2013-12-31
moldex3d-R12-SP1-download
Moldex3D Products Overview
Moldex3D is the world leading CAE product for the plastics injection molding industry. With the best-in-class analysis technology, Moldex3D can help you simulate the widest application range of injection molding processes to optimize product design and manufacturability, shorten time-to-market, and maximize product ROI.
Features
CAD-Embedded Pre-Processing
Superior Automatic 3D Mesh Engine
High Resolution 3D Mesh Technology
High Performance Parallel Computing
Simplify High-quality Mesh Generation Process
Extends the unrivaled meshing capabilities to offer a very intuitive Boundary Layer Mesh (BLM) generation tool in Moldex3D Designer, giving users who need to prepare advanced analyses a strong boost
Moldex3D CADdoctor Heals Geometrical Problems
Streamlines the model exchange process between CAD and CAE with powerful manual healing functions for maximum flexibility, improving efficiency with faster model repair workflow
Moldex3D Designer BLM Mode and CADdoctor Tutorial
Empower Dynamic Process Capabilities Based on Manufacturing Needs
Compression Molding
Investigates potential defects resulted from heat and pressure, decides appropriate materials, and optimize process conditions. Easily defines compression zones, surfaces, and directions for better production efficiency and enhanced processability
Moldex3D Compression Molding Tutorial
Bi-injection Molding
Assesses the filling pattern of the same plastic material with two colors being injected into a cavity from different gates and predicts welding line locations to enhance the quality of dual-colored products
Powder Injection Molding
Gets accurate at visualizing high-precision and complex metal/ceramic injection molding, helping users predict potential molding defects based on the fluid flow behavior of the feedstock consisted of powder and binder
Moldex3D Powder Injection Molding Tutorial
Strengthen Prediction and Optimization Capabilities through Enhancements
Annealing Process Analysis
Extends simulation calculation to post-molding annealing process, providing a powerful tool to determine processing condition based on the possible annealing method
Co-injection Analysis
Provides users a comprehensive insight into the flow behavior of core materials inside cavities when blow through happens
Core Shift with Two-way (FSI)
Predicts the simulation result of part inserts with two-way FSI method to increase accuracy and improve core deformation
Venting Analysis
Provides trapped air temperature and pressure results
Fiber Analysis
Empowers prediction capabilities on fiber breakage and fiber length distribution results, preventing high shear stress problems
DOE Optimization
Auto Gate Location Function
Identifies the best gate location to achieve flow balance and provide support for single and multiple gate models
Weight Designation of Multiple Quality Factors
Obtains optimal process conditions based on different weighting values of each quality factor
Garrad_Hassan_GH_Bladed_V4.5_tutorial
Bladed provides worldwide wind turbine and component manufacturers, certification agencies, design consultants and research organisations with a design tool that has been extensively validated against measured data from a wide range of turbines. It enables users to conduct the full range of performance and loading calculations. With a Windows-based user interface, it supports calculations of combined wind and wave loading, with full aeroelastic and hydroelastic modelling. It has been validated for the calculation of wind turbine loads for design and certification.
Multibody structural dynamics
Bladed utilises a new, completely self-consistent and rigorous formulation of the structural dynamics. This provides consistently reliable and accurate results and forms a solid foundation from which to continue to extend the structural model with features as part of the ongoing development programme.
Bladed Modules
In addition to the core base module, Bladed has several specialist bolt-on modules covering steady state analysis, dynamic load simulations, analysis of loads and energy capture, batch processing and automated report generation, interaction with the electrical network, and model linearisation for control design. Related information sheets can be downloaded at the bottom right of this page.
Turbine Definition
Turbine Definition
The main toolbar gives access to data entry screens which allow the various turbine components to be defined.
Load Environment
Load Environment
Comprehensive models of complex wind fields, definition models of hydrodynamic forces and an optional seismic module for earthquakes simulations.
Response Calculations
Response Calculations
From blade aerodynamics to power curves: simulations that cover all operational states; flexible control of calculation outputs.
Processing & Reports
Processing & Reports
A powerful post-processing facility to analyse the results of calculations, a graphics facility which allows the user to view results quickly and project management tool to store store and share turbine and calculation definitions.
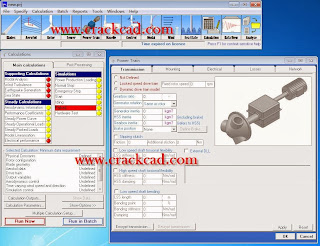
DNV-Nauticus-Hull-2013
Nauticus Hull software
Based on DNV’s strong industry knowledge and expertise, the system provides a highly efficient environment for design and verification. It is a complete structural analysis package, developed by naval architects for naval architects. The system is an important part of the design and verification work for more than 200 users worldwide. High quality technical support and a development strategy based on the latest technology make Nauticus Hull software a safe long-term solution.
Brix Explorer
Brix Explorer is the main entry point to all the Nauticus Hull programs. It organises the work and gives easy access to various templates for typical jobs to be carried out. The user is guided through the relevant tasks and data are gathered in a single database for each job. General information about the ship, such as dimensions, applicable rules, compartment data, loads, etc, is stored in the database and shared by all the programs. The Brix technology will also enable you to build on Nauticus Hull’s pre-defined templates to create your own customised workflows, integrating your best engineering practices.
Benefits of the Nauticus Hull software
Available in different configurations
Uses a common interface across all modules
Intuitive toolbars and design
A complete solution
Nauticus Hull is available in different configurations, from basic Rule Check package to advanced systems for wave load and finite element analyses. For all packages, a common user interface, with intuitive toolbars combined with specialised modelling wizards, minimises the learning period and user threshold. With less time spent on generating models, more time can be spent on essential design-process decisions.
Nauticus Hull covers a wide range of analysis including:
Rule check
High speed light craft
Container securing
3D Beam
Buckling assessment
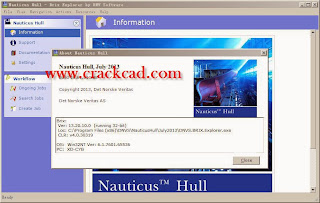
OPTIS-SPEOS-CAA-V5-Based-V15.1-tutorial-license
Especially recommended for a first approach to optical simulation in CAD CAM world.
Non-optics specialists will find it particularly easy to use
This module allows you to create any optical model by applying optical properties to all surfaces, materials and light sources.
After defining the optical mockup, you will be able to visualize the rays as they propagate in the mechanical system.
This module comes complete with intelligent abilities to create interactive simulations where rays are propagated through 'active' components in the 3D view. Moreover the rays are propagated with their wavelength information for further analysis by you. Advanced scattering, anisotropic surface & diffusive material generator are also available.
SPEOS CAA V5 Based Windshield Analysis allows CATIA V5 users to test the compliance of a windshield with ECE R43 and SAE Z26 regulations. It enables the simulation of typical experiments, such as sighting target reflection and transmission.
Moreover it provides optical parameters such as deviation, distortion, refractive power to characterize a given windshield; it also allows users to generate the distortion of an image or a video to find out what the effect of the curvature of the windshield shape will be.
SPEOS CAA V5 Based Windshield Analysis provides windshield manufacturers a powerful engineering tool to improve their development process, to speed up their reactivity and to enhance their support to their customers.
SPEOS CAA V5 Based Windshield Analysis gives car manufacturers a validation tool that can be used at all the stages of the design process saving effort on invalid designs, evaluating the impacts of modification and giving them independence from their suppliers.
OPEN-MIND-hyperMILL-2013-tutorial-download
With new functions for familiar strategies, hyperMILL 2013 steps in to further optimise manufacturing processes in order to realise untapped potential in production and make processes more efficient. Specifically, this means reducing programming and manufacturing times more than ever before and constantly improving surface quality.
hyperMAXX® for 2D pocket milling
The dynamic feedrate adjustment of hyperMAXX® (High Performance Cutting) reduces milling times, increases tool life and prolongs machine life. hyperMAXX® is fully integrated in hyperMILL® and can be opened as an optimisation strategy for 2D pocket milling, 3D arbitrary stock roughing and 5axis shape offset roughing.
Tool life can be tripled
Constant load on tool and machine
Machining operations always with climb milling
No sharp edges or sudden changes in milling direction
No post-processor adjustments required
Benefit: Significantly longer tool life, dramatically reduced machining times.
New “Rib Machining” cycle
OPEN MIND worked together with one of Germany's largest automotive manufacturers to develop the new “Rib Machining” cycle to program negative rib shapes. This feature automatically detects grooves to be milled. Steep areas and floors are machined separately.
Pocket machining and collision avoidance (shaft and tool against stock, trim curve and model) are integrated in the cycle. The system selects a suitable roughing strategy based on the geometric situation at hand. Contiguous areas are completely machined. The cycle supports tapered and conically strengthened tools.
Benefit: Trouble-free programming of negative rib shapes, shorter machining times and a higher level of quality.
Shape offset finishing
Barrel cutter shapes that enable larger infeed are now supported by hyperMILL®.
Benefit: Very short machining times and optimised surface quality.
New, spiral movement sequences enable a constant, continuous infeed.
Benefit: Better surface quality.
Tire module
The module allows the user to easily program tire projects. A special Tire Browser and user interface was developed to create and edit tire definitions. These tire definitions can reach a high level of complexity and account for multiple tracks.
Intelligent automated functions facilitate fast programming of individual pitches or pitches combined in pairs. Automatic segment program generation allows you to trim, sort and link tool paths with collision monitoring. It is possible to automatically generate segment surface geometries trimmed to segment splits. Numerous tire-specific 5axis strategies deliver maximum efficiency when machining tire moulds.
Benefit: Simple interface to external systems; quickly create the tire definition; extremely simple programming of individual pitches; optimised and secure segment programs; significantly reduced programming and machining times.
new verison for hypermill 2014
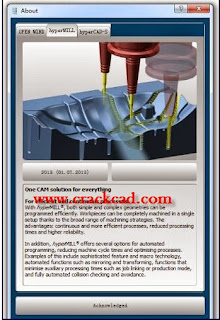
new verison for hypermill 2014
DNV-Sesam-2013-tutorial
Sesam GeniE software
The Sesam GeniE software is a software tool for designing and analyzing offshore and maritime structures made of beams and plates. Modelling, analysis and results processing are performed in the same graphical user interface. The use of concept technology makes the Sesam GeniE software highly efficient for integrating stability, loading, strength assessment and CAD exchange. All data are persistent enabling the engineers to do efficient iterative re-design of a structure.
Sesam GeniE software for:
Fixed structures
The analysis – hydrodynamic as well as strength calculations – and evaluation of results are done within the Sesam GeniE software. The software is built for frequent changes in both structural and equipment layout – any modification performed on a concept level will give an automatic updated and consistent analysis model.
Hydrodynamic design of floating structures
The Sesam HydroD software is a tool for hydrostatic and hydrodynamic analysis. By integrating these tasks, significant cost savings may be achieved in the engineering phase since the same panel model may be used by one tool.
Sesam HydroD software will perform compliance checks against statutory rules for stability including the importance of integrity of the deck tanks. Floating positions may be determined as a result of actual mass and buoyancy or from an automatic compartment filling to satisfy specified position.
The Sesam DeepC software is a tool for mooring and riser design as well marine operations of offshore floating structures. It will perform mooring analysis separately or when including the coupled effects from risers and vessels. Furthermore, Sesam DeepC software may be used for riser design where the risers are analyzed separately or when considering coupling effects. Marine operations may be simulated in the time domain for a study of motions and station keeping of multibody systems.
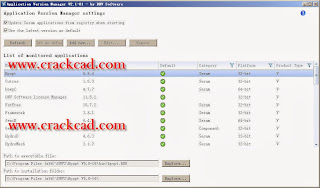
Subscribe to:
Posts (Atom)