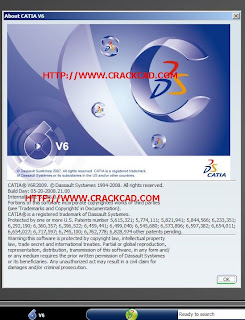
Dassault Systèmes (DS) (Euronext Paris: #13065, DSY.PA), a world leader in 3D and Product Lifecycle Management (PLM) solutions, today launched V6R2009x, the latest release of its new platform. Release 2009x demonstrates the continuing momentum of the V6 portfolio and its production proven online collaborative platform. Today’s announcement further substantiates PLM 2.0 – PLM Online for All.
“From leveraging online communities, such as 3DVIA.com, to integrated requirement, functional, logical, and physical definitions of products, the V6 platform is harnessing the collective intelligence of all participants in a product’s lifecycle,” said Dominique Florack, senior executive vice president, products, research and development, Dassault Systèmes. “V6R2009x delivers key functionality, such as compliance capabilities for environmental and FDA regulations, and a new BOM configuration solution to manage product unit effectivity.”
Today’s release delivers important industry-specific solutions for customers in the consumer goods, high-tech, industrial equipment, life sciences, automotive, and aerospace industries. Numerous companies are already experiencing the potential of V6, including Skanska in the architecture industry, Procter & Gamble in consumer packaged goods, Nikon in high tech, Pacific Brands in apparel, Hoffman Enclosures and Schuler in industrial equipment, Johnson Controls and novero in automotive, Piaggio in aerospace, and others.
“We believe innovation is the result of collaboration, and we’ve found CATIA V6 strongly embodies this philosophy,” said Ken Moro, Executive Staff, Industrial Design Dept. Imaging Company, Nikon Corporation. “From what we’ve seen in our preliminary experiences with CATIA V6, Dassault Systèmes has put the values of collaboration and innovation at the core of its online design solution. Global collaborative innovation is a driving force in today’s markets and we expect that it would contribute to our global design.”
As with the previous release of V6, Release 2009x is designed to extend the value of customers’ existing PLM assets. Dassault Systèmes continues to develop and make available transition scenarios for its varied user base, including customers with mixed DS and non-DS applications. Support for collaborative design scenarios between V4/V5 and V6 enables gradual adoption of V6 for an OEM and its supply chain. Further, DS plans additional releases of its popular V5 line of solutions, such as the recently announced V5R19, whose functionality enhancements are synchronized with and available in V6R2009x.
V6R2009x New & Enhanced Solution Highlights
Lifelike Experience – 3DVIA V6 applications are designed to deliver highly realistic or “lifelike” experiences online, thereby enabling new classes of users to imagine, interact and engage with 3D content in new ways. V6R2009x and 3DVIA Composer enable new communities of users in customer service, technical training and maintenance operations to leverage their company’s strategic PLM investments and reuse this information to create compelling 3D-based composite documents for all types of products. This now includes functional tolerancing and annotation (FT&A) data, all directly accessed from V6 solutions without requiring reverse engineering.
Collaborative Innovation – ENOVIA V6 provides an open, online collaborative environment, on a single IP management platform, for all product lifecycle activities. It federates all product-related knowledge no matter where it resides. V6R2009x introduces a new configuration management solution which supports product unit effectivity for aerospace manufacturers, as well as a host of new ENOVIA solutions for various sectors, such as CPG, retail, footwear and apparel, life sciences and industries concerned with REACH, RoHS, and FDA regulatory compliance.
Virtual Design – CATIA V6 enables the full spectrum of next generation collaborative virtual design, including shape design, mechanical and equipment engineering, as well as systems engineering integrating requirement, functional, logical and physical product definitions. V6R2009x’s new enhancements include advanced systems simulation within the 3D digital mockup, the “design anywhere, anytime” ability to capture and send intended design changes to offline collaborators, as well as “grid” and “solid” composites design approaches for optimized design and mating with non-composite structural parts.
Realistic Simulation – SIMULIA V6 provides industry communities, from designers to simulation specialists, with a unique collaborative environment for performing lifelike simulation and virtual product behavior testing to make well-informed, performance-based decisions. One of this domain’s key V6R2009x enhancements is the ability to leverage composite material lay-ups created within CATIA to simulate the structural behavior of the product design under dynamic loading, helping to predict the onset of buckling and failure.
Digital Manufacturing and Production – DELMIA V6, powered by V6’s single platform for IP management, delivers a collaborative, lifelike digital manufacturing environment for creating and sharing manufacturing IP and optimizing and executing virtual production systems. V6R2009x delivers a fully-integrated automotive body-in-white weld point management solution for easier collaboration between engineering and manufacturing as well as OEMs and their suppliers, a virtual NC machine simulation capability that extends out DELMIA V6’s NC machining portfolio, as well as robotic workcell and related motion path definition