses of the cast component for all production steps
Interactive and automatic result evaluation
Comprehensive database for all required data and properties of casting processes and materials
Available for 64-Bit Windows XP, 64-Bit Windows 7, 64-Bit RedHat Enterprise Linux 5, 64-Bit SUSE Linux Enterprise 11
2011-12-09
SPT-Group-OLGA-V7.1-DOWNLOAD
Version 7.1
The release includes new and enhanced features and functionalities for well modelling and risk management and optimisation projects.
World-wide, release - October 24th, 2011
Headlines:
Enhanced Well GUI and ESP/GLV in the Wells module:
- well modelling got easier and ESP’s and GLV’s can be selected from libraries
ROCX – transient near wellbore reservoir simulator:
- commercialization of the ROCX JIP for near wellbore reservoir transients coupled with OLGA
Risk Management and Optimisation:
- New module to tune complex models, manage risk and optimise production
Other improvements:
- FEMtherm, electrical heating and cooling in shapes
Produktbanner
Flow Assurance
OLGA is used in feasibility studies, conceptual studies, FEED and detailed designs and is essential for defining operating procedures and control schemes.
Application examples:
Transient thermohydraulics during start-up/shut-in
Optimal design for maximum operating envelope
Process and control system design
Flow assurance, investigating hydrates, wax, asphaltenes, corrosion, emulsions, scale and sand
Liquid inventory during pigging and rate changes
Slug mitigation and control
Fluid systems that can be modeled:
Oil and natural gas flowlines
Wet gas and condensate flowlines
Wellstream fluids
Dense phase flowlines
Single phase gas or liquid flowlines
Laboratory experiments
from dwcrk.com
FEFLOW-v6.06-crack-tutorial
What is FEFLOW?
FEFLOW is a professional software package for modeling fluid flow and transport of dissolved constituents and/or heat transport processes in the subsurface.
FEFLOW contains pre- and post processing functionality and an efficient simulation engine. A user-friendly graphical interface provides easy access to the extensive modeling options.
FEFLOW is a completely integrated system from simulation engine to graphical user interface. It also includes a public programming interface for user code.
Application Examples
FEFLOW is suitable for numerous different applications in flow and transport processes simulation in porous media, ranging from lab scale to continental scale. A few typical examples are listed here:
Groundwater Management
Geothermal Energy (Deep and Near-Surface)
Mine Water Management
Geotechnical Applications
Industrial Porous Media Design
Survey of Saltwater Intrusion
Study of Pollutant Dispersion
Coupled Groundwater/Surface-Water Simulation (Linkage with DHI MIKE11)
Flexible mesh generators
Finite-element discretization allows to use complex unstructured meshes that closely match natural structures while obeying requirements such as element size, element angles, etc. For large modeling areas, generation is supported by sophisticated automation algorithms to ensure efficient work. Automatically generated meshes also have to be adapted to internal geographical structures, like rivers or well locations.
As any single mesh generation approach cannot be expected to perform optimally under all conditions, FEFLOW offers a number of different mesh-generation algorithms and different options of user influence on the generation process.
Parallel computing
Transient calculations of complex regional models for long time periods require significant computational effort. Long simulation times can occur, even using the latest hardware available. Parallel processing allows a significant reduction in CPU times on multiple-processor platforms. In FEFLOW tasks of parallel structure as matrix assembly are processed in parallel on the different CPUs.
Finite-element method
Spatial discretization of the study area is a prerequisite for any numerical modeling. Classic groundwater simulation codes use finite difference discretization. In contrast, FEFLOW is based on the finite-element technique.
Major advantages of finite-element modeling include:
Unstructured meshing, thus much better representation of features like rivers, fractures, well locations by adaptation of the mesh
Better representation of sloping layers and anisotropy
Local mesh refinement without having to refine the whole column/row
Moving meshes for free-surface calculations
Automatic mesh refinement and coarsening
Less computational effort due to reduced element numbers for large regional models
Broad range of small-scale and large-scale applications
GIS/CAD interface
In most practical applications, the basic spatial data are available either in GIS (e.g., ESRI formats) file format or in a CAD-like format (e.g., AutoCAD exchange format). Direct import of these data formats helps to avoid intermediate conversion routines for transferring the basic data to the groundwater model. In the post processing step, data are easily transferred back to the GIS or CAD system to provide the results in data formats compliant to the project framework. FEFLOW can handle GIS as well as CAD data for import and export at all stages of modeling, e.g., to provide geographical input for mesh generation, parameter distribution, etc. Where appropriate, different regionalization methods are provided to transfer the basic data to the finite elements or mesh nodes. Using GIS files, attribute data can be directly transferred to the groundwater model. Alternatively, all data input can be performed manually or by importing ASCII files.
Up-to-date visualization tools
The days of presenting modeling results in large tables of figures are long gone. Today’s customers expect elaborate isoline maps, pathline diagrams, cross-sectional and 3D views and animations, which can also be used to present complex hydrogeologic conditions to the public.
FEFLOW addresses that need by its planar, cross-sectional and 3D visualization features.
Using FEFLOW three-dimensional visualizations of all model parameters and modeling results (like movements of contaminant plumes, etc.) can be produced.
2011-12-07
COADE-PVElite-V2011
PV Elite 2011 Main Features:
Modeling of ASME VIII-1 Jacketed Vessels
What this feature does - Delivers an integrated approach leveraging the 3D model and calculations in the modeling of jacketed vessels (ASME App. 9) and vapor/distribution belts.
How this feature used - Jackets or vapor belts can be added as details on cylindrical elements. Jackets can also span across element boundaries.
How this feature benefits you - Previously you would have to model the inner core vessel and the jacket sections as separate PV Elite models and then manually transfer the parameters between them. The same holds true for nozzles on the outer jacket and also the inner shell.
The old approach meant that results would reside in two or more places, meaning that reports would have to be manually combined. Moreover, you would have to apply correction factors to get correct combined wind and seismic loads. Another option would be to model the jacket/vapor belt in CodeCalc™, but then these items will excluded from any wind/seismic/support, and other calculations.
Why this is better than the old way of doing things
For starters it’s easier and quicker. With all the data in one model, there is less chance of errors from multiple inputs plus PV Elite automatically accounts for important interactions between the core vessel and jacket(s). The real-time 3D model, with intuitive sectioning capabilities, allows the on-screen display of the inner vessel plus jacket(s), which is a great in visualizing tool.
Modeling Tubesheet as Simply Supported
What this feature does - This feature provides an alternative method for modeling the welded joint between the tubesheet and shell or the tubesheet and channel cylinders, which can have the effect of reducing stress thereby producing a more economical design.
How this feature used - It is one of the optimization options available in the tubesheet tab of Heat Exchanger dialog.
How this feature benefits you - The tubesheet to shell or tubesheet channel junction is place of high stress. This alternative, permitted by the ASME code, gives you the option to produce a more economical, but also safe, design.
Why this is better than the old way of doing things - This new capability’s potentially more economical design option was not previously available in PV Elite. This meant that, in some cases, exchanger designers were limited to more conservative analysis therefore leading to more costly designs.
ASME Code Updates.
What this feature does
This feature includes all the rule updates in the ASME code addenda and material updates. The Imperial tables were completely re-created and the Metric ASME material tables were added.
CMG-2011-CMG-Technologies-Lanncher
MG (Computer Modelling Group Ltd.) is a computer software engineering and consulting firm engaged in the development, sale and technology transfer of reservoir simulation software.
CMG began as a company known for its expertise in heavy oil, and expanded its expertise into all aspects of reservoir flow modelling. Over the past 32 years, CMG has remained focused on the development and delivery of reservoir simulation technologies that assist oil and gas companies to determine reservoir capacities and maximize potential recovery.
To this end, we are continually improving our market-leading line of reservoir simulation technologies to better reflect the changing needs of our users.
CMG is a world-class software company traded on the TSX Stock Exchange under the symbol CMG. With over 400 oil and gas companies and consulting firms in more than 50 countries, CMG is one of the largest independent providers of reservoir simulation software in the world.
CMOST is the latest product offering in the CMG software suite. It is a state-of-the-art reservoir engineering optimization tool, employing innovative experimental design, sampling and optimization techniques to efficiently determine the reservoir parameters which define the production and ultimate recovery of oil and gas fields.
CMG’s Builder creates the base-case reservoir model as the first step in the process.
CMOST generates simulation runs automatically from the base model, then submits and analyzes the runs that are created from a range of values for multiple reservoir parameters specified by the engineer.
CMOST learns which values produce the best results enabling it to dramatically reduce the number of runs required to find the optimal solution. This is the fastest technique for an accurate history match(es) and reliable production forecasts.
CMOST improves the effectiveness of each reservoir engineer by eliminating the tedious labor of individual case generation for hundreds of scenarios. It allows them to focus on the high value effort of interpretation and evaluation of results.
CMOST’s power lies in modern experimental design and optimization algorithms which vary multiple parameters simultaneously to find the optimal solution – something a human cannot do.
CMOST dispatches to a cluster of computers or a single computer and interprets the results of numerous runs, terminates non-physical solutions and narrows the search space rapidly to reach not just local maximums or minimums, but the ultimate best case. Solutions to reservoir models with trillions of possible combinations and permutations can often be found in fewer than 1000 runs.
CMOST helps engineers create more accurate models in dramatically less time and allows asset managers to have a greater degree of confidence in the forecasts, multiplying the team’s effectiveness many fold.
Pansystem-2011-download
PanSystem®
software has been the industry’s leading well-test analysis
program for more than 20 years. It is a robust yet easy-to-use software tool
that provides multiple options for models and analysis. These options include
industry standards as well as user-defned models for additional fexibility.
Ultimately, the PanSystem application provides a way to simplify complex
transient well testing through detailed analysis, simulation and reporting.
PanSystem software is dedicated to transient well testing, a key technical
function in the oil and gas industry. A pressure transient well test has the
unique capability to obtain information from within the reservoir surrounding
the well and, with appropriate testing and analysis techniques, can provide
a wealth of data:
• Permeability of the reservoir-at-large and, in some cases, the near-
wellbore region
• Completion effciency, effective open interval size (over the life of the well)
• Reservoir structure (boundaries, heterogeneities)
• Reservoir pressure
• Nature of any pressure support
• Drainage area, connected pore volume, and initial hydrocarbons in place
• Vertical permeability, vertical communication in layered systems
• Well performance (over the life of the well)
• Communication between wells
• Deliverability and production forecasts
Typical applications
© 2010-2011 Weatherford. All rights reserved.
PanSystem®
Well-Test Analysis Software
3
The task of designing, executing and analyzing a well test
depends on operating conditions as well as completion
and reservoir type. PanSystem software analyzes a wide
range of situations and asset types.
• Low-pressure reservoirs, heavy oil: Wellbore fll-up
and leak-off tests, steam-injection tests
• Pumping wells: Acoustically derived pressures and rates
• Medium oil reservoirs: Conventional drawdown and
buildup tests
• Gas wells: Conventional analysis using real gas
pseudo-pressure, turbulent skin analysis for high-rate
wells, and gas well deliverability by empirical (C-and-n)
and LIT methods. (In depletion scenarios, gas properties
are revised as reservoir pressure declines.)
• Volatile oil/condensate reservoirs: Conventional
analysis techniques or use of multiphase pseudo-
pressure to model phase behavior and its effect on
relative permeability (in particular, liquid dropout or gas
breakout around wellbore)
• Hydrothermal wells: Steam production, water injection
• Gas- and water-injection wells: Injection and falloff
tests, including multiregion analysis to enable mobile
phase changes and temperature effects
• Interference tests: Inter-well permeability and ΦCt
product from type-curve analysis and/or history
matching by simulation
• Multilayered reservoirs: Conventional analysis or
specialized testing technique (MLT) using selective
fowmeter data
• Varying rate tests: Rates measured on surface or with
a downhole fowmeter
• Permanent downhole (or surface) gauges: Special
pressure decline analysis (PDA) section to analyze
long-term pressure and rate records for hydrocarbons
in place; deconvolution to reveal nature of the reservoir
and boundary models otherwise obscured by rate
changes and shut-ins
• Wireline formation tests: Analysis of pre-test, pump-out,
mini-DST, and vertical interference tests using dual- and
packer-probe analytical models (including special LAS and
DPK format data import)
From large-scale reservoir characterization to monitoring
of individual well performance, PanSystem’s well-
test analysis provides information for many important
operational decisions.
• Workover: Completion effciency from skin factor and
early time derivative shape; open interval length for
stimulation or reperforation; fracture quality
• Reservoir characterization: Horizontal permeability (from
kh
); vertical permeability; boundaries and heterogeneities;
gas cap/aquifer support; pressure support from a second
compartment; layering for reservoir model refnement and
feld-development planning
• Reserves estimation: Extended production test; long-
term fowing pressure record (with permanent downhole
gauge); buildup testing for reservoir model refnement
and feld-development planning
• Production performance prediction: Single well
forward prediction with material balance included for
feld-development planning
• Reservoir pressure decline: for feld-developmen
Paradigm-2011-EPOS-V4.1
he Paradigm 2011 release is the largest synchronized release of exploration, development and production technology in the company’s history. A result of years of research and development, the release carries the signature of innovation that the industry has come to expect from Paradigm™, with new, game-changing technologies that redefine workflows and best practices across the E&P chain. The release also expands Window® 7 platform support to Paradigm’s full interpretation suite.
In addition to the introduction of a rich set of geoscience and engineering applications, this release enhances multi-disciplinary collaboration, enabled and strengthened by expanded data integration, an intuitive user interface, and a highly ergonomic design.
The release introduces measurable product performance with the expanded use of multi-core (CPU and GPU) applications for seismic imaging, seismic attribute calculations, voxel interpretation and subsurface modeling. Productivity is enhanced with integration improvements and new workflows, such as interpretation with modeling, and new knowledge control and auditability solutions for multi-scenario management.
Major technological advances in Paradigm 2011 include:
• New “validation of interpretation data while modeling” workflows using true 3D paleo-flattening
• Pre-stack and post-stack data in a common interpretation canvas
• Multi-attribute interpretation with multi-well correlations and multi-well synthetics
• Innovative multi-attribute volume, section and map blending
• On-the-fly time-to-depth corrections from multiple velocity sources over multiple surveys
• Crossplot and transparent traverse operations over multi-survey data
• New voxel rendering technology (GPU enabled) for 8X performance improvements
• New GPU-based modeling kernels for >6X performance
• Regional multi-line 2D seismic facies classifications
• Geologic and seismic interpretation views with production data
• True 3D restoration and basin modeling
• 3D model uncertainty capture
• Multi-point geostatistics and proportional facies
• Hybrid Windows and Linux deployment for all interpretation and modeling technologies
Mastrecam-x6-v15.0.3.28-crack
Mastercam X6 Release Highlights
View the "What's New in Mastercam X6" PDF file
View Mastercam archive videos
Detailed list of new additions since the release of Mastercam X
Mastercam X6 delivers full 64-bit support and a powerful set of new tools to help you make the most of your shop. We've listed some highlights below (click the video icon to see a quick demonstration):
Mill and Router:
The new in-process stock model delivers an accurate representation of your part as toolpaths are applied to it. The model can be verified and used as the basis for additional toolpaths. video
Enhanced dynamic milling includes finer control and additional time savings. video
Fast 2D HST region chaining dramatically speeds up dynamic toolpath programming. video
Smart rest roughing uses the new in-process stock model to create a highly efficient pass to remove stock remaining from a larger tool
Hybrid finish "filler" passes divide your part into a series of Z sections and applies two different machining strategies to each section for a superior finish.
Lathe:
Variable depth roughing for longer insert life. video
Easy pick, pull and cutoff operations. video
Remaining stock removal. video
Smart finishing that identifies and cuts flats and walls with different motion. video
Finish tool inspection. video
Enhanced canned rough and finish toolpaths.
New finish feed / speed facing and canned grooving controls.
Wire:
Enhanced autosyncing.
Improved wirepath editing.
New force wire taper to vertical options.
CAD Tools:
Finer control over intersecting and trimming solid edges.
Enhanced solid trim to surface.
Dynamic transform along a vector.
Blade Expert: video
With the release of Mastercam X6 , we're also introducing Mastercam Blade Expert, a new purchasable add-on designed for multi-bladed parts. This powerful tool can be added to Mastercam Mill Level 3 or Router Pro, and delivers:
Powerful programming for fans, propellers, impellers, turbines, marine screws and more.
Variety of efficient roughing strategies.
Precise curt pattern control on blade, fillet, and floor finishing.
Automatic tool axis control.
Full machine simulation.
2011-09-13
Agilent-Advanced-Design-System-(ADS)-2011-05-crack
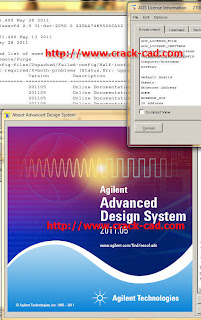
Advanced Design System is the leading electronic design automation software for RF, microwave, and high speed digital applications. ADS pioneers the most innovative and commercially successful technologies, such as X-parameters* and 3D EM simulators, used by leading companies in the wireless communication & networking and aerospace & defense industries. For WiMAX™, LTE, multi-gigabit per second data links, radar, & satellite applications, ADS provides full, standards-based design and verification with Wireless Libraries and circuit-system-EM co-simulation in an integrated platform.
Advanced Design System Key Features
Advanced Design System (ADS) continues to lead the RF EDA industry with the most innovative and commercially successful technologies, including Harmonic Balance, Circuit Envelope, Transient Convolution, Agilent Ptolemy, X-parameter*, Momentum and 3D EM simulators (including both FEM and FDTD solvers). With ADS’s Wireless Libraries and circuit-system-EM co-simulation technology, ADS provides full, standards-based design and verification within a single, integrated platform.
Key Features
* Complete schematic capture and layout environment
* Innovative and industry leading circuit and system simulators
* Direct, native access to 3D planar and full 3D EM field solvers
* Largest number of process design kits (PDKs) developed and maintained by leading foundry and industry partners
* EDA and Design Flow Integration with companies such as Cadence, Mentor, and Zuken
* Optimization Cockpit for real-time feedback and control when using any of 12 powerful optimizers
* X-parameter model generation from circuit schematic and Agilent's NVNA for nonlinear high-frequency design
* Up-to-date Wireless Libraries enable design and verification of the latest emerging wireless standards
Lumerical-FDTD-Solutions-7.5-download
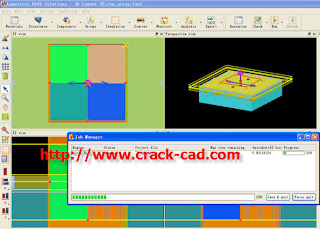
Vancouver, British Columbia January 13th, 2011 - Lumerical Solutions, Inc. a global provider of nanophotonic design software, today announced the immediate release of FDTD Solutions 7.5. This release features a concurrent computing capability which allows users to easily distribute simulations on multiple independent computer resources. Together with Lumerical's well established capabilities for distributed computation on high-performance computing clusters, FDTD Solutions 7.5 offers dramatic speed improvements when used on multiple desktops and workstations within traditional computer networks.
"FDTD Solutions 7.5 allows end-users to optimally achieve design goals on modern computing hardware," according to Dr. James Pond, Lumerical's CTO. "This release completes a multi-year mission to get individual computers simulating as fast as possible, and then to send those simulations to all available computers conveniently from your workstation. The time required to find an optimal design can easily be reduced by a factor of ten or more using the computers found in most offices or labs
2011-09-12
Kingdom_SMT_V8.6_download
What’s New In KINGDOM 8.6
The latest release of KINGDOM offers 27 new capabilities for customers. New capabilities range across 2d3dPAK, EarthPAK, VuPAK, VelPAK, and some capabilities applicable KINGDOM-wide. Shown below are two of the largest enhancements. Click Read More below to see all the new features.
Re-Engineered KINGDOM Fault Surface Modeling
The New Fault System is a complete redesign of the original fault system to provide a more accurate interpretation with new tools to modify fault surfaces.
* A new triangulation engine provides better fault surfaces.
* Fault smoothing using flex grid technology smooths one or all fault surfaces.
* Fault polygons are created using the exact line of intersection between the fault and the horizon or grid.
Microseismic Analysis in VuPAK Advanced
* Integrates seismic data interpretation with microseismic events
* Displays the events in any 2D or 3D window in time or depth
* Filters the data by any attribute with results seen in all views
* Includes easy tools to lasso or digitize desired subsets in any view in order to cut or crop points
* Provides dynamic visualization of microseismic events by any attribute as applied to color, size, and visibility
* Dynamically updates with user manipulation of microseismic events
* Generates a better understanding of reservoir response to well treatments
* Brings microseismic evaluation to the interpreter's desktop
* Provides a cost effective way to evaluate microseismic and treatment data
The latest release of KINGDOM offers 27 new capabilities for customers. New capabilities range across 2d3dPAK, EarthPAK, VuPAK, VelPAK, and some capabilities applicable KINGDOM-wide. Shown below are two of the largest enhancements. Click Read More below to see all the new features.
Re-Engineered KINGDOM Fault Surface Modeling
The New Fault System is a complete redesign of the original fault system to provide a more accurate interpretation with new tools to modify fault surfaces.
* A new triangulation engine provides better fault surfaces.
* Fault smoothing using flex grid technology smooths one or all fault surfaces.
* Fault polygons are created using the exact line of intersection between the fault and the horizon or grid.
Microseismic Analysis in VuPAK Advanced
* Integrates seismic data interpretation with microseismic events
* Displays the events in any 2D or 3D window in time or depth
* Filters the data by any attribute with results seen in all views
* Includes easy tools to lasso or digitize desired subsets in any view in order to cut or crop points
* Provides dynamic visualization of microseismic events by any attribute as applied to color, size, and visibility
* Dynamically updates with user manipulation of microseismic events
* Generates a better understanding of reservoir response to well treatments
* Brings microseismic evaluation to the interpreter's desktop
* Provides a cost effective way to evaluate microseismic and treatment data
2011-09-09
CGTECH-VERICUT-v7,14-download
Verification Simulate, verify, and analyze three axis milling, drilling, turning, mill/turn, and wire EDM tool paths.
Machine Simulation Build and simulate CNC machines and controls to check for collisions.
OptiPath Modify feed rates to make tool paths faster & more efficient.
Model Export Export an "as-machined" model in IGES or STL format.
Multi-Axis Simulate & verify four and five axis milling, drilling, turning, and combination mill/turn operations. Also supports simulation of synchronized and “pinch” turning operations where multiple channels/turrets are utilized.
CNC Machine Probing Create probing sequences at any stage in the machining process. Reduce the potential for error by simulating probing operations and save money on probing equipment.
Inspection Sequence
Save time and improve accuracy by generating in-process inspection instructions and documentation from VERICUT’s simulated in-process machined features! (Included with the base Verification product.)
VERICUT Reviewer
The ultimate shop floor communication tool! Get all the functionality of NC Review mode in a stand-alone viewer that does not use a license. (Included with the base Verification product.)
EDM Die Sinking Accurately simulate and verify EDM die sinking operations. Detect gouges, over/under burn, volume of material removed, contact area and electrode overlap. Supports multiple electrodes. (Included with the base Verification product.)
AUTO-DIFF Detect differences between design model & VERICUT part. Perform constant gouge-checking.
Cutter / Grinder Verification Verify multi-axis grinding operations. Features a simplified interface specifically for grinding.
Cutter / Grinder Machine Simulation Simulate multi-axis cutter/grinder machining operations and check for collisions.
CAD/CAM Interfaces Make verifying tool paths from within your CAD/CAM system easy and convenient.
Model Interfaces Read designated model file formats and use them as stock, fixture, design, tool holder and machine models. When combined with Model Export, VERICUT’s cut stock may be written out in these formats as well.
Machine Simulation Build and simulate CNC machines and controls to check for collisions.
OptiPath Modify feed rates to make tool paths faster & more efficient.
Model Export Export an "as-machined" model in IGES or STL format.
Multi-Axis Simulate & verify four and five axis milling, drilling, turning, and combination mill/turn operations. Also supports simulation of synchronized and “pinch” turning operations where multiple channels/turrets are utilized.
CNC Machine Probing Create probing sequences at any stage in the machining process. Reduce the potential for error by simulating probing operations and save money on probing equipment.
Inspection Sequence
Save time and improve accuracy by generating in-process inspection instructions and documentation from VERICUT’s simulated in-process machined features! (Included with the base Verification product.)
VERICUT Reviewer
The ultimate shop floor communication tool! Get all the functionality of NC Review mode in a stand-alone viewer that does not use a license. (Included with the base Verification product.)
EDM Die Sinking Accurately simulate and verify EDM die sinking operations. Detect gouges, over/under burn, volume of material removed, contact area and electrode overlap. Supports multiple electrodes. (Included with the base Verification product.)
AUTO-DIFF Detect differences between design model & VERICUT part. Perform constant gouge-checking.
Cutter / Grinder Verification Verify multi-axis grinding operations. Features a simplified interface specifically for grinding.
Cutter / Grinder Machine Simulation Simulate multi-axis cutter/grinder machining operations and check for collisions.
CAD/CAM Interfaces Make verifying tool paths from within your CAD/CAM system easy and convenient.
Model Interfaces Read designated model file formats and use them as stock, fixture, design, tool holder and machine models. When combined with Model Export, VERICUT’s cut stock may be written out in these formats as well.
SPT_Group_OLGA_7.0_download
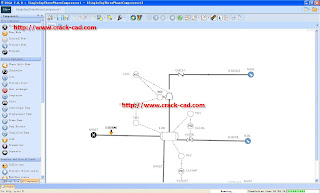
This minor release contains important bug fixes for e.g. OPC server and Wells GUI.
The most important fixes in OLGA 7.0.1 are:
* Problem with LoadSnap solved in OPC server
* Consistency in results when running cases with wells interactively, in batch or with OPC server
* Improved handling of illegal input data in OPC server
* Bug when starting simulations from the Wells GUI after updates fixed
* Bug in the distributed reservoir inflows option in the Wells GUI fixed
* Default units are included in the .genkey file (as in OLGA 6)
* Problem with ENDCONTROLLER solved
* Improvements in the documentation
LGA 7.0.1 Download
Version 7
OLGA 7.0 comes with a graphical user interface (GUI) which provides new look and feel features, a new diagram view and 3D visualization. Further, two new modules are available in OLGA 7.0. The OLGA HD Stratified Flow Model is a simplified 3D model for three phase stratified flow, and the Plug-In module is a framework for interfacing user-defined models.
Highlights in this release includes:
• Easy to use interface and workflows
• OLGA High Definition model for stratified flow
• Open framework for easy integration
Ucam_v9.2_110821_crack_for_win64_win32
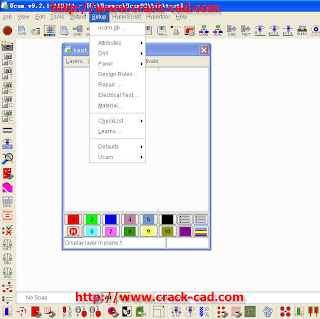
Ucam 9.2.1 fix
Enhancements (2 topics)
Table of Contents
CAD Output
Input
CAD Output
ODB++
BB02825 - ODB++ output can now create different sub-steps, if the original data contains nested blocks on which the uPCB attribute has been allocated. Previously only 1 sub-step was created.
Input
GAR
BB02907 - GAR now allows converting 0-sized aperture definitions. Previously these lines were ignored, while creating a wheel file, which could result in UNDefined apertures.
Contours
BB02677 - Split contours could not support regions containing small inner contours for which the size of the inner contour is in the range of the requested minimum overlap value. A message "Requested overlap is too high" was displayed and the region was not split. These small inner contours are not longer disturbing the Split contour function.
Shave
B357991 - Pad Shave function allows specifying if the shaving should be done between the different "regions" of a complex aperture. By default the shaving is applied between the regions of a complex aperture.
Soldermask
B358068 - The Soldermask Optimizer menu has been extended with an toggle for each section, allowing indicating which kind of optimizations should be applied.
Electrical Test
AutoFixture
B358150 - AutoFixture is supported by 64-bit workstations.
Utest
BB02800 - Introduction of new ucam.db key, testpoint.use.uplated_attr, for allowing ignoring the uPlated aperture and object attribute, stored on the drill layer(s), during test point generation. By default these uPlated attributes will be considered, but if needed, these attributes can be ignored.
General
User Interface
BB02807 - Introduction of new ucam.db keys, pos.cad.formats, pos.netlist.formats and pos.scoring.formats, for allowing influencing the order in which the different output languages are displayed in the output menus.
Input
Gerber
BB02766 - Introduction of new ucam.db key, gerber.evaluate.interpolation.mode, for allowing evaluating the applied circular interpolation mode while loading a Gerber file, in case the Gerber file is not clearly indicating which interpolation mode should be used.. When configuring gerber.evaluate.interpolation.mode: 1 and gerber.interpolation.mode with value G74 or G75 the conversion of the Gerber file can still use the best suitable interpolation mode, in case the conversion with the configured value for gerber.interpolation.mode would indicate problems with some arcs.
BB02815 - Introduction of a new ucam.db key, gerber.274d.jp, for influencing the conversion of flashes (D03 command) of standard Gerber files (RS-274D). Standard Gerber files in Japanese style should not use the model flash command, so only add a flash when the D03* command is explicitly specified. This key is also reflected in the SmartStart Options list, as "JP Style" option, for Gerber files.
Import ODB++
BB02774 - Compressed feature files (features.Z) are now decompressed in a temporary directory to avoid problems with read only containers.
B358354 - ODB++ Import is now only loading the symbol definitions that are required during the conversion of the loaded layers. Previously all symbol definitions, available in the ODB++ job, were converted; this could delay the import of the ODB++ data.
BB02758 - During ODB++ Import the regions containing inner contours can be grouped in a global contour aperture definition (reducing the amount of aperture definitions), when the image is not influenced. Previously each region, containing inner contours, was always using a dedicated contour aperture definition.
IPC-D-356
B358989 - Loading an IPC-D-356 file for being used as netlist references (load from SmartStart and with ipc356.exclude.drills: 1), using the new input algorithm (ipcmet.new_input_algorithm: 1) was missing some references, in case the loaded file was not fully according to the syntax description, e.g. when columns 18-20 are containing characters, although the syntax description indicates that these columns should remain empty). These lines, containing the unexpected characters, were notified to the operator. These lines are still notified but the resulting reference layers are containing the references for these lines.
Top
Job Editor
Layers
BB02843 - Clicking on the right mouse button can be used for hiding a layer.
Top
Job Management
Open Job
BB02861 - Introduction of a new ucam.db key, openjobinrunningucam, for indicating if Job Open, by double clicking on the .job file, should be done in the currently open UCAM session or if a new UCAM session should be started.
Top
Netlist Output
MNF2
BB02846 - Netlist output, of stepped data, was limited to 1022 Multiups. This has been extended to the limitation of the output file (e.g. 9999 for IPD-D-356B), on unlimited if the generated file is not having a limitation (e.g. MNF2).
Top
Verification
Design Rules
BB02770 - In case SmartDRC is not finding any violation, the warning message (indicating "drc found no errors") is now displayed in front of the SmartDRC window.
B358760 - Introduction of a new ucam.db key, drc.lsns_con, for influencing the algorithm that will be used while verifying the Same Net Spacing of Design Rule Check. Normally Same Net Spacing is running on the image (contourized image), configuring drc.lsns_con allows running the function on the way the image is constructed (by running some checks between objects of the same net).
2011-09-08
SimSci-Esscor_PRO/II_V9.1_download
PRO/II 9.1® process simulation software is a steady-state simulator enabling improved process design and operational analysis. It is designed to perform rigorous mass and energy balance calculations for a wide range of chemical processes.
Spanning oil & gas separation to reactive distillation, PRO/II offers the chemical, petroleum, natural gas, solids processing and polymer industries the most comprehensive process simulation solution available today.
Key Benefits
* Rigorously evaluate process improvements before committing to costly capital projects
* Improve plant yields through the optimization of existing plant processes
* Cost effectively assess, document and comply with environmental requirements
* Accelerate process troubleshooting
* Detect and remedy process bottlenecks
Key Capabilities
* Refining applications: heavy oil processing, crude preheating, crude distillation, FCC main and coker fractionator, naphtha splitter and stripper, sour water stripper, sulfuric and HF acid alkylation
* Oil & Gas Processing applications: amine sweetening, cascade refrigeration, compressor trains, deethanizar, demethanizer, gas dehydration, hydrate formation/inhibition
* Chemicals/Petrochemical applications: ethylene fractionation, C3 splitting, aromatic separation, cyclohexanes, MTBE separation, naphthalene recovery, olefin and oxygenate production and propylene chlorination
* Chemical applications: ammonia synthesis, azeotropic distillation, biofuels, crystallation, dehydration, electrolytes, inorganics, liquid-liquid extraction, phenol distillation, solids handling
* Polymer applications: free radical polymerization, step-growth polymerization, copolymers
* Pharmaceutical applications: batch distillation & reaction
Spanning oil & gas separation to reactive distillation, PRO/II offers the chemical, petroleum, natural gas, solids processing and polymer industries the most comprehensive process simulation solution available today.
Key Benefits
* Rigorously evaluate process improvements before committing to costly capital projects
* Improve plant yields through the optimization of existing plant processes
* Cost effectively assess, document and comply with environmental requirements
* Accelerate process troubleshooting
* Detect and remedy process bottlenecks
Key Capabilities
* Refining applications: heavy oil processing, crude preheating, crude distillation, FCC main and coker fractionator, naphtha splitter and stripper, sour water stripper, sulfuric and HF acid alkylation
* Oil & Gas Processing applications: amine sweetening, cascade refrigeration, compressor trains, deethanizar, demethanizer, gas dehydration, hydrate formation/inhibition
* Chemicals/Petrochemical applications: ethylene fractionation, C3 splitting, aromatic separation, cyclohexanes, MTBE separation, naphthalene recovery, olefin and oxygenate production and propylene chlorination
* Chemical applications: ammonia synthesis, azeotropic distillation, biofuels, crystallation, dehydration, electrolytes, inorganics, liquid-liquid extraction, phenol distillation, solids handling
* Polymer applications: free radical polymerization, step-growth polymerization, copolymers
* Pharmaceutical applications: batch distillation & reaction
Metrolog_XG_V13_download
Datapixel Optiscan HR laser line scanner Integration
While integrating the new OptiScan HR in Metrolog XG13: we also made some improvements enabling the acquisition and analysis of a higher density of points.
Now supporting the all new laser tracker made by Leica: AT 401 (3D)
Our Leica partnership is stronger than ever: we will support the latest laser tracker AT 401. Leica and Metrologic teams have worked extremely closely together to completely optimize the new device integration with Metrolog XG13.
Integration of the Romer RDS V3.0.0 driver including 3rd button support
The latest RDS driver is part of Metrolog XG13 to support the latest evolution of Romer measuring arm. It will enable our users to use the 3rd button available in some Romer equipment.
New LK DCC Controller integrated with Metrolog XG13:
LK MicronDrive (Serial Liaison) - Touch trigger mode - 3 axis
LK Cupe (Serial Liaison) - Touch trigger mode - 4-axis for Gantry style drive
LK MCC-200 (TCP-IP Liaison) - Touch trigger mode - 3 axis
Some additional new features information will follow soon…
Metrologic Group keeps developing and improving its product line and services by integrating the latest technologies and offering its leading tools, experience and know-how to the 3D measuring industry.
As part of your software maintenance agreement, you will receive automatically the software updates as they become available.
Step ahead with our Advanced 3D measuring solutions!!!
While integrating the new OptiScan HR in Metrolog XG13: we also made some improvements enabling the acquisition and analysis of a higher density of points.
Now supporting the all new laser tracker made by Leica: AT 401 (3D)
Our Leica partnership is stronger than ever: we will support the latest laser tracker AT 401. Leica and Metrologic teams have worked extremely closely together to completely optimize the new device integration with Metrolog XG13.
Integration of the Romer RDS V3.0.0 driver including 3rd button support
The latest RDS driver is part of Metrolog XG13 to support the latest evolution of Romer measuring arm. It will enable our users to use the 3rd button available in some Romer equipment.
New LK DCC Controller integrated with Metrolog XG13:
LK MicronDrive (Serial Liaison) - Touch trigger mode - 3 axis
LK Cupe (Serial Liaison) - Touch trigger mode - 4-axis for Gantry style drive
LK MCC-200 (TCP-IP Liaison) - Touch trigger mode - 3 axis
Some additional new features information will follow soon…
Metrologic Group keeps developing and improving its product line and services by integrating the latest technologies and offering its leading tools, experience and know-how to the 3D measuring industry.
As part of your software maintenance agreement, you will receive automatically the software updates as they become available.
Step ahead with our Advanced 3D measuring solutions!!!
CimatronE_V10_download
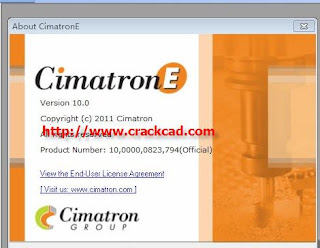
Cimatron develops and distributes CAD/CAM software for the manufacturing industry. With two major product lines, GibbsCAM and CimatronE, Cimatron caters to all manufacturing sectors, offering specialized solutions for mold and die makers, as well as solutions for 2.5-5 Axis production milling and turning.
Ranked among the top ten CAD/CAM suppliers in every global region, Cimatron has subsidiaries in Asia, North America and Europe, and works with certified independent service providers in over 40 countries worldwide.
imatronE 10 surpasses all previous versions, offering significantly faster mold design, die design and manufacturing capabilities, while increasing quality. Upgrading will impact overall delivery time, especially for full solution customers, and compress mold and die design, NC programming and machining times.
CAD enhancements provide stronger, more powerful capabilities, including a new built-in motion simulator, which specializes in tooling and provides an advanced analysis of kinematics. Die makers will enjoy an easier, more intuitive strip design process and greater automation for tool design. Mold designers will find new and unparalleled analysis capabilities for the parting line as well as shutoff and runoff surfaces, eliminating design flaws at a very early stage. There are also new applicative tools for lifter and insert creation.
CAM enhancements dramatically increase programming productivity, with background calculations and enhanced multi-core processing. Machining times are reduced, with significant upgrades to rough strategies, and there’s a new helical finishing strategy.
Beta tester Gary R. Zech, from D & F Mold, LLC., commented: “Background calculations are amazing! I don’t have to stop work and wait for a toolpath calculation while I’m in the middle of a job; I just keep working.”
The release of CimatronE 10 also introduces a new product, the patent pending CimatronE SuperBox. The SuperBox is a toolpath off-loading and processing acceleration device that dramatically shortens NC programming; it is reported to have saved users 85% off programming time.
AlphaCAM_V2011_R2_download
A general overview of the new features within Alphacam 2011 R2.
New Parallel and Flat Area 3D Machining Strategies
Mabel
Much improved Parallel and Flat Area 3D machining strategies for cutting solid models and surfaces provide reduced cutting time, improved surface finish and improved tool life.
* Automatic exclusion of flat areas on parts allowing for flat rather than ball ended cutters to be used.
* Steep and shallow areas of parts detected allowing for different strategies to be adopted, such as a smaller tool step-over in a steeper gradient to that used in a shallow area.
* Options to always down or up mill, and loop or round sharp external corners.
New Geometry Query Manager
Mabel
The Geometry Query Manager allows for a set of rules to be defined and applied to the current Alphacam drawing. Based on these rules, geometries are moved onto specifically named user layers. Machining Styles can then be applied to these layers automating the generation of tool paths. AutoStyles and CAD to CAM (add-in) have also been updated to take advantage of this new functionality, proving further automation improvements.
Adaptive Feed Rate Support for Z Contour Roughing
MabelThis new feature in Z Contour Roughing provides the ability to automatically adjust the tool’s feed rate throughout the tool path, taking into account the effective width of cut.
While machining a full width of cut, the feed rate can be automatically reduced to lessen the tool load. Conversely, while machining a narrower width of cut, the feed rate can be automatically increased to reduce machining time, without overloading the tool.
New Automatic Work Plane Ordering
Mabel
This new Order Work Planes command can be used to automatically optimize the order of geometries and tool paths. The shortest path around a 4 or 5-axis part is automatically calculated based on the CNC machine configuration.
This eliminates the time consuming process of manual ordering as well as reduces the rapid travel distances, resulting in faster machining time.
New Extract Solid Edge for Sawing
Mabel
This new Edge for Sawing command, added to Feature Extraction, creates special geometry from a selected solid model planar face. The resulting geometry is automatically configured for the correct tool side, orientation and depth of cut for Auto-Z sawing.
New Parallel and Flat Area 3D Machining Strategies
Mabel
Much improved Parallel and Flat Area 3D machining strategies for cutting solid models and surfaces provide reduced cutting time, improved surface finish and improved tool life.
* Automatic exclusion of flat areas on parts allowing for flat rather than ball ended cutters to be used.
* Steep and shallow areas of parts detected allowing for different strategies to be adopted, such as a smaller tool step-over in a steeper gradient to that used in a shallow area.
* Options to always down or up mill, and loop or round sharp external corners.
New Geometry Query Manager
Mabel
The Geometry Query Manager allows for a set of rules to be defined and applied to the current Alphacam drawing. Based on these rules, geometries are moved onto specifically named user layers. Machining Styles can then be applied to these layers automating the generation of tool paths. AutoStyles and CAD to CAM (add-in) have also been updated to take advantage of this new functionality, proving further automation improvements.
Adaptive Feed Rate Support for Z Contour Roughing
MabelThis new feature in Z Contour Roughing provides the ability to automatically adjust the tool’s feed rate throughout the tool path, taking into account the effective width of cut.
While machining a full width of cut, the feed rate can be automatically reduced to lessen the tool load. Conversely, while machining a narrower width of cut, the feed rate can be automatically increased to reduce machining time, without overloading the tool.
New Automatic Work Plane Ordering
Mabel
This new Order Work Planes command can be used to automatically optimize the order of geometries and tool paths. The shortest path around a 4 or 5-axis part is automatically calculated based on the CNC machine configuration.
This eliminates the time consuming process of manual ordering as well as reduces the rapid travel distances, resulting in faster machining time.
New Extract Solid Edge for Sawing
Mabel
This new Edge for Sawing command, added to Feature Extraction, creates special geometry from a selected solid model planar face. The resulting geometry is automatically configured for the correct tool side, orientation and depth of cut for Auto-Z sawing.
Optisworks_ 2011_for_solidworks 2010- 2011_key
OPTIS edits a range of software for the scientific simulation of light and human vision within a Virtual Reality Environment. Its solutions allow designers, ergonomists and engineers to simulate and optimize lighting performance, colors, optical effects, product lit appearance as well as the visibility and legibility of information on Human Machine Interfaces, in a fully-immersive CAD environment.
OPTIS is the only software editor of its kind to offer such a complete solution from optical design, to photometric optimization through to product visualisation all within one software, making it a truly corporate-wide solution.
The Science of light at your fingertips
OPTIS offers you a user friendly, highly intuitive simulation and visualisation tool harnessing the optics, light and human vision knowledge and experience that its team has gained over 20 years and 150 man years.
OptisWorks, Light & optical CAD Integrated software
Increase productivity, streamline your design process
OPTIS is the only company in the world to offer seamless integration of high-performance, physics based light and human vision simulation directly within SolidWorks®.
OPTIS delivers the only CAD integrated simulation solutions to provide a single virtual prototyping environment allowing optical and mechanical engineers to perform up-front analysis and product design optimization.
OPTIS is the only software editor of its kind to offer such a complete solution from optical design, to photometric optimization through to product visualisation all within one software, making it a truly corporate-wide solution.
The Science of light at your fingertips
OPTIS offers you a user friendly, highly intuitive simulation and visualisation tool harnessing the optics, light and human vision knowledge and experience that its team has gained over 20 years and 150 man years.
OptisWorks, Light & optical CAD Integrated software
Increase productivity, streamline your design process
OPTIS is the only company in the world to offer seamless integration of high-performance, physics based light and human vision simulation directly within SolidWorks®.
OPTIS delivers the only CAD integrated simulation solutions to provide a single virtual prototyping environment allowing optical and mechanical engineers to perform up-front analysis and product design optimization.
OPTIS-SPEOS-CAA-V5-Based-V10-key-crack-for win32&win64
World-leading light and human vision simulation solutions directly in CATIA V5
OPTIS edits a range of software for the scientific simulation of light and human vision within a Virtual Reality Environment. Its solutions allow designers, ergonomists and engineers to simulate and optimize lighting performance, colors, optical effects, product lit appearance as well as the visibility and legibility of information on Human Machine Interfaces, in a fully-immersive CAD environment.
OPTIS is the only software editor of its kind to offer such a complete solution from optical design, to photometric optimization through to product visualisation all within one software, making it a truly corporate-wide solution.
The Science of light at your fingertips
Web site:
OPTIS offers you a user friendly, highly intuitive simulation and visualisation tool harnessing the optics, light and human vision knowledge and experience that its team has gained over 20 years and 150 man years.
OPTIS edits a range of software for the scientific simulation of light and human vision within a Virtual Reality Environment. Its solutions allow designers, ergonomists and engineers to simulate and optimize lighting performance, colors, optical effects, product lit appearance as well as the visibility and legibility of information on Human Machine Interfaces, in a fully-immersive CAD environment.
OPTIS is the only software editor of its kind to offer such a complete solution from optical design, to photometric optimization through to product visualisation all within one software, making it a truly corporate-wide solution.
The Science of light at your fingertips
Web site:
OPTIS offers you a user friendly, highly intuitive simulation and visualisation tool harnessing the optics, light and human vision knowledge and experience that its team has gained over 20 years and 150 man years.
Roxar_IRAP_RMS_V2011_download_win32_win64
Emerson Process Management today announced the launch of Roxar RMS 2010, the latest release of the reservoir modeling system RMS™ which comes with major improvements across the entire workflow.
Within the Roxar modeling suite, users can build models for any reservoir. They can also estimate reserves, plan wells and simulate past and future production. In this way, they can do everything they need to produce maximum performance from their reservoirs, regardless of geology, location or complexity.
Benefits to users of RMS 2011 include:
? The ability to model beneath and around salt and other complex structures. RMS 2011 supports complex fault modelling that other applications can’t handle and incorporates these models into its advanced 3D gridding engine without simplification. Additional modelling functionalities that come with RMS 2011 include building intrusion objects into structural modelling to better model salt, and a new grid data structure for improved performance, scalability and more flexibility in the grid geometry.
? Enhanced facies modelling tools which will enable the user to rapidly combine the latest 4D seismic surveys into the models to improve the quality of interpretations, structural and property models, simulation models, and well plans. The model can also be the basis for a more quantitative use of 4D seismic data, especially towards history matching with both production data and 4D data.
? New well correlation tools with improved handling for horizontal and vertical well correlations which cross stratigraphic boundaries. RMS 2011 enables the user to split the horizontal well into separate sections so that well data can be inspected in the most practical manner possible, whether True Vertical Thickness (TVT) or True Stratigraphic Thickness (TST). In addition, advanced ghost curve capabilities can mix and match curves. Users can also examine array logs on top of one dimensional well logs, allowing for correlation to take place by taking into account seismic data as well as resistivity logs.
? Fractures are also fully integrated into the RMS 2011 reservoir modelling workflow through a DFN-based (Discrete Fracture Network) model which enables robust, fractured models to be built faster, providing an important tool in tackling the complex, fracture-prone geologies prevalent throughout the world.
? Improved usability and integration features which make RMS 2011 even more accessible and easier to use. Users are able to easily import large 2D or 3D surveys into RMS 2011 and enjoy an optimised working environment with updated data analysis charts, multiple and highly interactive visual displays and the best in graphics technology. For quality control purposes, the user can also produce all the necessary charts and maps to check consistency between the property models and the input data.
Within the Roxar modeling suite, users can build models for any reservoir. They can also estimate reserves, plan wells and simulate past and future production. In this way, they can do everything they need to produce maximum performance from their reservoirs, regardless of geology, location or complexity.
Benefits to users of RMS 2011 include:
? The ability to model beneath and around salt and other complex structures. RMS 2011 supports complex fault modelling that other applications can’t handle and incorporates these models into its advanced 3D gridding engine without simplification. Additional modelling functionalities that come with RMS 2011 include building intrusion objects into structural modelling to better model salt, and a new grid data structure for improved performance, scalability and more flexibility in the grid geometry.
? Enhanced facies modelling tools which will enable the user to rapidly combine the latest 4D seismic surveys into the models to improve the quality of interpretations, structural and property models, simulation models, and well plans. The model can also be the basis for a more quantitative use of 4D seismic data, especially towards history matching with both production data and 4D data.
? New well correlation tools with improved handling for horizontal and vertical well correlations which cross stratigraphic boundaries. RMS 2011 enables the user to split the horizontal well into separate sections so that well data can be inspected in the most practical manner possible, whether True Vertical Thickness (TVT) or True Stratigraphic Thickness (TST). In addition, advanced ghost curve capabilities can mix and match curves. Users can also examine array logs on top of one dimensional well logs, allowing for correlation to take place by taking into account seismic data as well as resistivity logs.
? Fractures are also fully integrated into the RMS 2011 reservoir modelling workflow through a DFN-based (Discrete Fracture Network) model which enables robust, fractured models to be built faster, providing an important tool in tackling the complex, fracture-prone geologies prevalent throughout the world.
? Improved usability and integration features which make RMS 2011 even more accessible and easier to use. Users are able to easily import large 2D or 3D surveys into RMS 2011 and enjoy an optimised working environment with updated data analysis charts, multiple and highly interactive visual displays and the best in graphics technology. For quality control purposes, the user can also produce all the necessary charts and maps to check consistency between the property models and the input data.
2011-08-09
Cadence IC Design Virtuoso 6.15
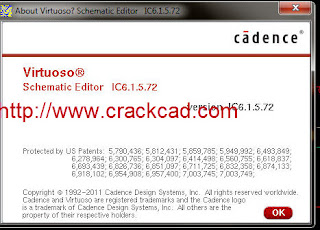
Circuit design
Selectively automating non-critical aspects of custom IC design allows engineers to focus on precision-crafting their designs. Cadence® circuit design solutions enable fast and accurate entry of design concepts—which includes managing design intent in a way that flows naturally in the schematic—coupled with an advanced design environment that allows designers to visualize and understand the many interdependencies of an analog, RF, or mixed-signal design and their effects on circuit performance.
Virtuoso Schematic Editor
Provides a complete design and constraint composition environment for front-to-back analog, custom-digital, RF, and mixed-signal designs.
2011-07-29
Mentor-Calibre-2011.2-download
Mentor's IC verification and sign-off includes not only traditional rule-based physical verification and parasitic extraction, but also new capabilities and automated technologies that help improve yield by enhancing the design itself.
Calibre® is the overwhelming market share leader and the industry standard for IC physical verification, due to the outstanding performance, accuracy and reliability of Calibre products. Over the last two years, Calibre nmDRC™ has reduced average DRC runtime by a factor of five, while Calibre's innovative Hyperscaling and MTFlex™ technologies have cut memory requirements in half. Calibre nmDRC also reduced overall cycle time with incremental DRC, which allows designers to make DRC runs in parallel. As DRC violations are reported, designers can immediately fix and recheck just the affected areas, while the initial DRC run continues.
To handle complex and multi-variate, multi-dimensional checks that are not adequately addressed by traditional design rules, Calibre nmDRC's equation-based DRC (eqDRC) capability enables designers to express design rule checks as continuous, multi-dimensional functions that accurately and precisely reflect underlying physical interactions. With eqDRC, designers can use Calibre nmDRC to address complex DFM issues that other DRC tools simply can't handle.
Calibre nmLVS provides actual device geometry measurement, programmable electrical rule checking, and sophisticated interactive debugging capabilities to ensure accurate circuit verification and further improve the designer's productivity.
Calibre® is the overwhelming market share leader and the industry standard for IC physical verification, due to the outstanding performance, accuracy and reliability of Calibre products. Over the last two years, Calibre nmDRC™ has reduced average DRC runtime by a factor of five, while Calibre's innovative Hyperscaling and MTFlex™ technologies have cut memory requirements in half. Calibre nmDRC also reduced overall cycle time with incremental DRC, which allows designers to make DRC runs in parallel. As DRC violations are reported, designers can immediately fix and recheck just the affected areas, while the initial DRC run continues.
To handle complex and multi-variate, multi-dimensional checks that are not adequately addressed by traditional design rules, Calibre nmDRC's equation-based DRC (eqDRC) capability enables designers to express design rule checks as continuous, multi-dimensional functions that accurately and precisely reflect underlying physical interactions. With eqDRC, designers can use Calibre nmDRC to address complex DFM issues that other DRC tools simply can't handle.
Calibre nmLVS provides actual device geometry measurement, programmable electrical rule checking, and sophisticated interactive debugging capabilities to ensure accurate circuit verification and further improve the designer's productivity.
Mentor-Graphics-PADS-V9.31
New Features
The following new features are available in this release:
Archive Navigator
This new utility provides a quick and easy method of automatically creating and restoring archives of the PADS projects, including DxDesigner® and PADS Layout.
Archives will be stored in a local vault and properties such as archive name, when and who created the archive, along with a user defined name and description will assist when using integrated searching capabilities to identify and restore the required archive.
Allegro to PADS Layout Import
PADS Layout can now import Cadence Allegro boards after initial preparation in Allegro. Once a Skill script is run in Allegro, the design can be brought seamlessly into PADS
Updated Altium Design to PADS Layout Import
PADS Layout import of Altium Designer now supports Summer 08 files (v7.1) and older.
Modeless Properties Dialogs in PADS Logic (Mentor Idea D113, D239)
Additional Property dialog boxes (Part, Net, Net Name, Bus, Bus Name, and Pin) are now modeless. These dialog boxes can now remain open, and you can select other objects in the design. When the object is selected, the dialog box will automatically update.
Join, Close and Break Commands for 2D Lines and Copper (Mentor Idea D329)
New commands were added to PADS Layout in the popup menu for selected 2D Lines and Copper shapes.
Join – creates an opened polyline (path) from selected lines.
Close – create closed shape (polygon) from selected lines.
Break – splits selected closed drawings into set of opened lines.
Note: There are several conditions when these commands cannot succeed – for example, the selection contains reuse members or shapes located on different layers or the command result is ambiguous from geometrical point of view. In such cases an appropriate message with details is displayed in the Status Window.
Synchronize Library List Between PADS Logic and PADS Layout (Mentor Idea D149)
A new checkbox “Synchronize with PADS Layout” was added to Library List dialog box in PADS Logic. A similar “Synchronize with PADS Logic” was added to Library List dialog in PADS Layout. When this checkbox is selected, all changes made to Library List in one application are immediately written to the other application’s settings. Library List settings are stored separately in .ini files for both applications as previously, so you can easily decide if and when you want to have them synchronized.
Autohatch Copper on File Load (Mentor Idea D424)
The new checkbox “Autohatch on file load” was added to “Hatch and Flood” options in PADS Layout. When this checkbox is selected every design is automatically hatched when opened. The result is the same as the Hatch All command from Pour Manager.
Options Dialog Box Redesign
The Options dialogs in PADS Layout, Logic and Router were redesigned to use trees instead of tabs. In PADS Layout and Router, the tree is organized in categories for better orientation and options grouping. Content of tabs which were overloaded in previous versions of PADS was divided into fewer elements on the new option tree.
Visual Style Selection in Customization
A new option, “Visual Style” was added to the Options tab in Customize dialog in PADS Layout, Logic and Router. This option allows the selection of a visual style (color and menus style) for the main application window from a list of several available styles.
PADS Applications Are Now DPI Aware
With increased text size in system settings, all fonts and dialog boxes are correctly scaled and displayed according to system settings.
The following new features are available in this release:
Archive Navigator
This new utility provides a quick and easy method of automatically creating and restoring archives of the PADS projects, including DxDesigner® and PADS Layout.
Archives will be stored in a local vault and properties such as archive name, when and who created the archive, along with a user defined name and description will assist when using integrated searching capabilities to identify and restore the required archive.
Allegro to PADS Layout Import
PADS Layout can now import Cadence Allegro boards after initial preparation in Allegro. Once a Skill script is run in Allegro, the design can be brought seamlessly into PADS
Updated Altium Design to PADS Layout Import
PADS Layout import of Altium Designer now supports Summer 08 files (v7.1) and older.
Modeless Properties Dialogs in PADS Logic (Mentor Idea D113, D239)
Additional Property dialog boxes (Part, Net, Net Name, Bus, Bus Name, and Pin) are now modeless. These dialog boxes can now remain open, and you can select other objects in the design. When the object is selected, the dialog box will automatically update.
Join, Close and Break Commands for 2D Lines and Copper (Mentor Idea D329)
New commands were added to PADS Layout in the popup menu for selected 2D Lines and Copper shapes.
Join – creates an opened polyline (path) from selected lines.
Close – create closed shape (polygon) from selected lines.
Break – splits selected closed drawings into set of opened lines.
Note: There are several conditions when these commands cannot succeed – for example, the selection contains reuse members or shapes located on different layers or the command result is ambiguous from geometrical point of view. In such cases an appropriate message with details is displayed in the Status Window.
Synchronize Library List Between PADS Logic and PADS Layout (Mentor Idea D149)
A new checkbox “Synchronize with PADS Layout” was added to Library List dialog box in PADS Logic. A similar “Synchronize with PADS Logic” was added to Library List dialog in PADS Layout. When this checkbox is selected, all changes made to Library List in one application are immediately written to the other application’s settings. Library List settings are stored separately in .ini files for both applications as previously, so you can easily decide if and when you want to have them synchronized.
Autohatch Copper on File Load (Mentor Idea D424)
The new checkbox “Autohatch on file load” was added to “Hatch and Flood” options in PADS Layout. When this checkbox is selected every design is automatically hatched when opened. The result is the same as the Hatch All command from Pour Manager.
Options Dialog Box Redesign
The Options dialogs in PADS Layout, Logic and Router were redesigned to use trees instead of tabs. In PADS Layout and Router, the tree is organized in categories for better orientation and options grouping. Content of tabs which were overloaded in previous versions of PADS was divided into fewer elements on the new option tree.
Visual Style Selection in Customization
A new option, “Visual Style” was added to the Options tab in Customize dialog in PADS Layout, Logic and Router. This option allows the selection of a visual style (color and menus style) for the main application window from a list of several available styles.
PADS Applications Are Now DPI Aware
With increased text size in system settings, all fonts and dialog boxes are correctly scaled and displayed according to system settings.
sap2000_v15
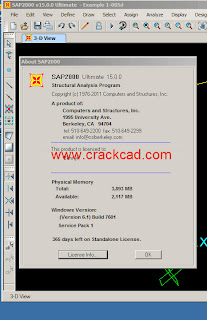
SAP2000 V15 Enhancements Subscribe RSS
New graphical user interface with tabbed windows.
New DirectX graphics.
Display and output of frame stresses.
Load optimization feature to determine the optimal loading scale factors to achieve goals and limits on displacement and force response throughout the structure.
Built-in European concrete and steel material properties.
Canadian NBCC loading for wind, seismic, and response-spectrum.
American ASCE-7 loading for wind, seismic, and response-spectrum.
Italian NTC 2008 response-spectrum functions with geographic database.
Indian steel frame design code IS 800 2008.
New Zealand steel frame design code NZS 3404-1997.
Canadian steel frame design code CSA S16-2009.
Updated Hong Kong concrete frame design code to include Supplement 1.
Australian concrete frame design code AS3600-2009.
Enhanced Eurocode 3-2005 steel frame design, including design for Class 4 sections.
National annexes for Eurocode 2-2004 concrete frame design for Singapore, Germany, and Portugal.
National annexes for Eurocode 3-2005 steel frame design for Singapore, Germany, and Portugal.
Hybrid steel frame section property.
Simple arc for tendon profile definition.
Updated API functionality.
Import of StruCAD*3D design parameters and wave acceleration loading.
Note that the Bridge module has been moved to the CSiBridge product with expanded features and capabilities. Basic moving-load analysis has been retained for non-bridge applications.
Other minor enhancements.
2011-06-17
CoventorWare-2010
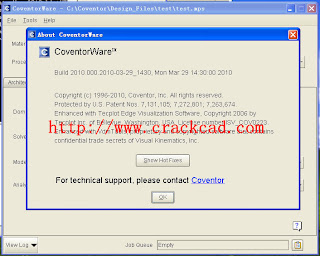
CoventorWare® for MEMS CAD Design,
Multiphysics Modeling and Simulation
CoventorWare 2010 Press Release
MEMS devices are increasing in complexity, as well as in the functionality they can deliver. Our CoventorWare platform has established itself as the leading design and simulation suite for all phases of MEMS design – from system level modeling to detailed 3D simulation and optimization, to manufacturing yield enhancement. With our 2010 release we have not only improved performance, but have added simulation capabilities that address rapidly emerging design requirements for exciting new MEMS-enabled applications.
The CoventorWare software suite is filled with MEMS-specific features that enable you to:
develop MEMS devices at a lower cost
become productive more quickly, focusing on your MEMS design instead of your software
efficiently design new MEMS products, moving them quickly from development into production
rapidly explore and optimize design and process options
adapt existing designs and processes to new markets
efficiently accommodate customer-requested design changes
save fab cycles during development and improve yield
SeisWare-7.02-download
What's new in SeisWare 7.2?
New log editor
New volumetrics calculator
Opacity in 3D visualizer
Overlay synthetic on seismic
Deviated synthetics follow well track
Trace correlation 3D autopicker
Scale bar on seismic section and plots
Licensing log file
Enhancements to SeisWare interpretation package
Crossplot
3D Visualizer
Basemap
PETRA integration via Data Pipeline
Well Import
And much more...
For a full detailed presentation on What's New in SeisWare 7.2, click here.
The new functionality and enhancements in this version build on an already strong foundation.
Fault interpretation
Spectral Decomposition
Semblance Calculator
SEG-Y calculator
Cross plotting
Seismic zone attributes
Interactive synthetics
2D and 3D auto pickers
Log signatures on the maps
Automatic mistie incorporates 2D/3D/synthetics and jump ties
PETRA(r) data import and export
Link to ESRI shapefile or SDE layer
Time to depth interval velocity method
Custom coordinate system
Cross correlation & advanced cross correlation (pseudo facies analysis)
Coordinate conversion utility
OpenSpirit link to access data from multiple vendors
Automatic mistie analysis
Grid and horizon paint brush smoother
Data pipeline - enhanced data transfer from various applications
Proportional time slices
OpenSpirit link now supports seismic data transfer
New log editor
New volumetrics calculator
Opacity in 3D visualizer
Overlay synthetic on seismic
Deviated synthetics follow well track
Trace correlation 3D autopicker
Scale bar on seismic section and plots
Licensing log file
Enhancements to SeisWare interpretation package
Crossplot
3D Visualizer
Basemap
PETRA integration via Data Pipeline
Well Import
And much more...
For a full detailed presentation on What's New in SeisWare 7.2, click here.
The new functionality and enhancements in this version build on an already strong foundation.
Fault interpretation
Spectral Decomposition
Semblance Calculator
SEG-Y calculator
Cross plotting
Seismic zone attributes
Interactive synthetics
2D and 3D auto pickers
Log signatures on the maps
Automatic mistie incorporates 2D/3D/synthetics and jump ties
PETRA(r) data import and export
Link to ESRI shapefile or SDE layer
Time to depth interval velocity method
Custom coordinate system
Cross correlation & advanced cross correlation (pseudo facies analysis)
Coordinate conversion utility
OpenSpirit link to access data from multiple vendors
Automatic mistie analysis
Grid and horizon paint brush smoother
Data pipeline - enhanced data transfer from various applications
Proportional time slices
OpenSpirit link now supports seismic data transfer
topsolid-2011-tutorial
TopSolid 2011: Integrated CAD/CAM At Its Best
TopSolid 2011 has been designed to specifically provide solutions for our customers needs. This new 2011 release offers new features for design and manufacturing in mechanical engineering, tool making and wood industry.
Outstanding design capabilities
TopSolid’Design is a fully integrated and associative CAD software enabling the operator to draft and design products more efficiently. Discover the principal improvements of the 7.5 version, among the many new functions this version has to offer.
Integrated CAM at its best
One of TopSolid’Cam’s greatest forces is its capacity to manage all machining processes thereby making it one of the only CAM solutions on the market which is able to machine all parts by offering the most suitable machining processes. TopSolid’Cam 2011 offers many new functions to enable companies to reduce machining times, increase product quality and reduce tool costs.
Integrated CAD/CAM for the Wood Industry
Thanks to its continual evolutions, TopSolid’Wood has become a leader in design and manufacturing software for the wood industry. TopSolid’Wood and TopSolid’WoodCam 2011 offer not only increased productivity in design and manufacturing but also eliminate all communication obstacles between research and manufacturing departments.
Excellent CAD/CAM for mold makers
A fully integrated CAD module, TopSolid’Mold is designed to meet the highly specialized needs of mold makers and tool & die specialists. TopSolid’Mold 2011 offers many new functions to complete the digital process chain for mold makers.
Excellent CAD/CAM for tool makers
In addition to incorporating all those functions standard to TopSolid, TopSolid’Progress enables the successful blanking of a sheet metal part and the design of the strip in half the time needed by a standard CAD software. Discover the principal improvements of the 2011 version, among the many new functions this version has to offer.
TopSolid 2011 has been designed to specifically provide solutions for our customers needs. This new 2011 release offers new features for design and manufacturing in mechanical engineering, tool making and wood industry.
Outstanding design capabilities
TopSolid’Design is a fully integrated and associative CAD software enabling the operator to draft and design products more efficiently. Discover the principal improvements of the 7.5 version, among the many new functions this version has to offer.
Integrated CAM at its best
One of TopSolid’Cam’s greatest forces is its capacity to manage all machining processes thereby making it one of the only CAM solutions on the market which is able to machine all parts by offering the most suitable machining processes. TopSolid’Cam 2011 offers many new functions to enable companies to reduce machining times, increase product quality and reduce tool costs.
Integrated CAD/CAM for the Wood Industry
Thanks to its continual evolutions, TopSolid’Wood has become a leader in design and manufacturing software for the wood industry. TopSolid’Wood and TopSolid’WoodCam 2011 offer not only increased productivity in design and manufacturing but also eliminate all communication obstacles between research and manufacturing departments.
Excellent CAD/CAM for mold makers
A fully integrated CAD module, TopSolid’Mold is designed to meet the highly specialized needs of mold makers and tool & die specialists. TopSolid’Mold 2011 offers many new functions to complete the digital process chain for mold makers.
Excellent CAD/CAM for tool makers
In addition to incorporating all those functions standard to TopSolid, TopSolid’Progress enables the successful blanking of a sheet metal part and the design of the strip in half the time needed by a standard CAD software. Discover the principal improvements of the 2011 version, among the many new functions this version has to offer.
CAESAR II 2010_V5.3
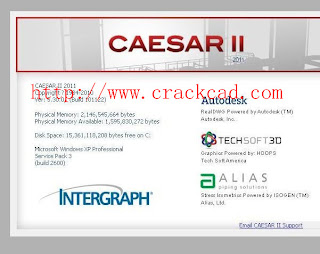
CAESAR II is the Pipe Stress Analysis standard against which all others are measured and compared. The CAESAR II spreadsheet input technique revolutionized the way piping models are built, modified, and verified. CAESAR II was the first pipe stress program specifically designed for the PC environment. The interactive capabilities permit rapid evaluation of both input and output, thereby melding seamlessly into the "design - analyze" iteration cycle.
CAESAR II incorporates a wide range of capabilities, from numerous piping codes, to expansion joint, valve & flange and structural data bases, to structural and buried pipe modeling, to equipment and vessel nozzle evaluation, to spectrum and time history analysis. Most of the features of CAESAR II are available at a keystroke, but at the same time are not imposed upon the analyst.
A menu driven scroll and select interface provides logical options when and where expected. Context sensitive help provides instant technical assistance for each data field, with expected units. Data values presented in the help screens are automatically presented in the current set of units to aid input.
The customization options of CAESAR II have been driven by user requests, code changes, and the need to benchmark older, existing systems and their initial design. Many of these customization options enable newer analysis techniques appearing in current literature.
As with all COADE products, CAESAR II is continuously maintained and improved by the engineering staff. The engineering staff of COADE have worked in industry, for engineering and consulting firms. This experience not only guides program development, but provides users with knowledgeable support. This allows CAESAR II to work the way a typical engineer thinks and solves a problem. This also means that the technical support provided to users by the engineering staff is almost instantaneous. Users talk straight to the developers, insuring an accurate and timely answer.
Program revisions incorporate additional capabilities addressing both technical and operational items. Users are encouraged to suggest improvements which help their day to day usage of the software. See the enhancement list for details of capabilities added for each release of the CAESAR II program.
Whether you are a one-man consulting company or a large corporation, if you are looking for a piping analysis program, CAESAR II is the best solution available - period.
Allegro PCB Edito 16.5
Allegro® PCB Editor: What's New in Release 16.5
Product Version 16.5 May 2011
Allegro PCB Editor: What's New in Release 16.5
Product Version 16.5
May 2011
This document describes new features in the current and previous releases of Allegro PCB Editor. Significant enhancements have
been made in the following areas:
Embedded Component Design
Graphical User Interface
Etch Edit Enhancements
Intelligent PDF Output
Associative Dimensioning
Design for Manufacturing
DRC Updates
ECAD-MCAD Flow
Database and Misc Enhancements
RF PCB Enhancements
To view the latest updates on hardware and software requirements, see the Allegro Platform System Requirements. Also refer to the
Migration Guide for Allegro Platform Products, Product Version 16.5.
Embedded Component Design
With increased market demands for smaller and lighter products, improved performance and higher speeds, it may become
necessary to consider the embedding of passive or even active components within the inner substrates of the PCB. If you are
designing product that essentially can be held in your hand, perhaps ones used in mobile applications or a consumer electronic
device like a digital camera, embedded component technology may be in your product roadmap plans. The methods on how
components are mounted and logically connected to the formation of cavities may differ from vendor to vendor. The Allegro Marketing
and R&D teams have done its best to provide a robust solution that can accommodate the vast options you may encounter in the
industry. As always, our best advice for advanced PCB Design whether that be HDI, Flex or Embedded is to work closely with your
Fabricator who may also own the Allegro tools. They can advise on the proper parameter and constraint settings that best
accommodate their process flow.
To support embedded components, following enhancements have been done in Allegro PCB Editor.
Licensing
Front to Back Flow Support
Setup
Key Terminology
Design Rule Checks
Best Practice Paper
Licensing
Embedded Component Design is available in both the PCB Editor and Package/SiP tools. Under the new licensing scheme for 16.5,
the "Miniaturization" product option is selected.
Front to Back Flow Support
The overall functionality associated with Embedded Component Design is largely contained in the back end physical products.
However, the primary method that enables a component to be an embedded candidate is driven from a component definition or
instance level property called EMBEDDED_PLACEMENT. This property can be applied at the schematic level with values of Required
or Optional, thus enforcing the front-to-back flow restrictions you may want to impose on your design process. Alternatively, it can be
applied with the physical back-end editors.
Setup
To setup your board file for supporting embedded components, choose Setup - Embedded Layer Setup
The embedded layer setup form controls the layer(s) to be used for embedded placement, Component direction of Body Up or Body
Down, attachment methods of Direct or Indirect and associated global parameters.
Key Terminology
Direct Attach The manufacturing technology where the components are soldered directly to an internal layer. One
way to visualize this is to think of assembling a traditional PCB with the components on the external
surface(s) and then laminating more layers on top of the
Product Version 16.5 May 2011
Allegro PCB Editor: What's New in Release 16.5
Product Version 16.5
May 2011
This document describes new features in the current and previous releases of Allegro PCB Editor. Significant enhancements have
been made in the following areas:
Embedded Component Design
Graphical User Interface
Etch Edit Enhancements
Intelligent PDF Output
Associative Dimensioning
Design for Manufacturing
DRC Updates
ECAD-MCAD Flow
Database and Misc Enhancements
RF PCB Enhancements
To view the latest updates on hardware and software requirements, see the Allegro Platform System Requirements. Also refer to the
Migration Guide for Allegro Platform Products, Product Version 16.5.
Embedded Component Design
With increased market demands for smaller and lighter products, improved performance and higher speeds, it may become
necessary to consider the embedding of passive or even active components within the inner substrates of the PCB. If you are
designing product that essentially can be held in your hand, perhaps ones used in mobile applications or a consumer electronic
device like a digital camera, embedded component technology may be in your product roadmap plans. The methods on how
components are mounted and logically connected to the formation of cavities may differ from vendor to vendor. The Allegro Marketing
and R&D teams have done its best to provide a robust solution that can accommodate the vast options you may encounter in the
industry. As always, our best advice for advanced PCB Design whether that be HDI, Flex or Embedded is to work closely with your
Fabricator who may also own the Allegro tools. They can advise on the proper parameter and constraint settings that best
accommodate their process flow.
To support embedded components, following enhancements have been done in Allegro PCB Editor.
Licensing
Front to Back Flow Support
Setup
Key Terminology
Design Rule Checks
Best Practice Paper
Licensing
Embedded Component Design is available in both the PCB Editor and Package/SiP tools. Under the new licensing scheme for 16.5,
the "Miniaturization" product option is selected.
Front to Back Flow Support
The overall functionality associated with Embedded Component Design is largely contained in the back end physical products.
However, the primary method that enables a component to be an embedded candidate is driven from a component definition or
instance level property called EMBEDDED_PLACEMENT. This property can be applied at the schematic level with values of Required
or Optional, thus enforcing the front-to-back flow restrictions you may want to impose on your design process. Alternatively, it can be
applied with the physical back-end editors.
Setup
To setup your board file for supporting embedded components, choose Setup - Embedded Layer Setup
The embedded layer setup form controls the layer(s) to be used for embedded placement, Component direction of Body Up or Body
Down, attachment methods of Direct or Indirect and associated global parameters.
Key Terminology
Direct Attach The manufacturing technology where the components are soldered directly to an internal layer. One
way to visualize this is to think of assembling a traditional PCB with the components on the external
surface(s) and then laminating more layers on top of the
Delcam v17.8.1.26 for SolidWorks 2010-2011
Delcam for SolidWorks - Features and Benefits
Features:
Multi-threaded 3-axis toolpath operations
2.5D toolpath creation
3+2 toolpath creation
5-axis simultaneous toolpath creation
Drilling
Turning
Turn/mill
Full machine simulation
Set Up Wizards
Customisable templates
Different styles of feature recognition, including:
Click here to play the video
Watch this video to find out more
about Delcam for SolidWorks'
features and benefits
Automatic Feature Recognition
Simply select the model
Delcam for SolidWorks finds all the features and applies toolpaths automatically
Interactive Feature Recognition
Users specify which feature types are to be recognised
Delcam for SolidWorks finds all the features of the specified type in a single step
SolidWorks Feature Recognition
Toolpaths can be generated directly from SolidWorks feature definitions
Features can be selected graphically or from the SolidWorks Feature Manager tree
Features:
Multi-threaded 3-axis toolpath operations
2.5D toolpath creation
3+2 toolpath creation
5-axis simultaneous toolpath creation
Drilling
Turning
Turn/mill
Full machine simulation
Set Up Wizards
Customisable templates
Different styles of feature recognition, including:
Click here to play the video
Watch this video to find out more
about Delcam for SolidWorks'
features and benefits
Automatic Feature Recognition
Simply select the model
Delcam for SolidWorks finds all the features and applies toolpaths automatically
Interactive Feature Recognition
Users specify which feature types are to be recognised
Delcam for SolidWorks finds all the features of the specified type in a single step
SolidWorks Feature Recognition
Toolpaths can be generated directly from SolidWorks feature definitions
Features can be selected graphically or from the SolidWorks Feature Manager tree
Mentor-Graphics-Precision-RTL-2011a-61-crack
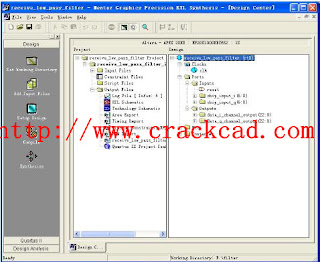
With a rich feature set that includes advanced optimizations, award-winning analysis, and industry-leading language support, Precision RTL enables vendor-independent design, accelerates time to market, eliminates design defects, and delivers superior quality of results.
Key Features & Benefits
FPGA Vendor Independent Synthesis
Support for Actel, Altera, Lattice, and Xilinx
OEM support for Abound Logic, Achronix, Atmel, QuickLogic, and TierLogic
Same HDL and constraints for all devices
Excellent Quality of Results
Meet performance and area goals quickly
Advanced timing-driven optimizations
Technology inference for multiple vendors
Award-Winning-Analysis
RTL and gate-level technology schematics
Interactive static-timing engine to perform"what-if" timing analysis
Industry Leading Language Support
Supports any combination of Verilog, VHDL, SystemVerilog, and EDIF formats
Supports Synopsys Design Constraint
2011-05-11
Agilent-Advanced-Design-System-(ADS)-2011-crack
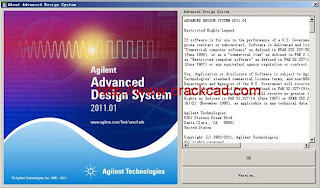
ADS 2011 brings you the following exciting enhancements:
10x speedup in planar 3D electromagnetic simulation
10x speedup in non-linear circuit simulation
Patent pending convolution technology that allows accurate signal integrity simulation with measured S-parameter data of high-speed interconnects
New Simulation Models and Libraries
Further improvement in graphical user interface
The combined benefits of all the above translates to at least a doubling of your design productivity.
10x speedup in planar 3D electromagnetic simulation
The 3D planar EM simulator, Momentum, in ADS 2011 now has at least 10x speed improvement and 6x capacity improvement. This enables you to use electromagnetic simulation as an interactive design tool instead of a sign-off verification tool before hardware prototyping. The high speed of Momentum simulation now allows multiple design explorations to be accomplished easily.
An example of a wireless LAN transceiver simulation where the chip area is minimized by 32% by packing the 11 spiral inductors closer together. This translates to a corresponding 32% reduction in the cost of the 802.11/b transceiver RFIC.
The simulation took just 2.3 minutes with 650MB of RAM as compared to 38 minutes with 1.2GB of RAM in earlier versions of Momentum. This 15x speed improvement allows for interactive placement of the inductors with their proximity effects analyzed very quickly achieving the overall 32% die size reduction.
10x speedup in non-linear circuit simulation
The already powerful harmonic balance simulator in ADS just received additional algorithmic enhancements from Agilent EEsof’s recent acquisition of Xpedion GoldenGate, who has the world’s fastest and highest capacity harmonic balance simulator. Now the harmonic balance simulator in ADS 2009 update 1 can handle bigger circuits and solve them 10x faster. For example, a large RFIC with over 2000 nonlinear elements and over 2000 large signal sources is solved within 250 seconds as compared to 2,485 seconds in the previous versions. The speed and capacity improvements are especially important for fast optimization of large RF-System-In-Package (SIP), MMIC and RFIC to meet higher levels of integration and performance demanded by consumer wireless electronics today.
New Simulation Models and Libraries
The following new models and libraries are now in ADS2011:
PSP and HiSIM transistor models for accurate nano-scale (30nm, 45nm) RFIC simulation
Triquint TOM4 latest III-IV FET model optimized for PHEMT technologies to accurately model highly non-linear behavior
Models for gigabit serial link signal integrity analysis:
HSPICE W-elements
IBIS switches
Verilog AMS
De-embedding element for easy removal of test fixture effects
Impulse response model writer
CODE-V10.2-CRACK
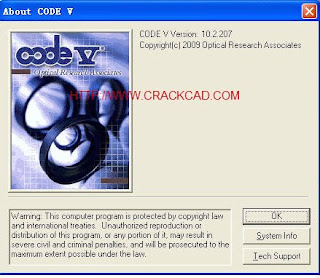
CODE V has been at the forefront of optical design and analysis software innovations, with continual improvements to keep pace with optical industry demands. It is the preferred tool of numerous companies, government agencies, research labs, and universities worldwide. CODE V inspires this loyalty because it reliably produces better optical designs in less time – designs that are often cheaper to fabricate than those produced with other software. With a customizable Windows-based user interface, extensive help features, and excellent technical support to back it up, CODE V is also easy to learn and use.
CODE V Enables Faster Time to Market
CODE V’s flexible user interface, faster algorithms, intelligent defaults, and features to support the manufacturing process all help you develop and assemble the best design faster.
User-friendly interface with customizable data display and navigation features that allow you to adapt the workspace to your workflow and reduce design steps.
Integrated command line enables you to expedite design steps by freely mixing commands and mouse operations.
A fully functional macro capability that provides a powerful tool for enabling complex analyses to be run with an easy-to-use script.
COM interface for automating tasks and leveraging other COM-enabled applications to achieve an integrated, multi-application engineering environment.
New lens wizard to jump start model creation.
Supplied example systems and patent lens search.
Off-the-shelf components.
Built-in prisms models.
Black-box lens modules.
Built-in glass catalogs, including IR/UV materials.
User-programmable features support for surface shape, surface properties, and others.
The fastest design optimization capability in the industry.
Tolerancing and fabrication support features that solve production problems before your design reaches manufacturing.
Mastercam-X5- MU1-crack
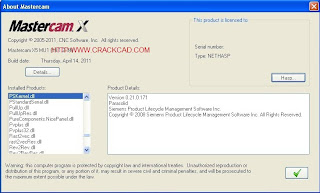
Mastercam X5 MU1 is Released
View the "What's New in Mastercam X5" PDF file
View Mastercam archive videos
Detailed list of new additions since the release of Mastercam X
This maintenance update is available at no charge to all current Mastercam maintenance customers, and can be downloaded here.
The updates and new tools available in Mastercam X5 MU1 include:
Mill:
Enhanced collision checking and containment options for 3D HST toolpaths.
Improved Curve 5-axis and Swarf 5-axis cutting, allowing overlap.
Faster Mill tree-style dialog performance.
Router:
Drag and drop parts from one sheet to another during geometry or toolpath nesting.
Output block drilling parameters for easy use on setup sheets and with certain point-to-point routers.
Wire:
Enhanced 4-axis Direct wirepath accommodates a new suite of geometry and outputs even smoother motion.
Improved functionality give you even more precision tab control.
CAD Tools:
Updated file translators for ACIS, CATIA, SolidWorks, Solid Edge, Unigraphics and Rhino.
Easier surface curve selection and solid layout functions.
With the release of Mastercam X5 MU1, we're also introducing Mastercam Port Expert, a new purchasable add-on designed for the head porting industry. This powerful tool can be added on to Mastercam Mill Level 3 or Router Pro, and delivers:
Intelligent, specialized programming that machines as far as possible into the port with 3-axis toolpaths before switching smoothly to 5-axis motion.
Advanced collision detection to help ensure high-quality cuts.
Flexible machining definition and constraints, allowing automatic or manual choices.
ESI PAM-Stamp 2G 2011
Version: 2011.0
OS supported: Windows 32-bit, Windows 64-bit
Languages supported: English only
PAM-STAMP 2G is a complete, integrated, scalable and streamlined stamping solution. It covers the entire tooling process from quotation and die design through formability and try-out validation, including springback prediction and correction. It provides solutions-oriented tools for Automotive, Aerospace, and General stamping processes.
PAM-STAMP 2G allows users to make decisions online, bringing together the design engineer, the material provider, the die designer and the try-out press shop from an early stage of the design right through to production. This web-enabled technology allows images, annotation, text and 3D, models to be shared, thus supporting a truly collaborative engineering environment.
OS supported: Windows 32-bit, Windows 64-bit
Languages supported: English only
PAM-STAMP 2G is a complete, integrated, scalable and streamlined stamping solution. It covers the entire tooling process from quotation and die design through formability and try-out validation, including springback prediction and correction. It provides solutions-oriented tools for Automotive, Aerospace, and General stamping processes.
PAM-STAMP 2G allows users to make decisions online, bringing together the design engineer, the material provider, the die designer and the try-out press shop from an early stage of the design right through to production. This web-enabled technology allows images, annotation, text and 3D, models to be shared, thus supporting a truly collaborative engineering environment.
2011-03-24
ETA Dynaform 5.8
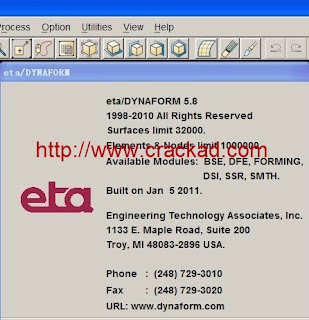
As tough market competition demands faster cycle times, lower software costs and lower user qualification thresholds, Engineering Technology Associates, Inc. (ETA) has developed a new tool, the INC Solver, to address these needs. The solver is included in DYNAFORM 5.7.3, released today.
To expaBody Side Simulationnd the usability of DYNAFORM’s Die Face Engineering (DFE) module, INC is a finite element analysis (FEA) solver designed for sheet metal forming simulations. It provides a value solution for customers who are looking for rapid die design and a virtual tryout tool that generates quick results, is easy to master, but does not sacrifice accuracy.
Tagged at “Best Practice” within INC, the solution pre-populates a set of default parameters produce accurate results. This feature provides a guided
process for inexperienced users; while more advanced users can adjust these default parameters to their preferences. Also, INC Solver requires very few manipulations overall to simulate a typical 3-piece draw analysis.
For die face design virtual tryout, the solver offers capabilities for simulating gravity-loading, binder-wrap, crash-form, single-action and double-action draw die, as well as springback prediction and lancing operations. INC solver supports non-conforming CAD surfaces and its fusion-fission approach handles mesh adaptivity effectively.
INC takes advantage of Intel’s latest multiple-core computing platform to make computing very affordable. For example, a 4-Core system costing under $1500 can process the most complicated large bodyside panel simulation in less than 50 minutes.
In addition to DFE, DYNAFORM includes three other modules, including DYNAFORM includes three other modules, including Blank Size Engineering (BSE), LS-DYNA-based Formability Simulation (FS) and LS-DYNA-based Die System Analysis (DSA). DYNAFORM is a complete die system simulation solution which allows organizations to bypass soft tooling, reducing overall tryout time, lowering costs, increasing productivity and providing confidence in die system design.
2011-03-11
Ixiacom_IxChariot_7.5_crack
xChariot is the industry's leading test tool for simulating real-world applications to predict device and system performance under realistic load conditions. Comprised of the IxChariot Console, Performance Endpoints and IxProfile, the IxChariot product family offers thorough network performance assessment and device testing by simulating hundreds of protocols across thousands of network endpoints. IxChariot provides the ability to confidently assess the performance characteristics of any application running on wired and wireless networks
Features
* Over 150 application scripts simulating Enterprise, Triple-Play and Internet traffic
* Real-world application behavior at the transport layer (Layer 4)
* Creation of separate control and data-plane activity using Application Groups.
* Tailored scripting capabilities using IxProfile and IxChariot's SDK
* Create sophisticated traffic patterns with and without QoS for IPv4 and IPv6
* Measure throughput, jitter, packet loss, end-to-end delay, MOS and MDI
* Seamless correlation of IP stats with 802.11 client statistics such as RSSI
* Measure the impact of new technologies such as VoIP, IPv6, and multicast video
* Embed custom payloads to test specific data content across the network
* Troubleshoot critical performance issues on network segments and devices
* Measure IPTV channel 'zap' times
* Test high BDP networks such as satellite links and 10 Gigabit Ethernet
* Leverage Ixia's hardware test platform to create wire-speed Layer 2-3 traffic running in conjunction with application traffic patterns created by IxChariot®
Features
* Over 150 application scripts simulating Enterprise, Triple-Play and Internet traffic
* Real-world application behavior at the transport layer (Layer 4)
* Creation of separate control and data-plane activity using Application Groups.
* Tailored scripting capabilities using IxProfile and IxChariot's SDK
* Create sophisticated traffic patterns with and without QoS for IPv4 and IPv6
* Measure throughput, jitter, packet loss, end-to-end delay, MOS and MDI
* Seamless correlation of IP stats with 802.11 client statistics such as RSSI
* Measure the impact of new technologies such as VoIP, IPv6, and multicast video
* Embed custom payloads to test specific data content across the network
* Troubleshoot critical performance issues on network segments and devices
* Measure IPTV channel 'zap' times
* Test high BDP networks such as satellite links and 10 Gigabit Ethernet
* Leverage Ixia's hardware test platform to create wire-speed Layer 2-3 traffic running in conjunction with application traffic patterns created by IxChariot®
Zuken_CR5000_Board_Designer_v12_download
Zuken's CR-5000 Board Designer provides an intuitive, integrated environment for designing PCBs, BGAs and MCMs. It serves to guide the user, via a common user interface, from schematic capture through to floorplanning, placement and routing, analysis and into manufacturing. It operates seamlessly across Unix and Windows platforms combining the functionality of a high-end tool with ease of use. While rules are constant throughout the design process, they are dynamically linked to ensure flexibility and consistency.
Benefits
* A single, intuitive environment with a coherent approach throughout the design process, easy links between tools, and a common database and libraries
* Rules-driven design for correct-by-construction outcomes
* An optimized combination of automatic, semi-automatic, and interactive functionality to maximize design productivity
* Design partitioning facilitates intelligent, concurrent engineering; especially useful for large or complex products and for the re-use of proven circuits
* Re-use of proven circuit blocks saves time
Fast and reliable design process
CR-5000 enables the right-first-time design of electronics products through a constraints-driven design process. From design to manufacturing data preparation, PCB integrity is maintained by concurrent design and verification, with co-simulation of both analog and digital functional blocks and programmable devices, signal integrity, power integrity, and EMC optimization. Proven DFM techniques are applied in parallel to the design process.
Migration preserves legacy data
Migrating to CR-5000 from Cadence Allegro and OrCAD, Mentor Graphics Expedition, Board Station and PADS, or Altium Designer is simple. Users can move all the data to CR-5000 from previous designs, re-using symbols, footprints and other supporting design data, and benefit from the ability to re-work legacy designs and component libraries.
Benefits
* A single, intuitive environment with a coherent approach throughout the design process, easy links between tools, and a common database and libraries
* Rules-driven design for correct-by-construction outcomes
* An optimized combination of automatic, semi-automatic, and interactive functionality to maximize design productivity
* Design partitioning facilitates intelligent, concurrent engineering; especially useful for large or complex products and for the re-use of proven circuits
* Re-use of proven circuit blocks saves time
Fast and reliable design process
CR-5000 enables the right-first-time design of electronics products through a constraints-driven design process. From design to manufacturing data preparation, PCB integrity is maintained by concurrent design and verification, with co-simulation of both analog and digital functional blocks and programmable devices, signal integrity, power integrity, and EMC optimization. Proven DFM techniques are applied in parallel to the design process.
Migration preserves legacy data
Migrating to CR-5000 from Cadence Allegro and OrCAD, Mentor Graphics Expedition, Board Station and PADS, or Altium Designer is simple. Users can move all the data to CR-5000 from previous designs, re-using symbols, footprints and other supporting design data, and benefit from the ability to re-work legacy designs and component libraries.
ANSA-V13.1-BETA-CAE-download
Main new features introduced
* Visibility control with the new NEAR function
* Connections Manager: new options in several FE-Representations
* Handling of tailored-blank parts by the SKIN function
* Jacobian criterion calculation methods
* OpenFOAM quality criteria: non-orthogonality and Warping (Face Flatness)
* New 'Growth ratio' quality criterion
* Mesh quality improvement for Jacobian on 2nd order shells and solids:
o corner and mid nodes are moved
o controlled by the Mesh Parameters (Freeze volume skin, Fix quality allow distance values)
* Support of solid elements in IDEAS-V universal format
* Hexa Block meshing enhancements
* Kinematics tool:
o drawing mode per Kinematic Rigid Body
o Explode view
* NX NASTRAN: Support of CPYRAM pyramid solid element
* Abaqus: New supported keywords
* PAM-CRASH: updates and numerous new keywords support for v2010
* PERMAS: New dependency errors detection function and new keywords support
* Enhancements in ANSA - TOSCA Environment
* Scripting language extensions
and more...
* Visibility control with the new NEAR function
* Connections Manager: new options in several FE-Representations
* Handling of tailored-blank parts by the SKIN function
* Jacobian criterion calculation methods
* OpenFOAM quality criteria: non-orthogonality and Warping (Face Flatness)
* New 'Growth ratio' quality criterion
* Mesh quality improvement for Jacobian on 2nd order shells and solids:
o corner and mid nodes are moved
o controlled by the Mesh Parameters (Freeze volume skin, Fix quality allow distance values)
* Support of solid elements in IDEAS-V universal format
* Hexa Block meshing enhancements
* Kinematics tool:
o drawing mode per Kinematic Rigid Body
o Explode view
* NX NASTRAN: Support of CPYRAM pyramid solid element
* Abaqus: New supported keywords
* PAM-CRASH: updates and numerous new keywords support for v2010
* PERMAS: New dependency errors detection function and new keywords support
* Enhancements in ANSA - TOSCA Environment
* Scripting language extensions
and more...
CAMWORKS 2011_FOR_SOLIDWORKS2011
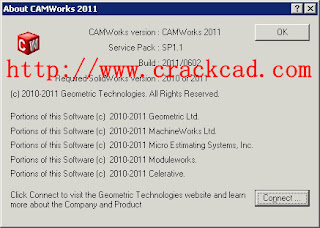
CAMWorks 2011 is an intuitive solids‐based CAM solution that helps manufacturers increase productivity and profitability through best‐in‐class technologies
and adaptable automation tools that maximize machining efficiencies. It is simple to use and eliminates the drudgery of CNC programming with Intelligent
Machining through automation.
CAMWorks 2011 is an intuitive solids‐based CAM solution that helps manufacturers increase productivity and profitability through best‐in‐class technologies
and adaptable automation tools that maximize machining efficiencies. It is simple to use and eliminates the drudgery of CNC programming with Intelligent
Machining through automation.
CAMWorks® uses the familiar SolidWorks® interface, so it is easy to learn and easy to use. The CAMWorks trees are similar to the SolidWorks FeatureManager design tree. Items in the tree can be suppressed, expanded, renamed and moved using the same procedures as SolidWorks. Online help, Installation and Quick Start Guide and tutorials can help you generate toolpaths and code quickly. The tutorials are provided electronically in Adobe PDF files.
Minimize Efforts
CAMWorks is a feature-based CAM system that provides the ability to automatically recognize many machinable features. Automatic Feature Recognition (AFR) analyzes the solid model geometry and identifies mill features such as holes, slots, pockets, and bosses; turning features such as outside diameters, faces, grooves and cutoffs; and wire EDM features such as die openings. AFR recognizes features regardless of the CAD system in which they were created.
Features that cannot be found automatically or that need to be defined for your specific machining requirements can be defined effortlessly using the Interactive Feature Recognition (IFR) wizard.
After machinable features have been defined, the user can take advantage of the machining automation in CAMWorks to generate operations. Machining operations include roughing, finishing, drilling, etc. Operations are associated to machinable features.
Automate and Control intelligently
CAMWorks defines areas to be machined as features, then applies automation and intelligence to generate toolpathsGeometric Technologies (A division of Geometric Americas Inc.)' innovative TechDB™ (Technology Database) is designed to significantly reduce the time required to generate machining strategies and processes. Using knowledge-based machining technology, the database associates tooling, operation strategies and machining parameters to the features. When operations are generated, CAMWorks applies these settings automatically. To further enhance the automation process, the knowledge-based rules in the TechDB are fully customizable to apply your company’s best practices. While CAMWorks promotes saving time through automation, at any time in the process full interactive manual control is available at your fingertips.
Esi_procast_2010.4_download
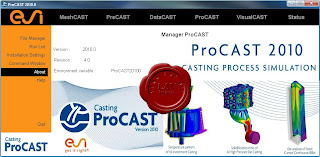
he leading Finite Element solution for casting process simulation
Throughout the manufacturing industry, casting process simulation is now widely accepted as an important tool in product design and process development to improve yield and casting quality.
Based on powerful Finite Element solvers and advanced specific options developed with leading research institutes and industries, ProCAST provides an efficient and accurate solution to meet the casting industry needs. Compared to a traditional trial-and-error approach, ProCAST is the key solution to reduce manufacturing costs, shorten lead times for mold developments and improve the casting process quality.
ProCAST provides a complete software solution allowing for predictive evaluations of the entire casting process including mold filling, solidification, microstructure and thermo-mechanical simulations. It enables to rapidly visualize the effects of mold design and allows for correct decision making at an early stage of the manufacturing process.
Subscribe to:
Posts (Atom)